- Joined
- Jan 19, 2010
- Messages
- 1,193
- Reaction score
- 41
I liked the poppin so much I wanted to build another one.
But I thought, lets do it a little different. How about two brass cylinders. Oooh, a double brass poppin, thats what Ill do. ;D
I actually started making the cylinders a couple weeks ago, right before I got my new lathe, so I was a little pre occupied and could not get pics up til now.
Here is what I started with.
Drilling the hole,
Boring the hole, (This is all standard stuff here, nothing exciting)
Marking out the fins with my height guage.
Now, cutting the fins, Brass cuts like a champ, I am always nervous when I use a parting blade, but It seems like with brass you can ram the tool in and all is well.
Here they are.
Kel
But I thought, lets do it a little different. How about two brass cylinders. Oooh, a double brass poppin, thats what Ill do. ;D
I actually started making the cylinders a couple weeks ago, right before I got my new lathe, so I was a little pre occupied and could not get pics up til now.
Here is what I started with.
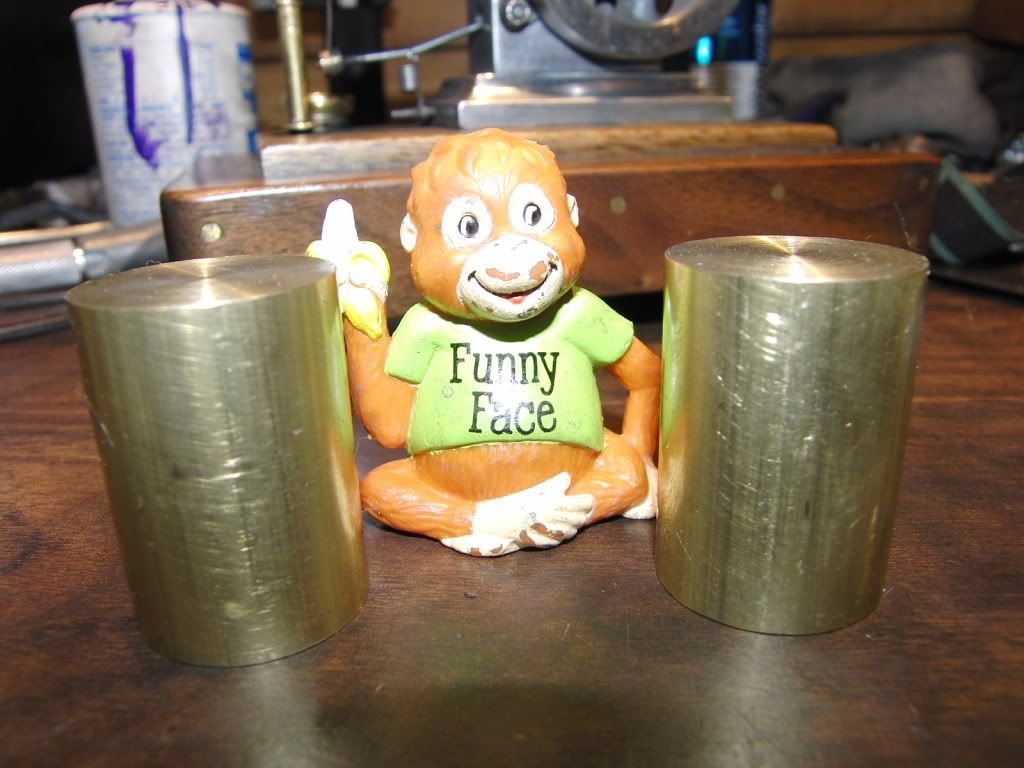
Drilling the hole,
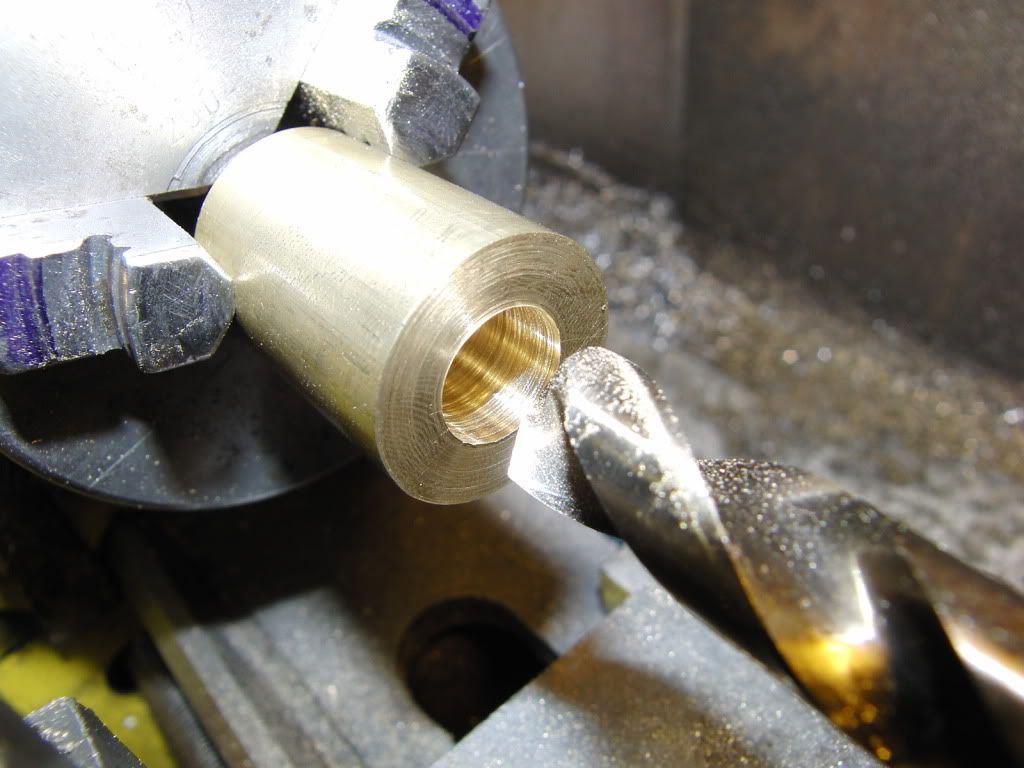
Boring the hole, (This is all standard stuff here, nothing exciting)
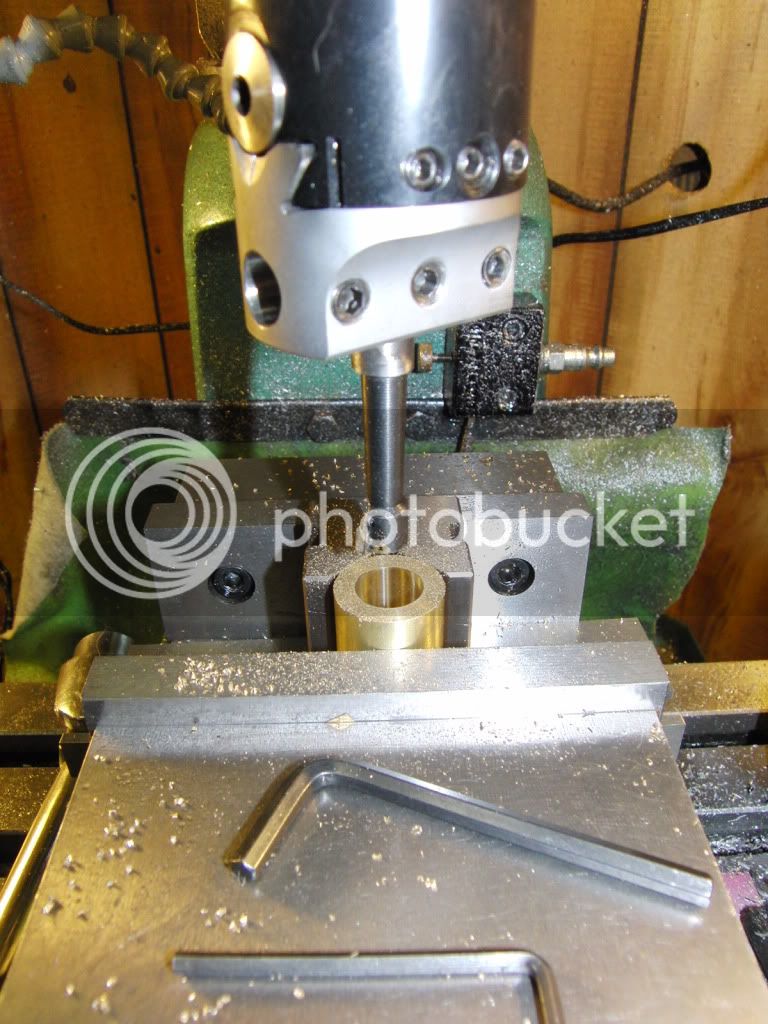
Marking out the fins with my height guage.
