Time to start on the Jan Ridder's Flame Eater. This will be a slow build for me as I only get a few hours to work now and then. 2nd engine, first time working with cast iron and doing any deep boring, etc... Should be a fun learning experience. My machines are in "inches" so I'm converting from metric and fudging the numbers when I can.
The "shop". Has to be cleaned up and rolled away every nite so the cars can go back inside (major PITA):
I turned the cylinder OD yesterday. Sorry--no pics. Got to use my 1-2" mic for the 1st time.
The fins setup. Got to use my home-made carriage-stop/DI-holder and 2" DI:
Just finished up the cylinder fins.
Turned out OK I think. I don't have a 2mm tool and didn't want to grind one--so 1/16" is close enough and I recalculated the dimensions ending up with a few more "thinner" fins than on the plans. I don't think it will matter but if it does I've shot myself in the foot from the very beginning:
More as it happens.
The "shop". Has to be cleaned up and rolled away every nite so the cars can go back inside (major PITA):
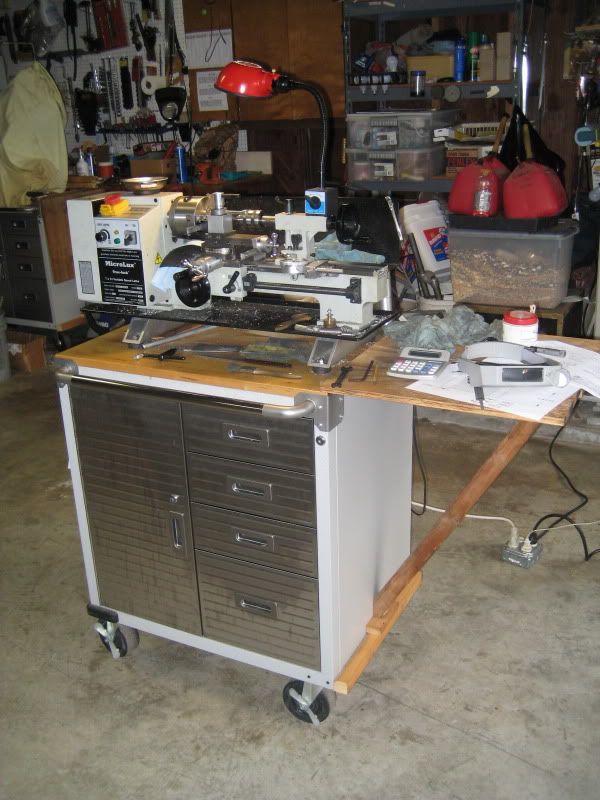
I turned the cylinder OD yesterday. Sorry--no pics. Got to use my 1-2" mic for the 1st time.
The fins setup. Got to use my home-made carriage-stop/DI-holder and 2" DI:
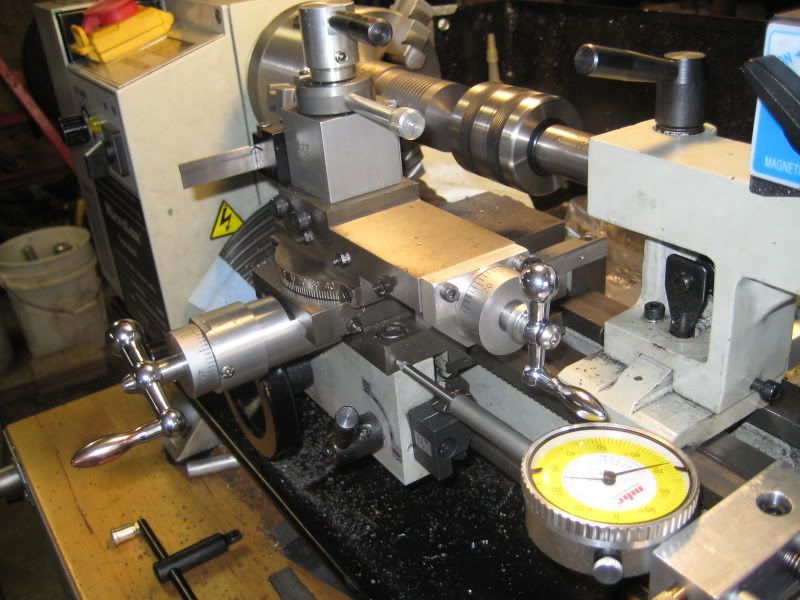
Just finished up the cylinder fins.
