Milling the top side.
It's been flipped.
Here I'm milling the bottom side. I don't know where the remaining two screws are. I'll surly get them in by the time I get that far. It takes about an hour to mill a side. This is the third try for this cam. I was having trouble getting the sides to register. The trouble turned out to be my cheap 3/16 collet had the hole off center such that the cutter was running out by .007. I bought a new American made collet and my troubles cleared up.
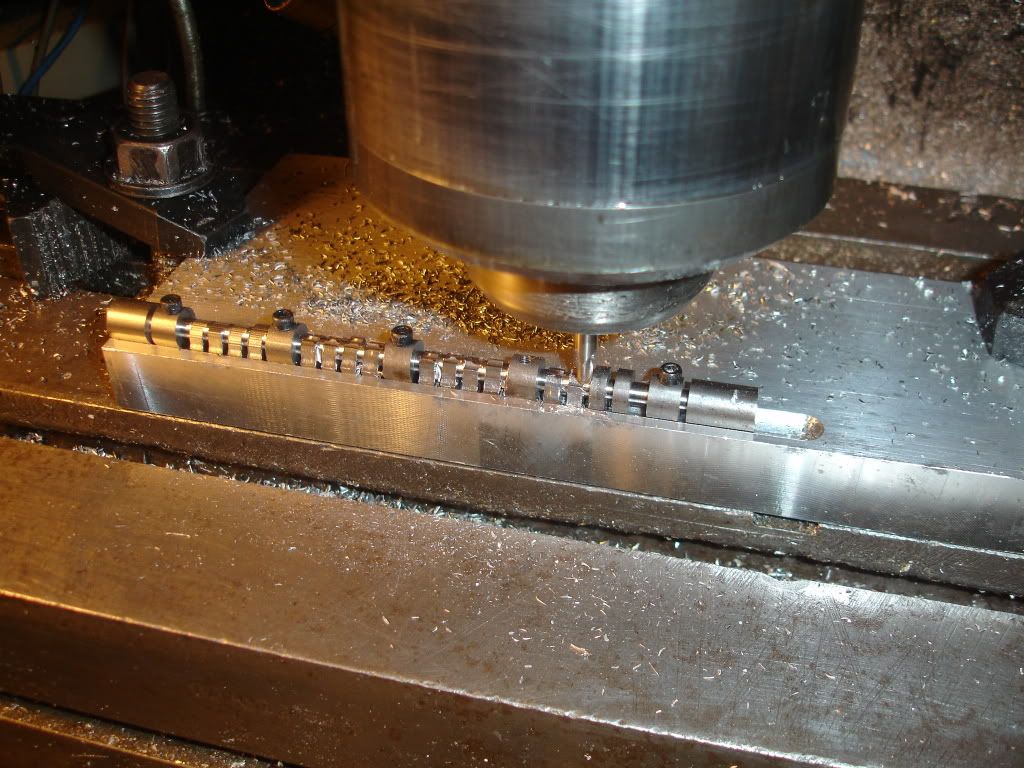
It's been flipped.
