hey there. here are some mods i made to my machines. i have had my mini mill for a year now and have done a mod or two. i have had my mini lathe for a week. here are the mods i have done to each one.
first is my mill. i have added a Z axis "DRO", and added a ball bearing supported shaft for the z axis feed.
here are pix of the upper and lower mounts for the readout. one has side to side adjustment, and the other has up/down adjustment, so i dont have to drill holes in an exact location for it to work.
this mod to the spring shaft lets the readout sit closer to the mill column.
lathe mods:
replaced lame washers with a milled plate to retain half nut gib.
it has a step machined in it so i can tighten the screws and still have the gib be a sliding fit, so the adjustment screws actually work correctly.
before:
after:
a pic of the actual plate.
made swiveling handles for the cross slide and compound.
they are knurled to look cool and have a little grip to them.
next i plan to make some nice handles for my mill and make a carriage lock for the lathe.
first is my mill. i have added a Z axis "DRO", and added a ball bearing supported shaft for the z axis feed.
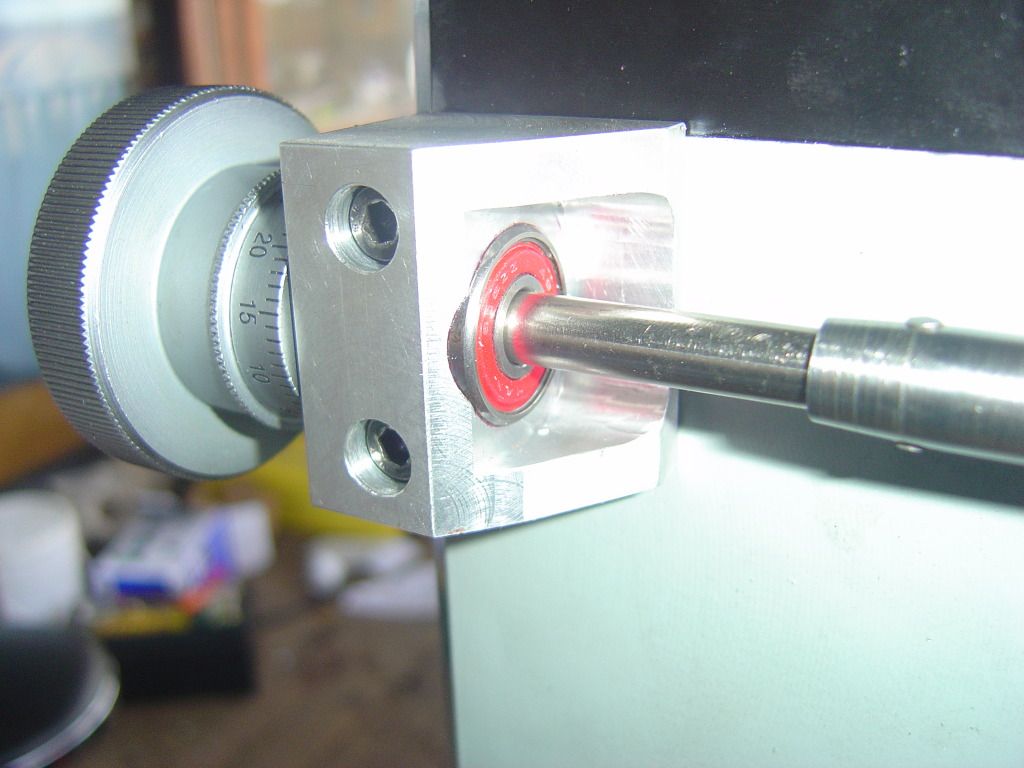
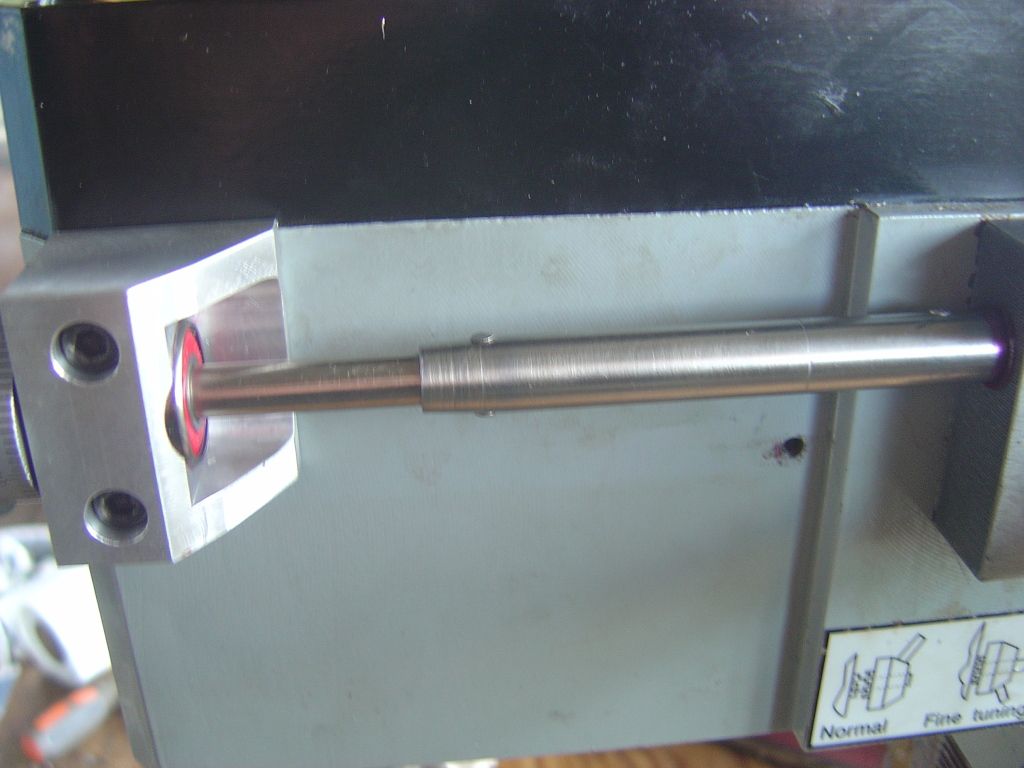

