The gearcase needs 8 8-32 tapped holes put in the top surface for the top cover. This pic is of the gearcase set in the mill vise and using an edgefinder to find the left edge of the part.
Spotting the holes with a spotting drill first.
Then drilling with a tap drill.
Then tapping.
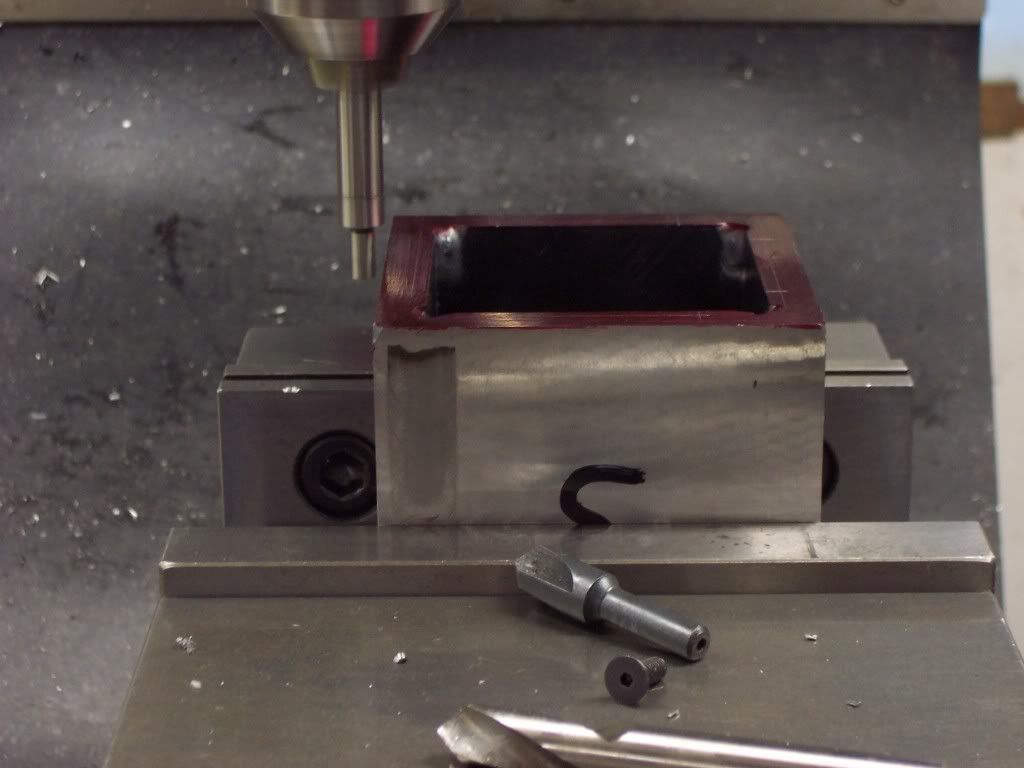
Spotting the holes with a spotting drill first.
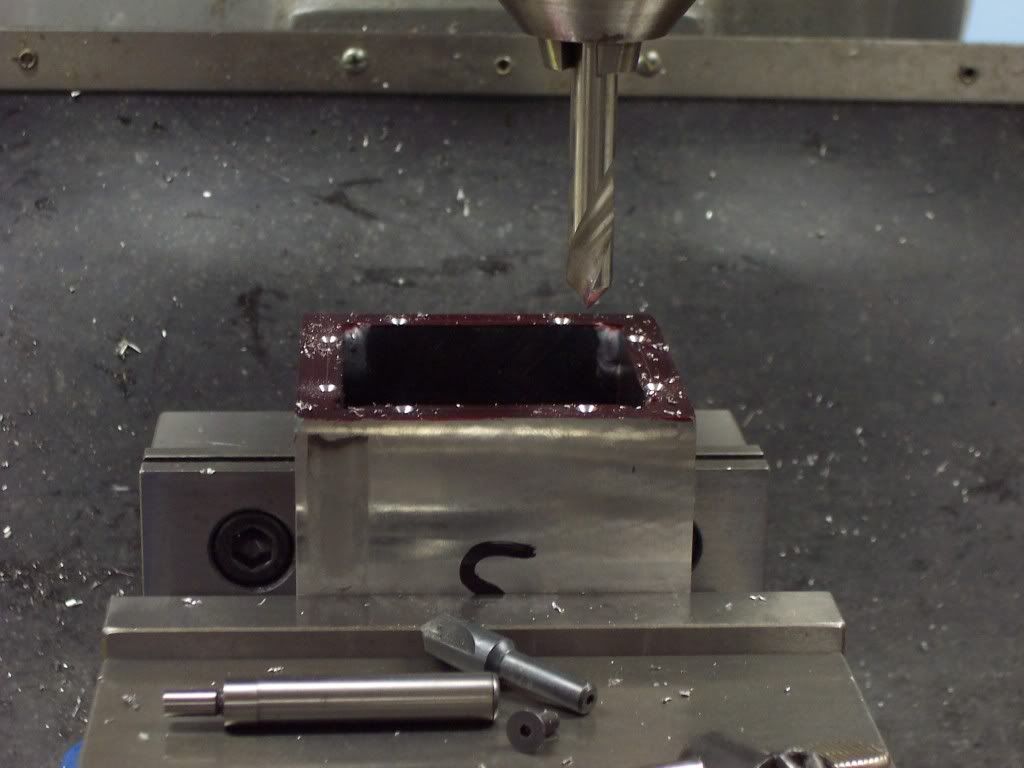
Then drilling with a tap drill.
