If this part of the forum is to strictly to give advice (as on first look it seems), take this as advice on how not to do what I'm just now learning how to do.
So indulge me mklotz and dsquire - if you will; if anything, the replies I hope to receive would contain some tips and tricks.
The objective is to try my hand at scraping (I'm already proficient at scrapping, thank you - I can scrap work in more ways than one).
Now, I have read what I could online and I am still waiting for books and a DVD I ordered last week... but I was never good at waiting and decided to give it a shot. I will make a small height transfer scriber such as the one Lautard describes in his second book.
The base started it's life as a former flywheel blank.
It'll get scraped flat.
I will show you what I have till now, and then will post a video with the sharpening of the scraper...
The diameter of the stock was 2.375", and from flat to flat is is 1.875" if I recall. This is after a few roughing cycles -- I hope this is the correct amount of blue??. Note the surface. Each stroke leaves little lines, and this is because the cutting edge is not smooth. Mental note to show the chips, they are nice and "curly"... pretty thin though...
IMAGE 1:
This is after an other cycle. Again, just a tad of blue on the surface plate, worked around with the brayer. Would this be flat enuf for a non bearing surface? 4-5 points per square inch?
IMAGE 2:
This is after a couple of more rounds. I was only cutting the areas with the blue...
So indulge me mklotz and dsquire - if you will; if anything, the replies I hope to receive would contain some tips and tricks.
The objective is to try my hand at scraping (I'm already proficient at scrapping, thank you - I can scrap work in more ways than one).
Now, I have read what I could online and I am still waiting for books and a DVD I ordered last week... but I was never good at waiting and decided to give it a shot. I will make a small height transfer scriber such as the one Lautard describes in his second book.
The base started it's life as a former flywheel blank.
It'll get scraped flat.
I will show you what I have till now, and then will post a video with the sharpening of the scraper...
The diameter of the stock was 2.375", and from flat to flat is is 1.875" if I recall. This is after a few roughing cycles -- I hope this is the correct amount of blue??. Note the surface. Each stroke leaves little lines, and this is because the cutting edge is not smooth. Mental note to show the chips, they are nice and "curly"... pretty thin though...
IMAGE 1:
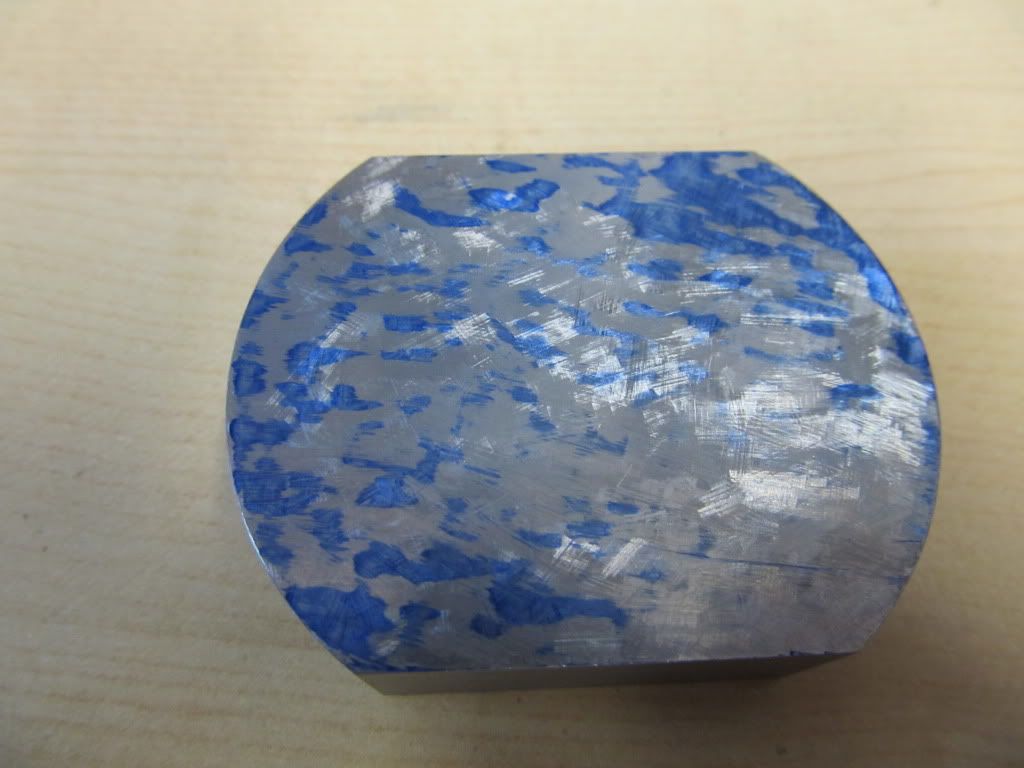
This is after an other cycle. Again, just a tad of blue on the surface plate, worked around with the brayer. Would this be flat enuf for a non bearing surface? 4-5 points per square inch?