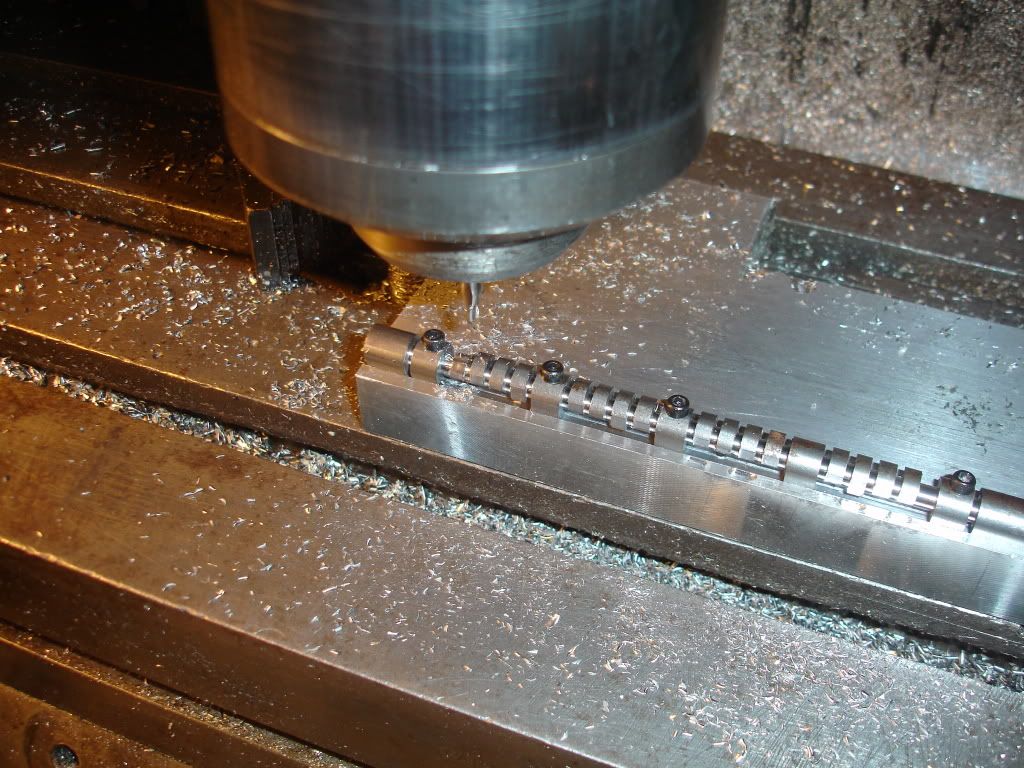
Here I'm milling the bottom side. I don't know where the remaining two screws are. I'll surly get them in by the time I get that far. It takes about an hour to mill a side. This is the third try for this cam. I was having trouble getting the sides to register. The trouble turned out to be my cheap 3/16 collet had the hole off center such that the cutter was running out by .007. I bought a new American made collet and my troubles cleared up.
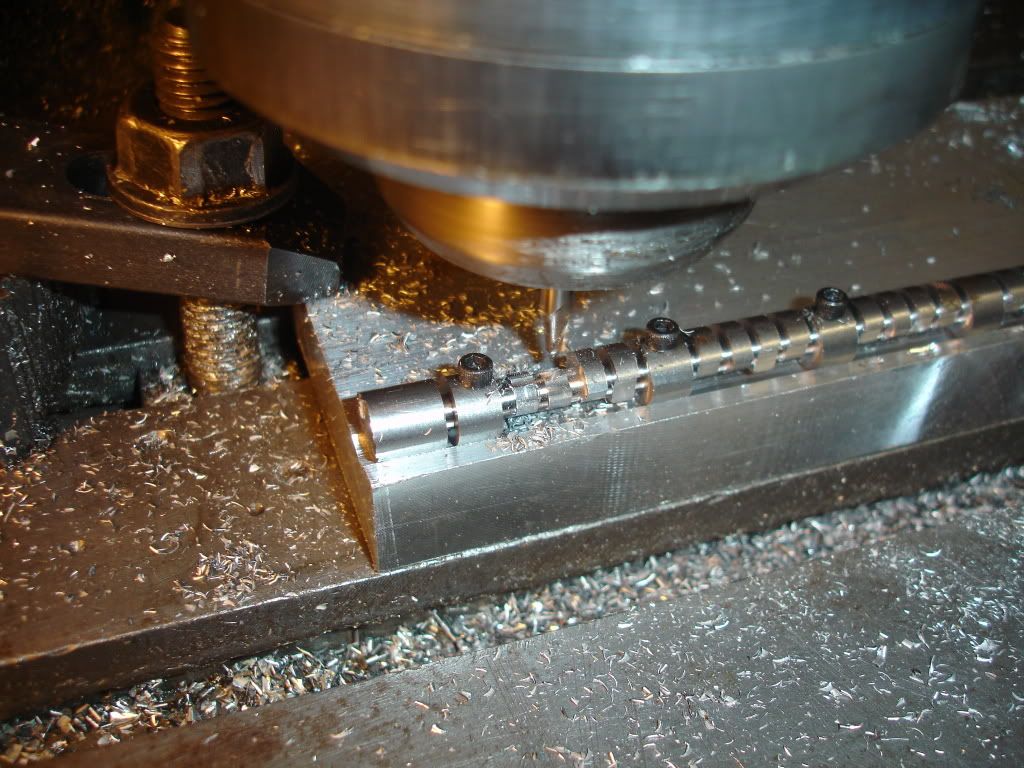