Enough time has gone by now, that I can start thinking about the wonky crankshaft on my opposed piston engine. Through trial and error I have weeded out the carburation issues, the flywheel issues, and now the only real issue remaining is the crankshaft. The engine runs great. The crankshaft seems to be good everywhere except for the portion that extends out past the front bearing. I built the crankshaft in pieces, and held the two ends in a jig for my final assembly, hoping that would yield a nice straight crank, but sadly that was not to be. There is considerable run-out as can be easily seen by looking at all the bobbing and weaving that aluminum hand-wheel on the front of the crankshaft is doing while the engine runs. It doesn't do that on the flywheel end---seems to run "true as a die" back there. I really don't want to build a new crankshaft. My plan is to remove the crankshaft from the engine, cut the front off the crankshaft right beside the "throw" nearest to the front bearing, hold the flywheel end in my 3 jaw chuck, and bore the "throw" 13/32", then make up a new end which is .375" diameter over its full length except for the bit that extends through the 1/4" crank throw, which will be 13/32" diameter. I now have a tailstock chuck for my lathe with a bearing on it so that it can rotate freely. I am considering holding the flywheel end in the main chuck, holding the new end in the tailstock chuck, and silver soldering the final joint while the part is held perfectly aligned in the two chucks. There won't be enough heat transfer to damage either chuck, and if it doesn't work, I can then build a whole new crankshaft.-Nothing ventured --Nothing gained!!! To see what I am describing as "Wonky" click on the video link and watch that front aluminum wheel.
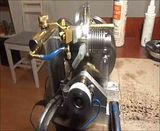