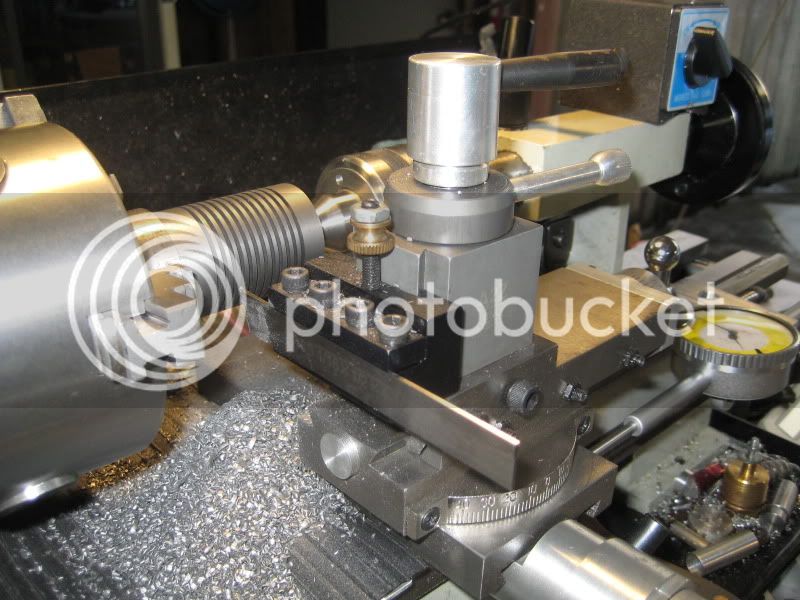
Turned out OK I think. I don't have a 2mm tool and didn't want to grind one--so 1/16" is close enough and I recalculated the dimensions ending up with a few more "thinner" fins than on the plans. I don't think it will matter but if it does I've shot myself in the foot from the very beginning:
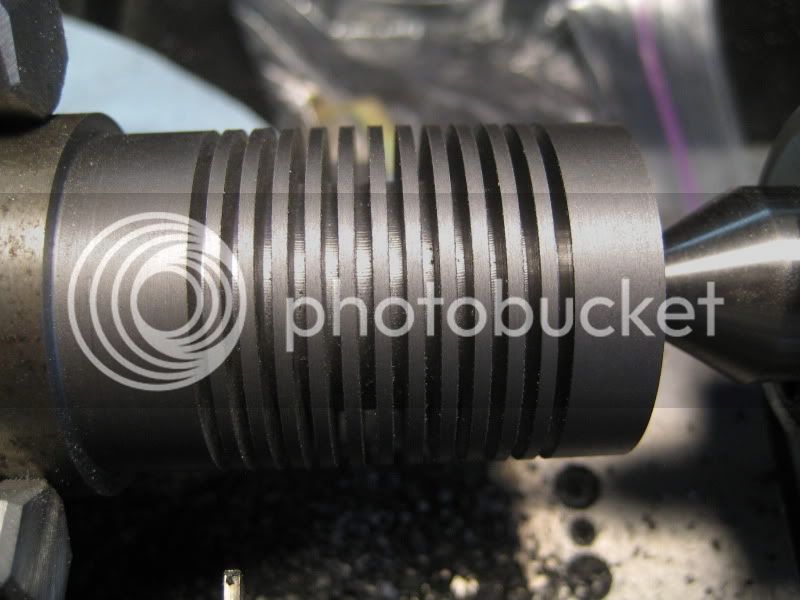
More as it happens.