I've reached the point in this build where I need a bit more stable platform to set things on as I add them. I didn't want to invest any more time/work until I was sure that I was going to be able to make the crankshaft. Now that it is finished, I will go ahead and build the engine baseplate. This is not going to be an "oil in the base" engine. Oil will be administered from the open top, via squirt can. The milled "catch basin" in the baseplate will catch any oil drips and guide them out thru a drain hole in the front of the baseplate. I will probably put a perimeter gasket between the "engine block" and the baseplate to keep oil from seeping out onto the surface of the baseplate..
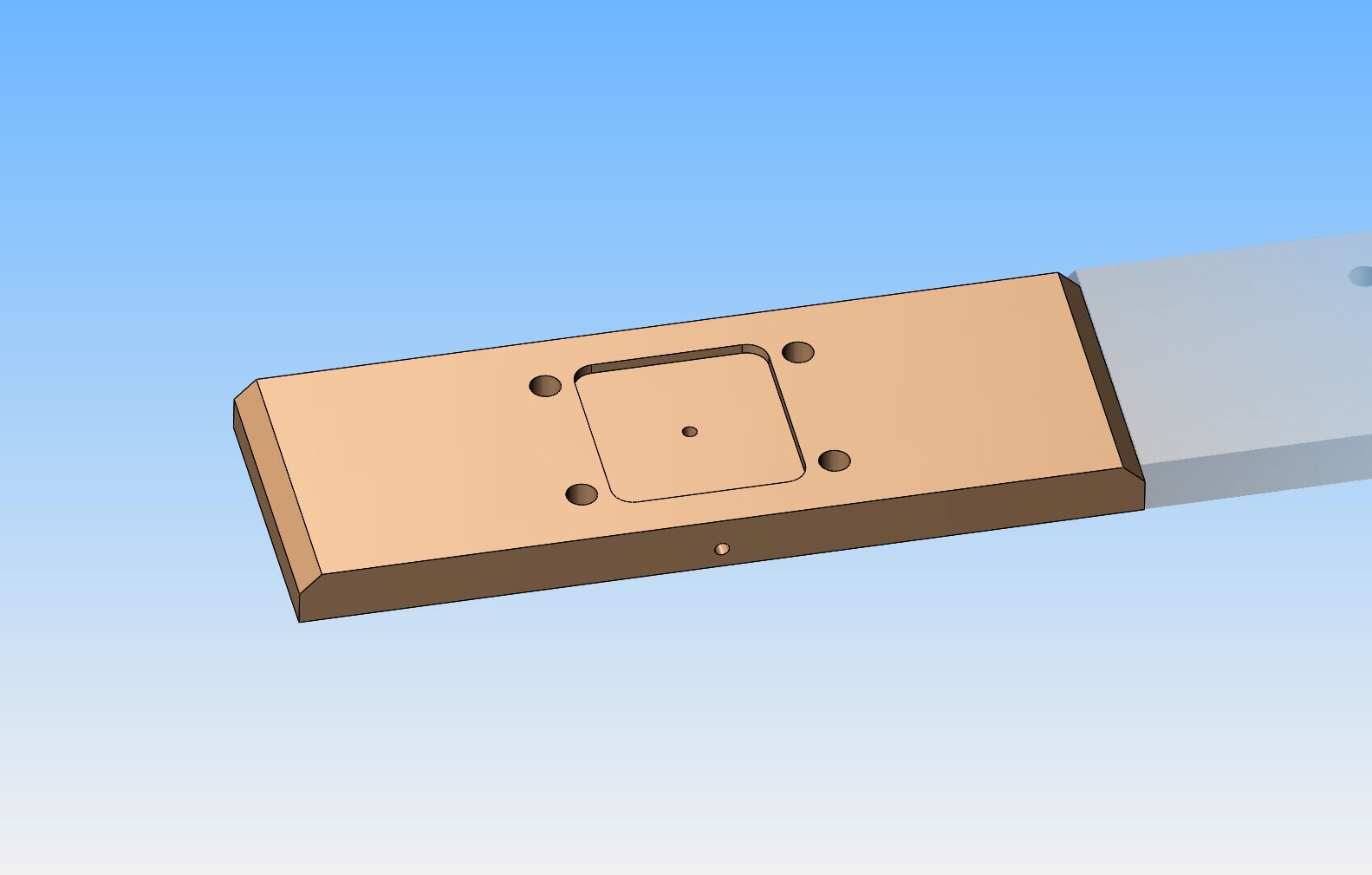