here are pix of the upper and lower mounts for the readout. one has side to side adjustment, and the other has up/down adjustment, so i dont have to drill holes in an exact location for it to work.
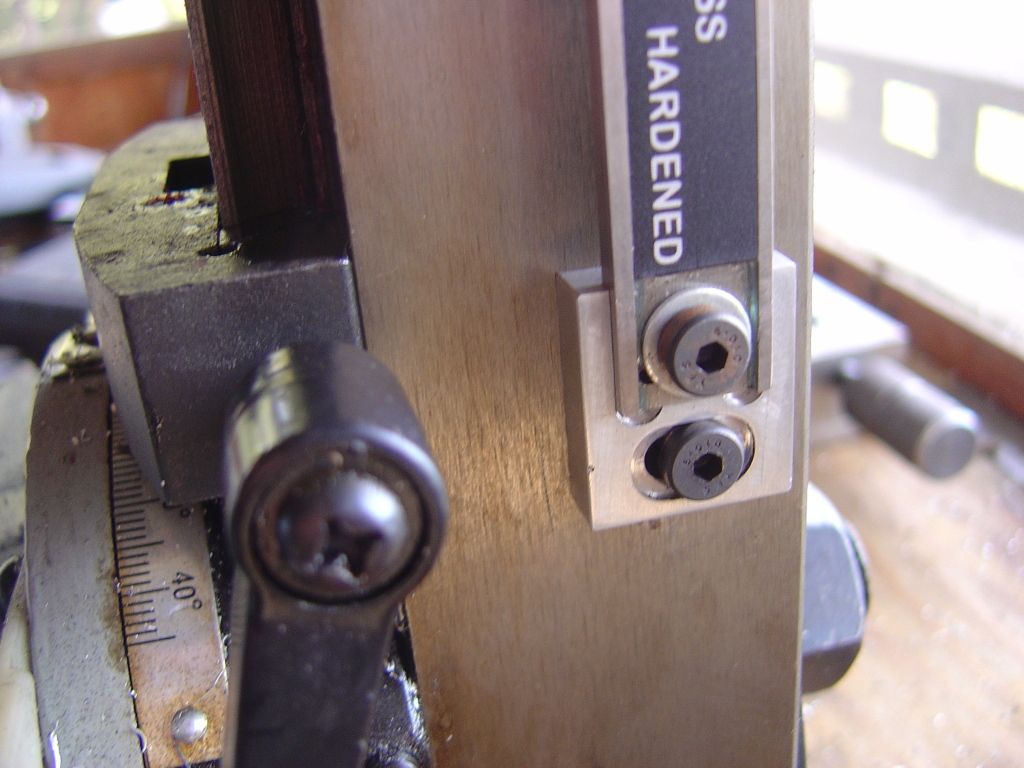
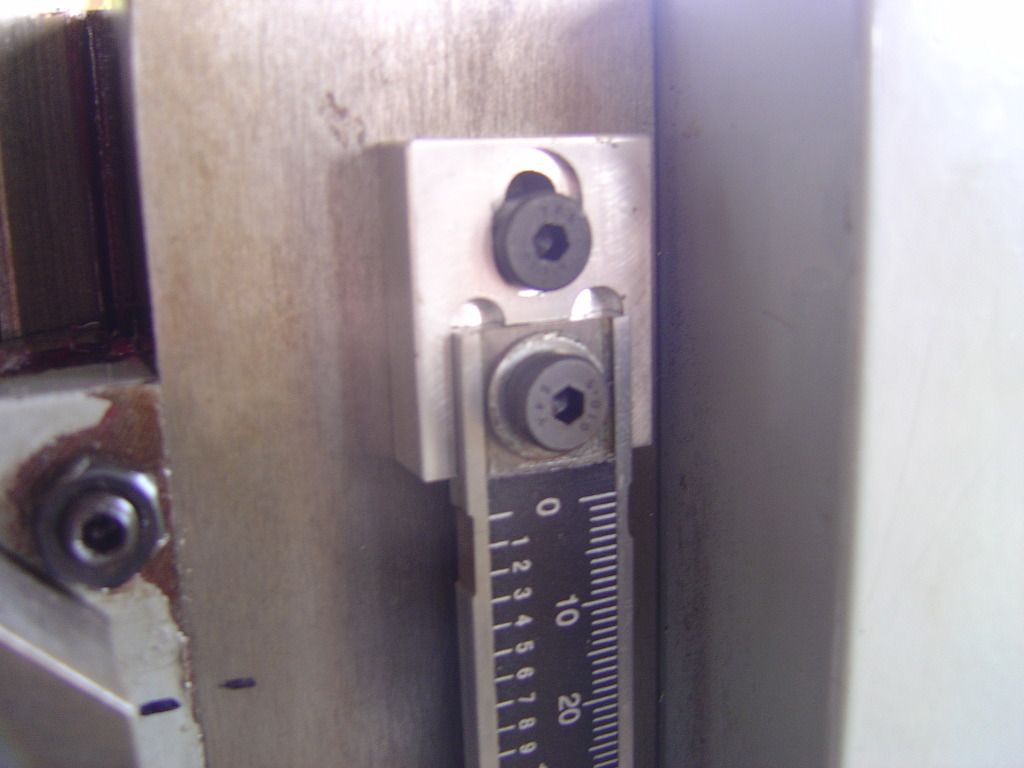
this mod to the spring shaft lets the readout sit closer to the mill column.

lathe mods:
replaced lame washers with a milled plate to retain half nut gib.
it has a step machined in it so i can tighten the screws and still have the gib be a sliding fit, so the adjustment screws actually work correctly.
before:

after:
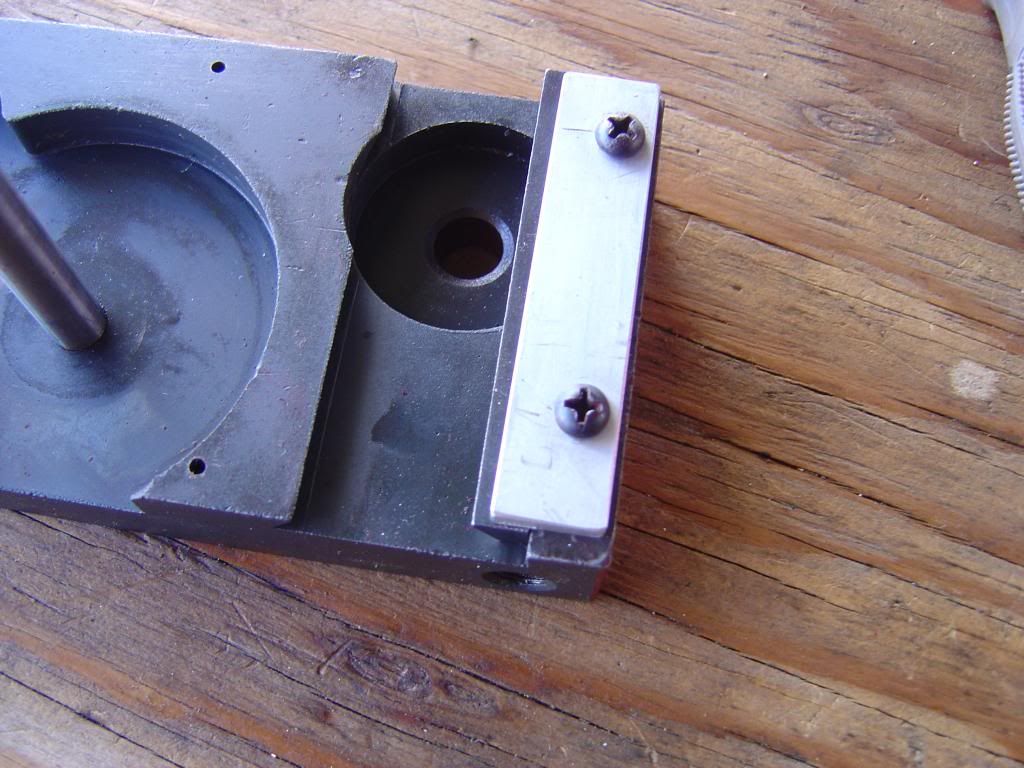
a pic of the actual plate.
