I have decided to go ahead and build the pump, http://www.homemodelenginemachinist.com/index.php?topic=6056.0 as its a slow Sunday and all of the major hot-rod (my OTHER hobby) events are over for this summer. As I started hunting through my "stash" of aluminum, the first thing to become apparent was that I don't have any 3" x 1" aluminum flat bar.---Thats okay--we're resourcefull---Make it out of two peices bolted together!! I have dismantled the "Varying load machine" and scavenged a peice of 1" square aluminum bar from it. The next thing to show up is that the maximum diameter of stock that will fit though the hole in my 4 jaw chuck is only 1 1/8", and a 1" square bar is 1.41" across the corners!! How the heck can I drill a 1/2" hole full length of a 10 5/8" long part. (Its too tall to fit in the milling machine, along with a chuck and 1/2" drill).---Like I said, "resourcefull is my middle name"---I'll turn the bottom half to 1" diameter between centers so I can grip it in my 3 jaw chuck to drill it. Are you with me so far???---I put a dead center in the 3 jaw, put a live center in the tailstock, then realize that I have no lathe dog big enough to fit over a 1" square bar.---Out to my scrap steel pile, find a peice of 1 1/2" square tubing with a 1/8" wall, weld a 1/2" peice of threaded rod to it for a "tail" that fits between the chuck jaws, drill and tap two 1/4"-20 holes on two adjacent sides of it to locate it on the square bar, and I'm off to the races!!!
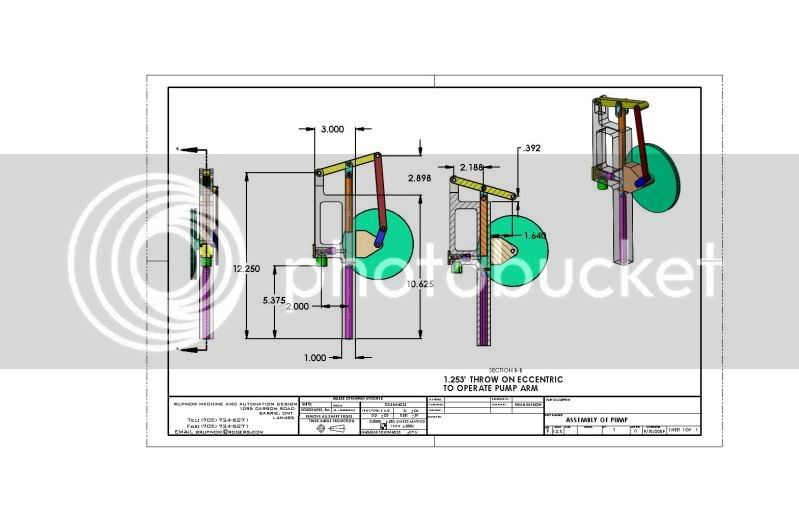
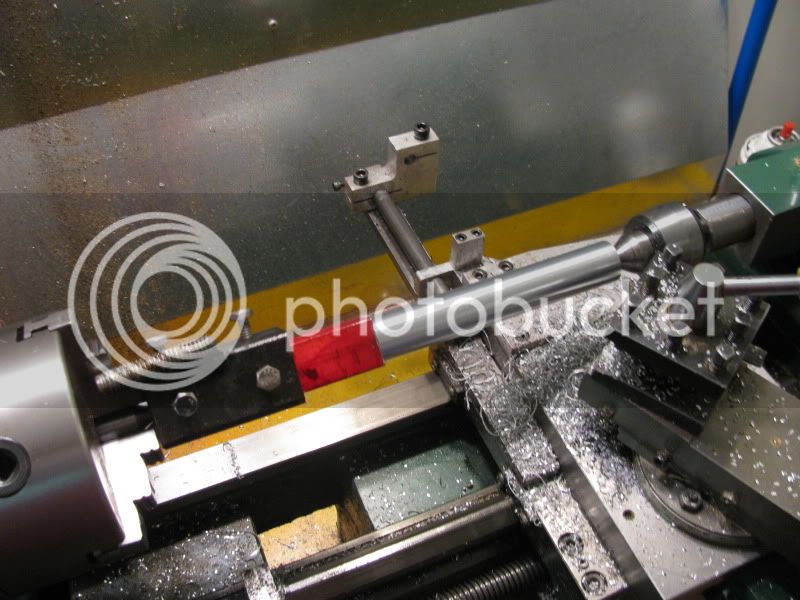