- Joined
- Feb 17, 2008
- Messages
- 2,326
- Reaction score
- 440
With all the cast iron machining done the first order of business was to clean up the lathe and mill. I had kept them reasonably clean as I went along but it still took a hour or so the do the job right. Cast Iron is nice to machine but a pain to clean up.
Then it was over to the mill to center drill, drill and tap the oil cup holes 3-56. I know it's not a common thread, but I like it. Not too much to be said about that and really not worthy of a photo, but I did one anyway. Next up the oil cups.
Gail in NM
Then it was over to the mill to center drill, drill and tap the oil cup holes 3-56. I know it's not a common thread, but I like it. Not too much to be said about that and really not worthy of a photo, but I did one anyway. Next up the oil cups.
Gail in NM
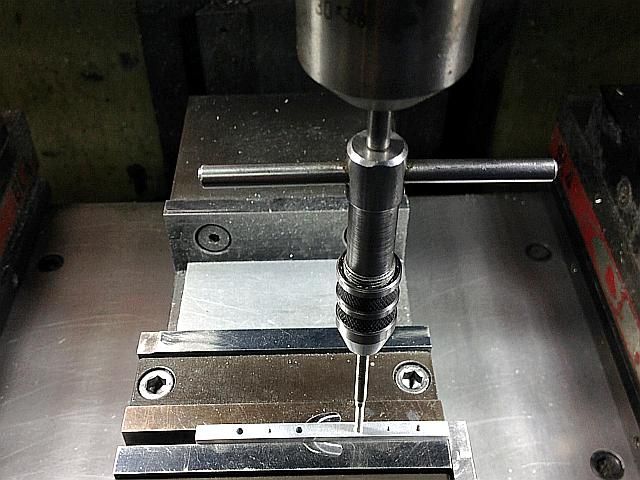