Moving on to the third and almost final grind, I layed the side of the tool which would be opposite the cutting side against the toolrest, and held the tool at approximately 15 degrees to the centerline of the grinding wheel (Same as the picture I posted), and more or less held the visible line which resulted from the second grind on the tool in line with the side of the grinding wheel. Then I kept grinding and checking untill the resulting flat surface just touched the sharp corner at the end of the tool which had resulted from the first two grinds.
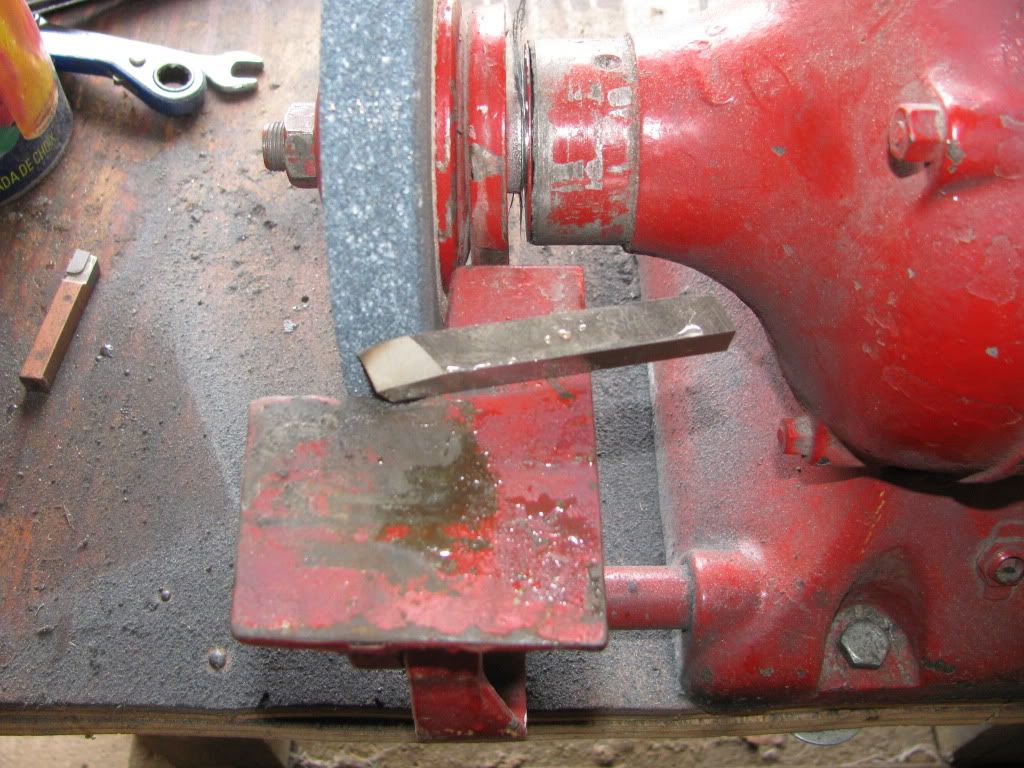