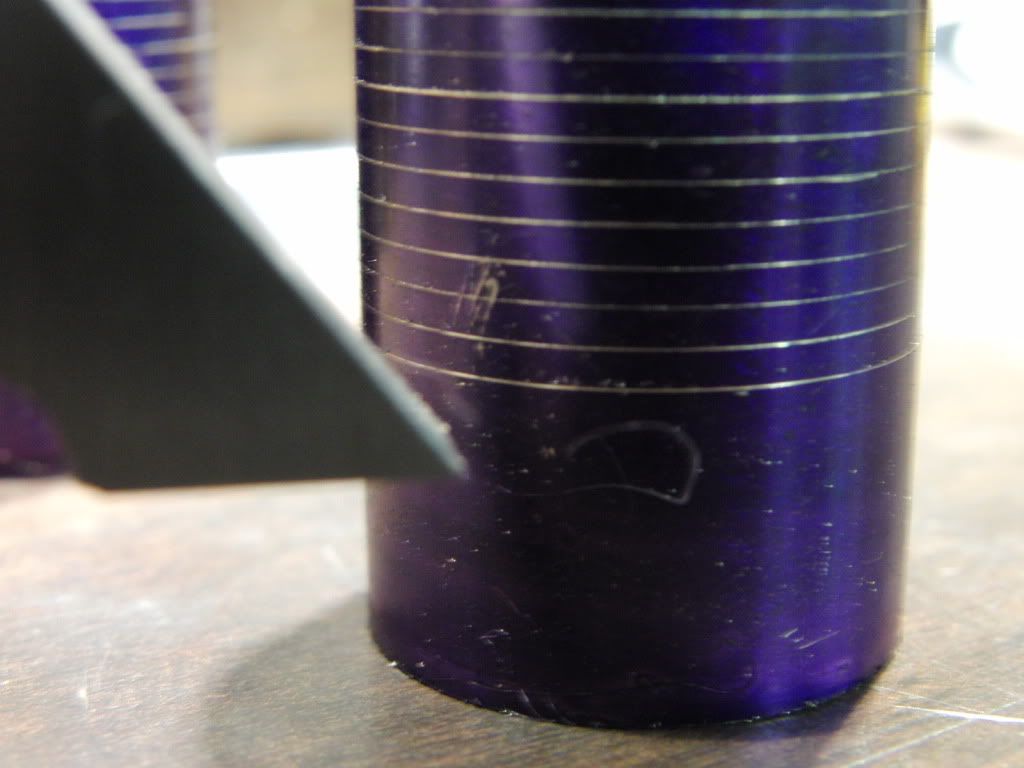
Now, cutting the fins, Brass cuts like a champ, I am always nervous when I use a parting blade, but It seems like with brass you can ram the tool in and all is well.
