Heres a pic of cutting the Woodruff keyway. The shaft is held in the vise jaws using V-blocks. I used my angle plate on the outboard end for support. The center in "Z" was found by using a piece of .004" thick paper between the cutter and the major dia of the part. The knee was raised until the paper walks out from between cutter and the part and then Zero was set. I next moved the knee up in .001" increments until it lightly touched the part. This was done with the cutter rotating and I reset my Zero. Now I moved the knee up half the dia of my shaft and half the thickness of the cutter to put me on center.
The info for the depth of cut was taken from my Machinery Handbook.
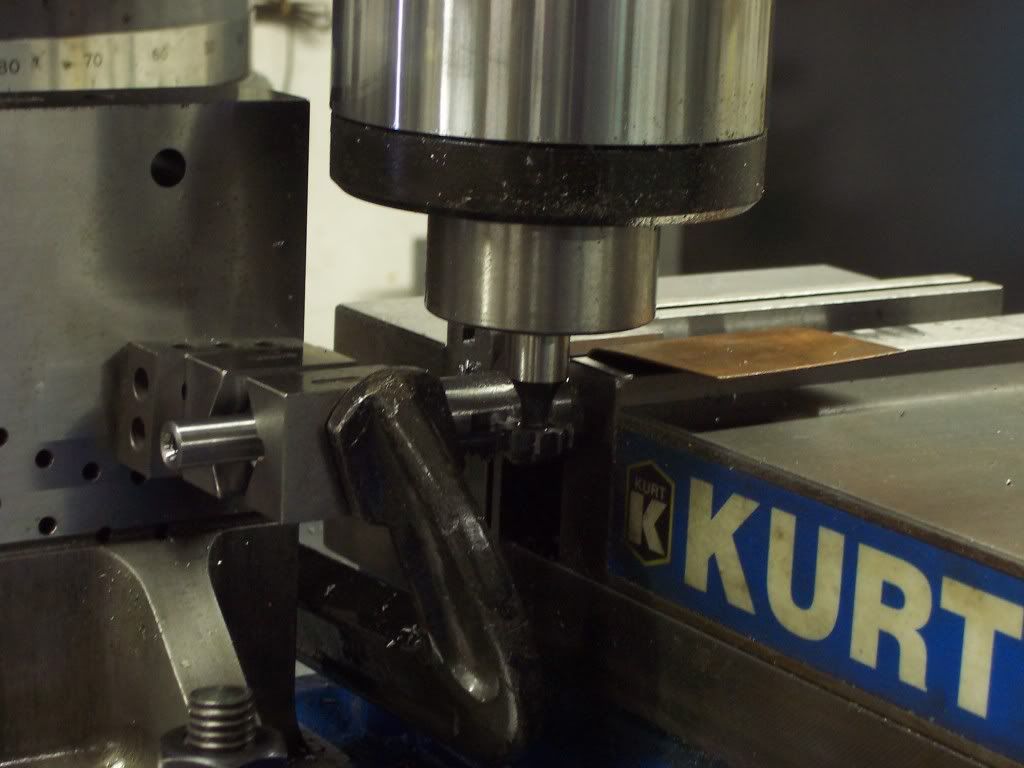
The info for the depth of cut was taken from my Machinery Handbook.