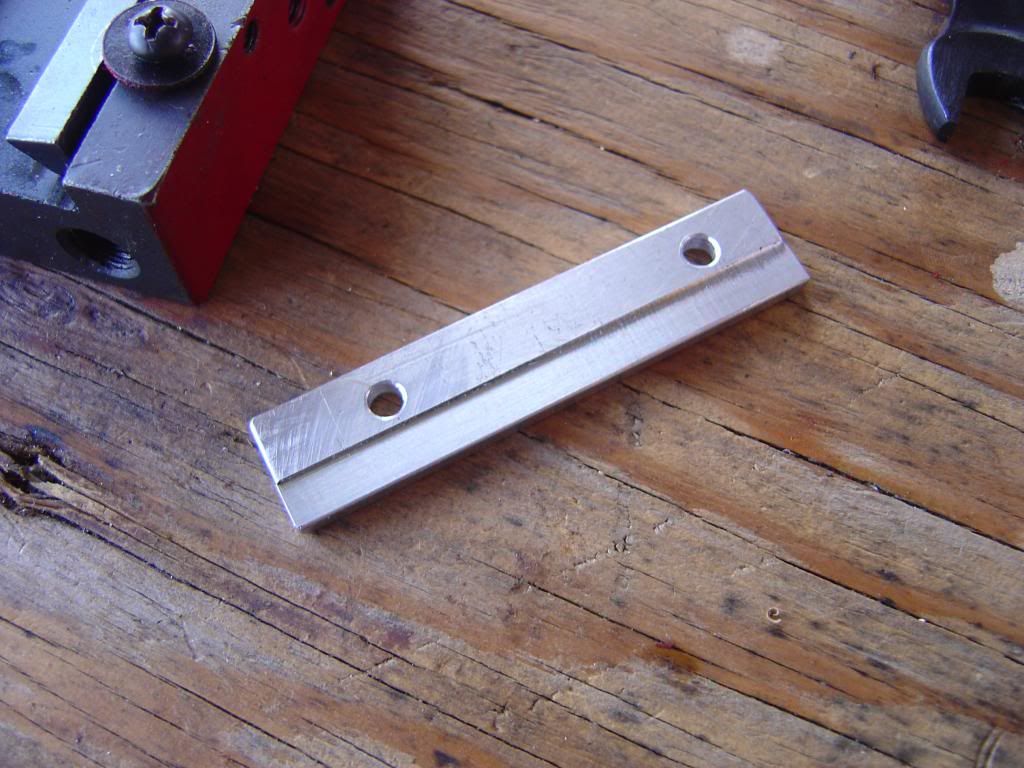
made swiveling handles for the cross slide and compound.
they are knurled to look cool and have a little grip to them.