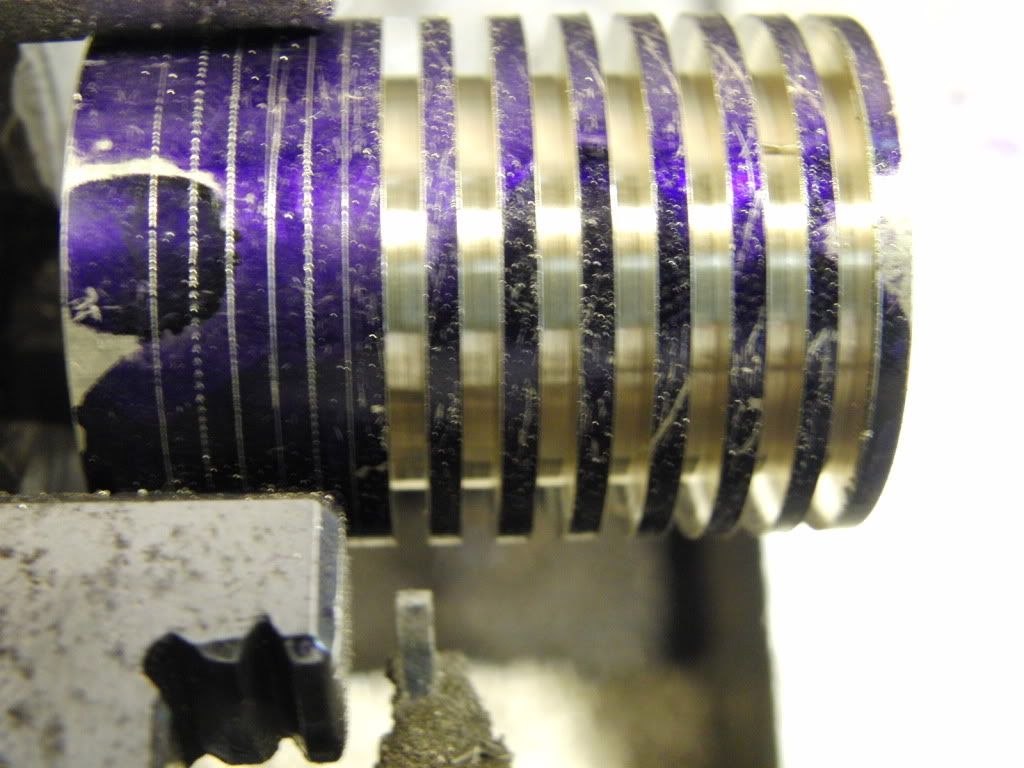
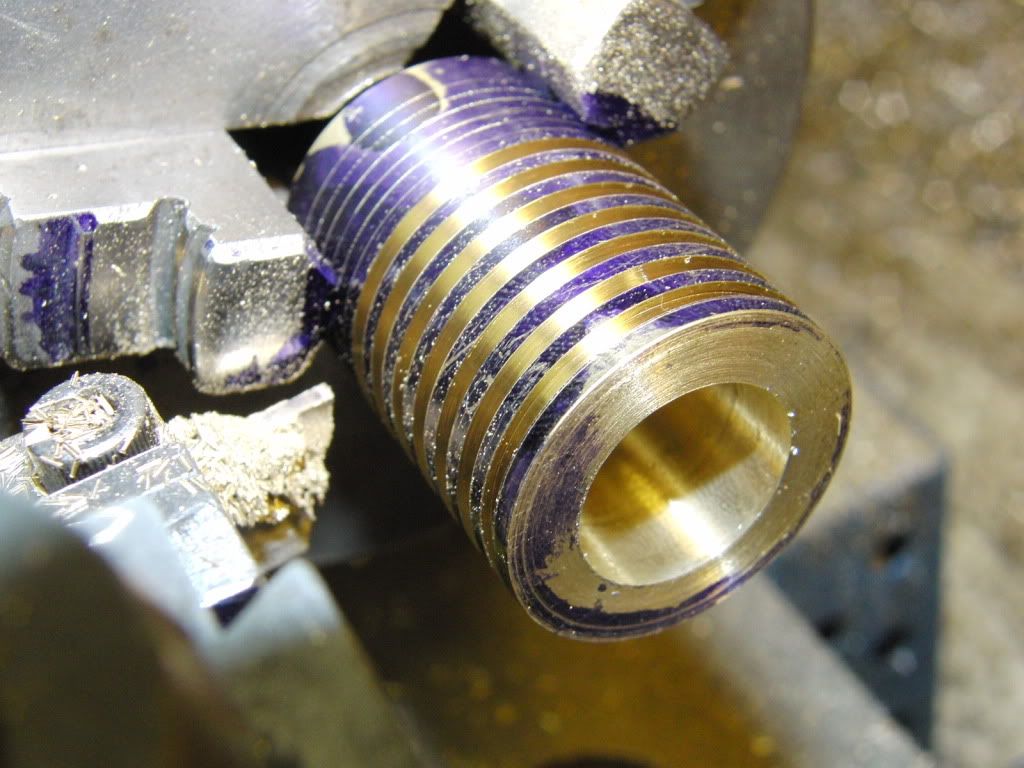