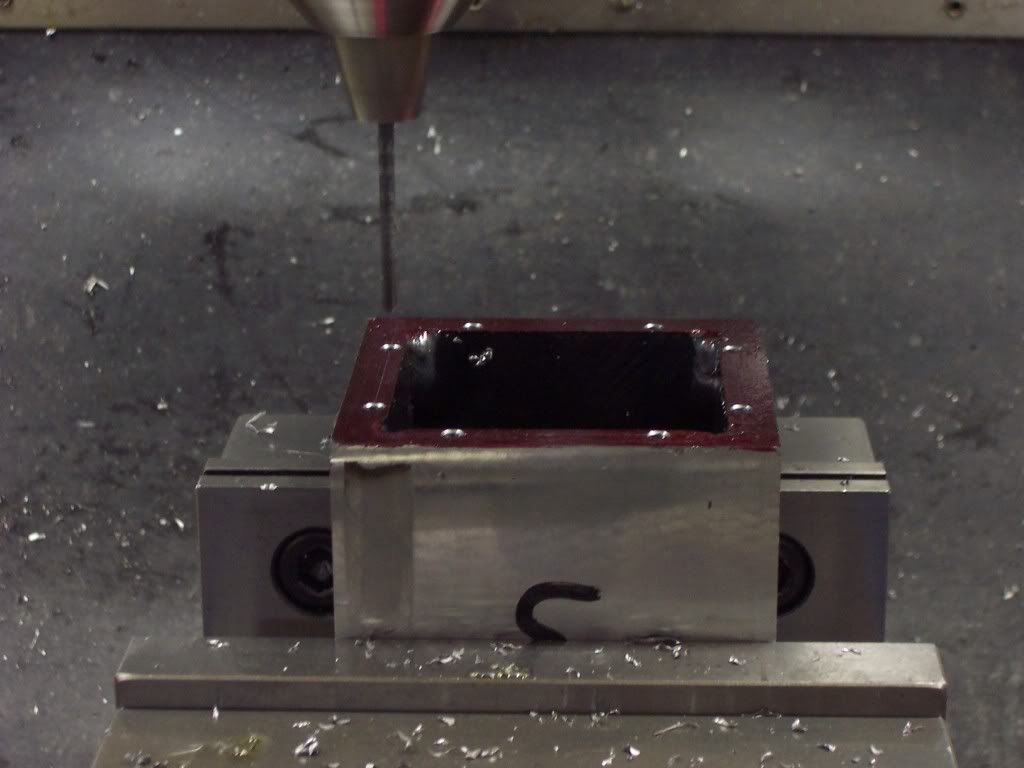
Then tapping.
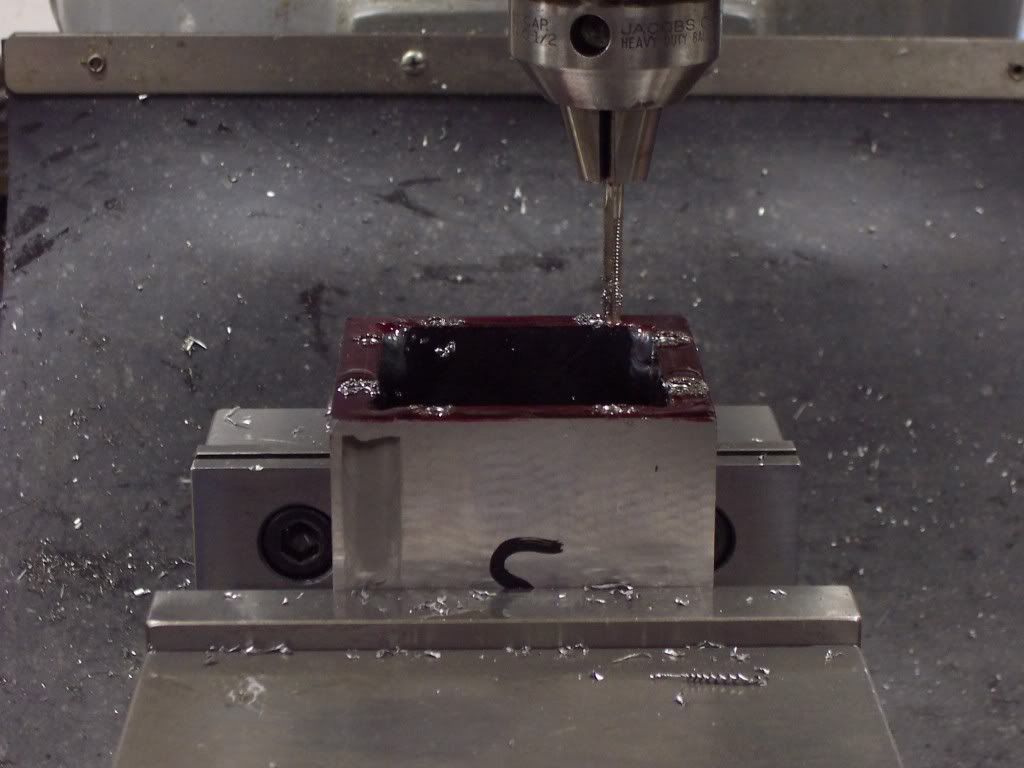