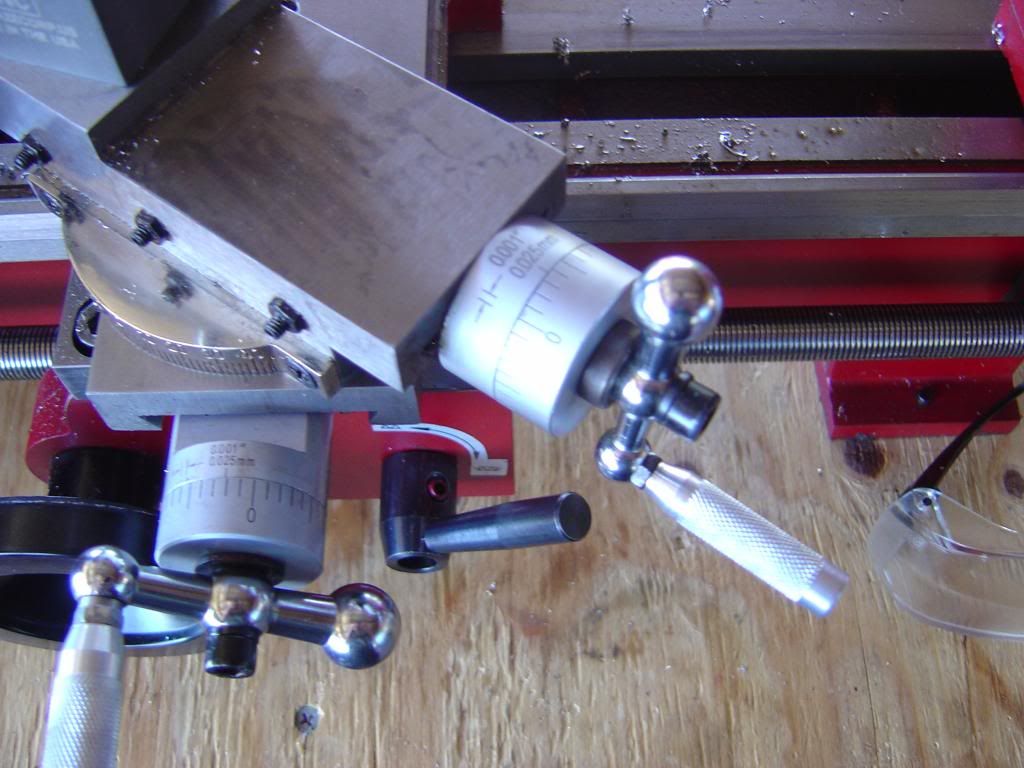
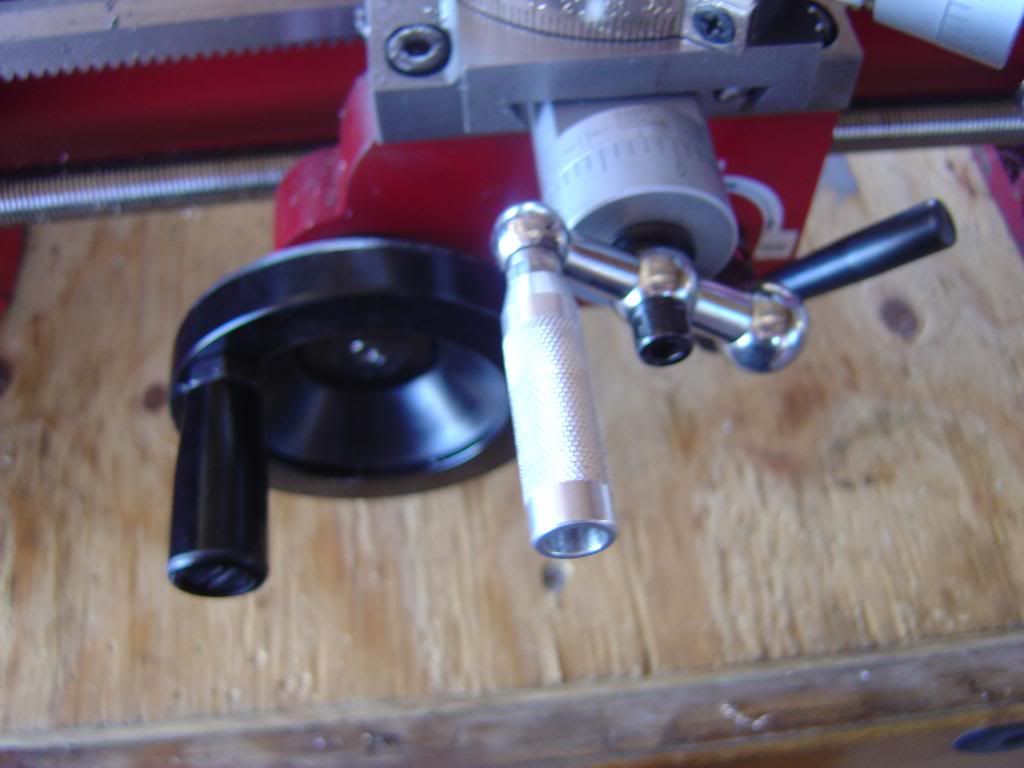

next i plan to make some nice handles for my mill and make a carriage lock for the lathe.