Here they are.
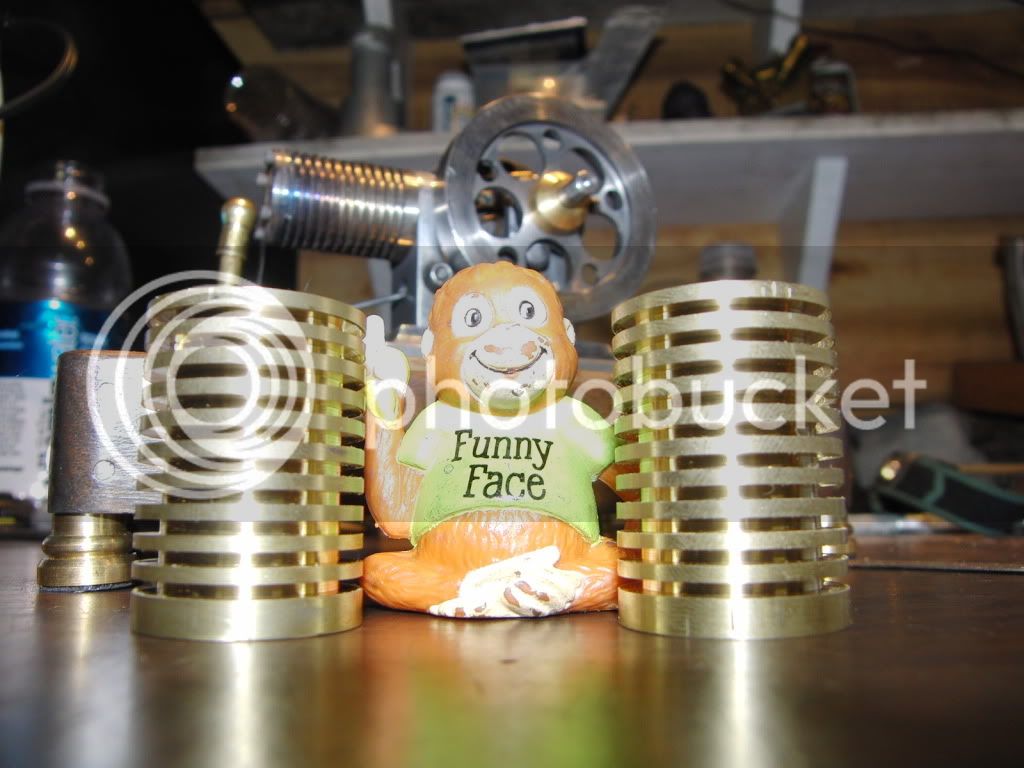
Kel