Sshire
Well-Known Member
- Joined
- Jun 29, 2011
- Messages
- 936
- Reaction score
- 259
Elmer's pumping engine
Since I've been home from Cabin Fever for a few days, it's time to begin making engines for next year.
The first will be Elmer's Pumping Engine. As usual for me, I'm working bottom up. I had a piece of 1/2" 12L14 that will be good for the base. After squaring it up and milling to size, I flattened it with the face mill.
Even though all holes will be positioned with the DRO, I marked out all of the spots for drilling. This is just to prevent brain drift or reading a number incorrectly.*
Not much interesting or revolutionary here, but part one is done.
Next will be the catwalk. This should be much more interesting once I decide how I'm going to do the center opening. (drill corners and saw to connect or center cutting end mill and just DRO around the perimeter until the middle piece of aluminum falls out.)
Since I've been home from Cabin Fever for a few days, it's time to begin making engines for next year.
The first will be Elmer's Pumping Engine. As usual for me, I'm working bottom up. I had a piece of 1/2" 12L14 that will be good for the base. After squaring it up and milling to size, I flattened it with the face mill.
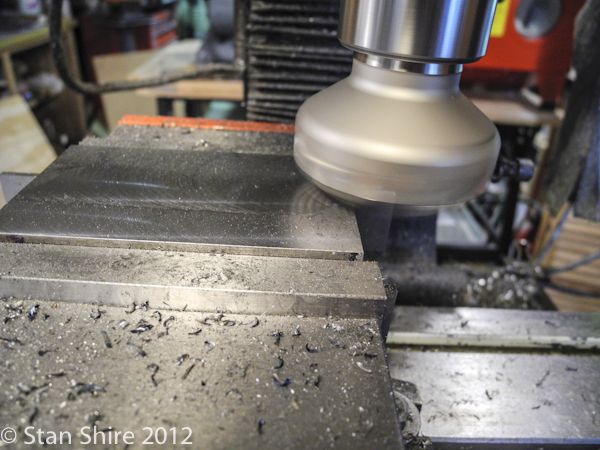
Even though all holes will be positioned with the DRO, I marked out all of the spots for drilling. This is just to prevent brain drift or reading a number incorrectly.*
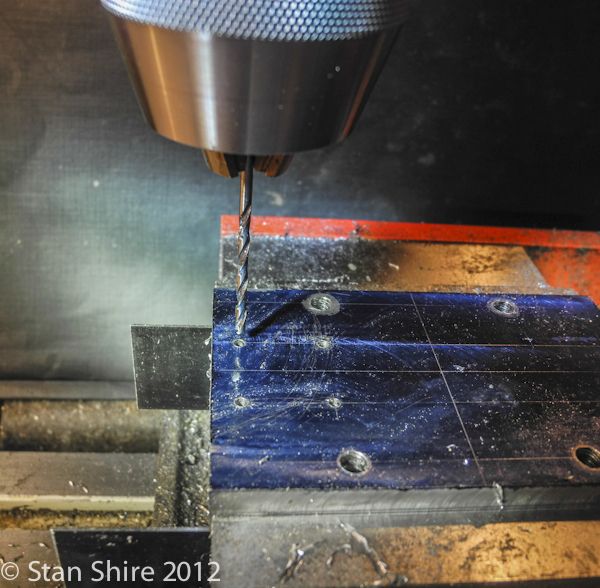
Not much interesting or revolutionary here, but part one is done.
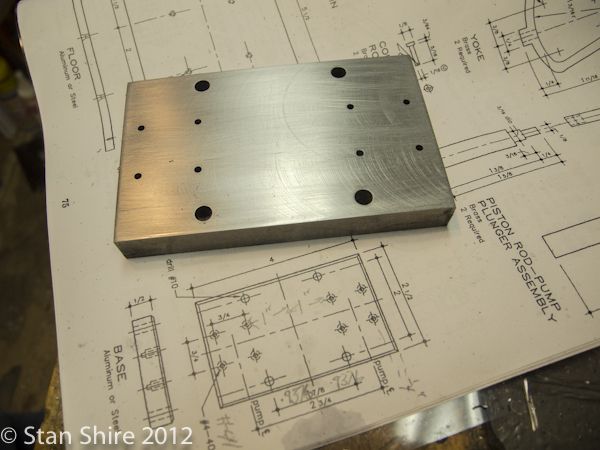
Next will be the catwalk. This should be much more interesting once I decide how I'm going to do the center opening. (drill corners and saw to connect or center cutting end mill and just DRO around the perimeter until the middle piece of aluminum falls out.)
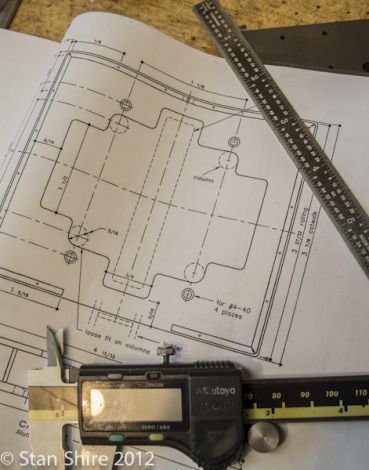