- Joined
- Aug 25, 2007
- Messages
- 3,890
- Reaction score
- 715
About time to get started on another engine. This will the smallest IC engine I've attempted with a 5/8" bore and 1.25" stroke. I want this to be another slow running engine and I think this is about as small as I can go without it sounding like a weed whacker.
Didn't have a beer can for scale, so I had to fabricate one, 12oz by the way. The cylinder will be made from cast iron. I decided to go with air cooling because it's so much simpler than water cooling. The flywheel is 5.5", which is quite large for this size engine, more like some of the really early Crosley and Daimler engines. Hopefully this will let me attain the slower idle speeds I'm looking for. The engine will be throttled using the simple carburetor I designed. I'm going to try really hard to provide the drawings for parts as I go along.
I'm toying with the idea of trying this CAM setup instead of the traditional geared cam...
Chuck
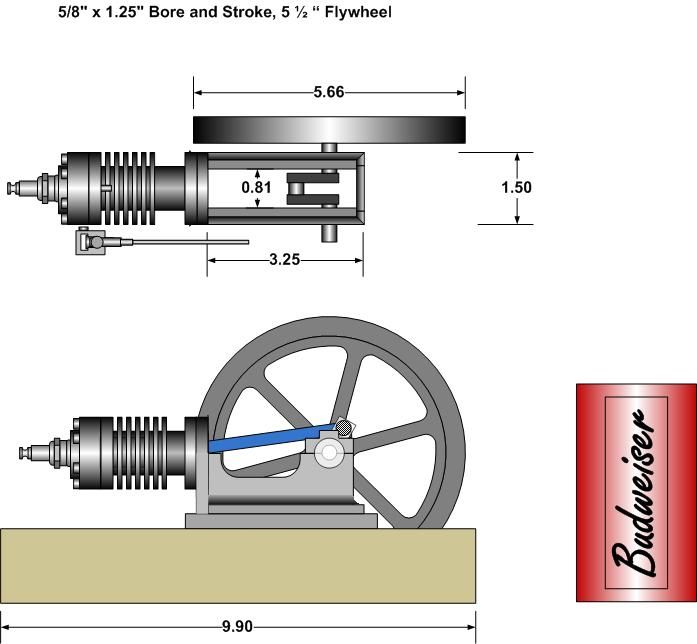
Didn't have a beer can for scale, so I had to fabricate one, 12oz by the way. The cylinder will be made from cast iron. I decided to go with air cooling because it's so much simpler than water cooling. The flywheel is 5.5", which is quite large for this size engine, more like some of the really early Crosley and Daimler engines. Hopefully this will let me attain the slower idle speeds I'm looking for. The engine will be throttled using the simple carburetor I designed. I'm going to try really hard to provide the drawings for parts as I go along.
I'm toying with the idea of trying this CAM setup instead of the traditional geared cam...
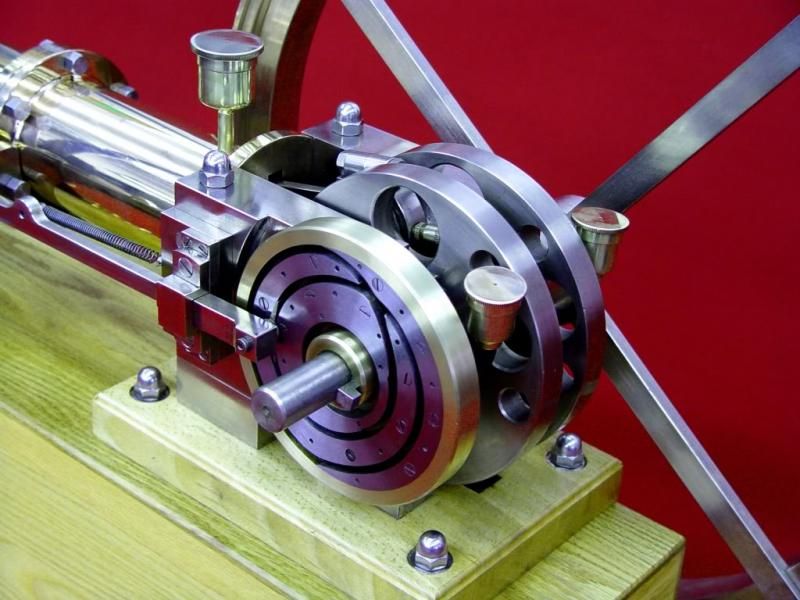
Chuck