IMAGE 2:
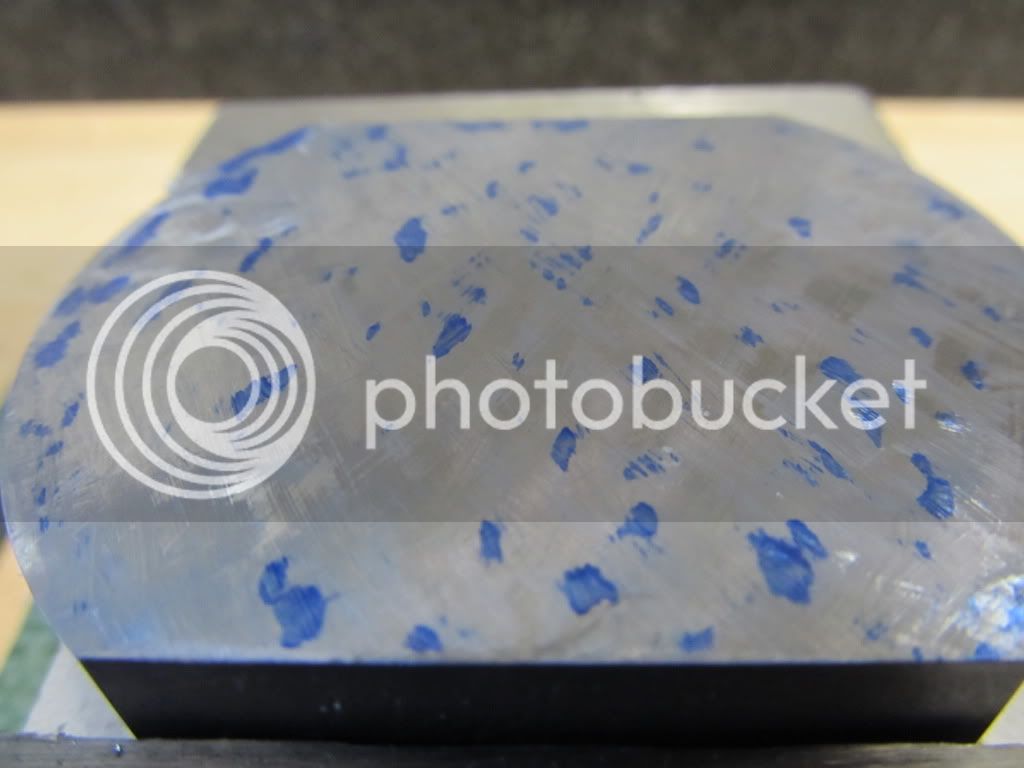
This is after a couple of more rounds. I was only cutting the areas with the blue...
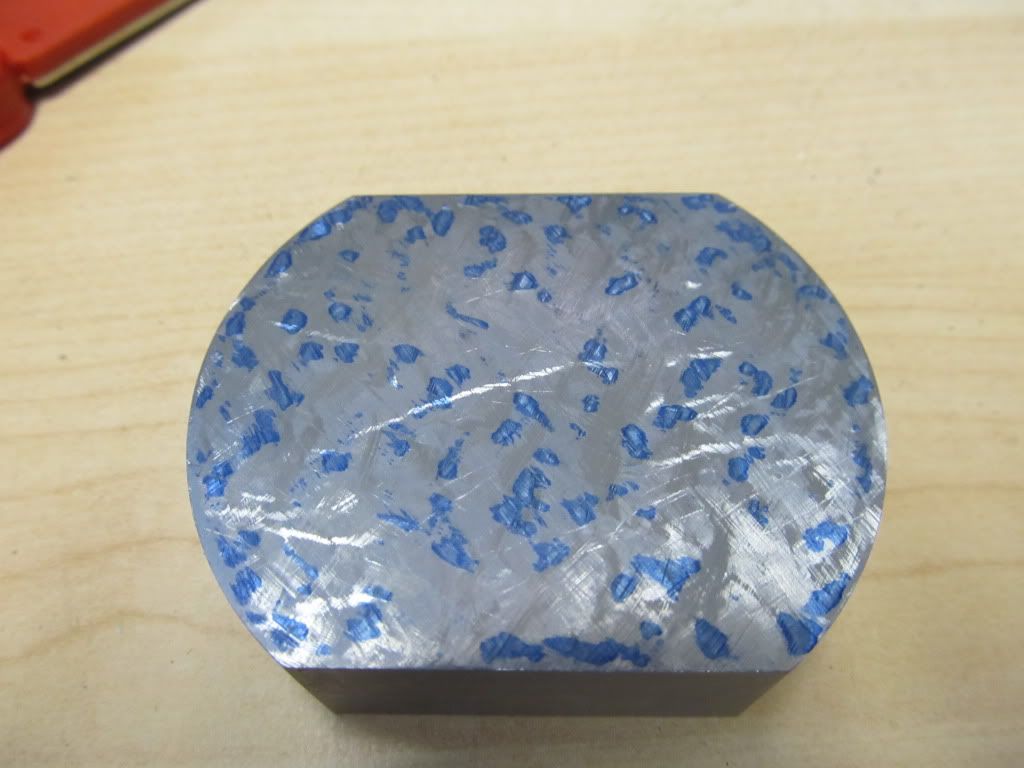