kutzdibutz
Well-Known Member
- Joined
- Feb 16, 2012
- Messages
- 74
- Reaction score
- 28
Hi there,
hmm- is there something wrong with the posts? Too many pictures? Too much bullsh*tting?, Too boring? Looks a bit like monologise around here...
Anyways- I made it to the shop again and started the next part. This one will connect the power piston with the crankshaft. (eventually) Sketching it in CAD was sooo easy and quickly done- but making it for real took me some headscratching. First I cleared a piece of aluminum (of the same mavellous smearing sh*t) and placed in the 4-jaw. Center drill and turned the front bit round.
For the ange of the cone I 'adjusted' the cutter- and of course it did chatter like hell when it was cutting on the long edge of the tool. I also know I should have used the cross slide adjusted to the cone angle- but I was too lazy to take the support apart for back and forth adjustment and dismount all the chip protection I installed for my DRO only to do a proper setup for making the cone... At the end I removed the chatter-marks with a file. Not very elegant- but it worked... :hDe:
Then drilling the hole and the lathe job for this part is done...
So thats as far as I made it tonight- next fun will be on the mill again...
Cheers, Karsten
hmm- is there something wrong with the posts? Too many pictures? Too much bullsh*tting?, Too boring? Looks a bit like monologise around here...
Anyways- I made it to the shop again and started the next part. This one will connect the power piston with the crankshaft. (eventually) Sketching it in CAD was sooo easy and quickly done- but making it for real took me some headscratching. First I cleared a piece of aluminum (of the same mavellous smearing sh*t) and placed in the 4-jaw. Center drill and turned the front bit round.
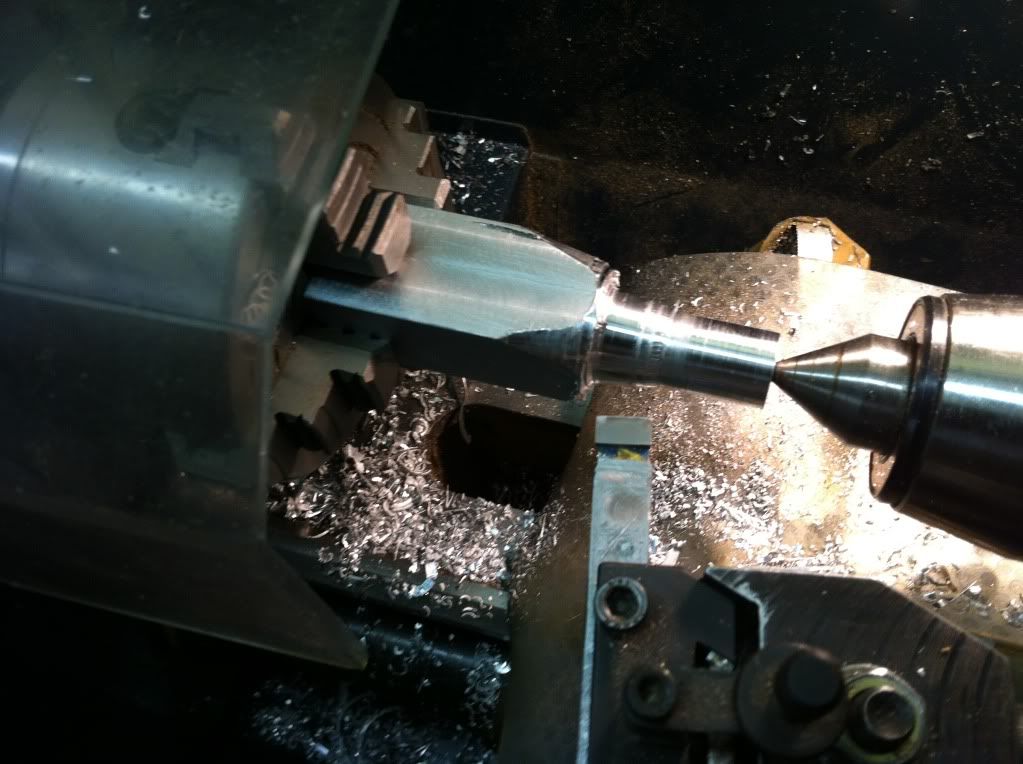
For the ange of the cone I 'adjusted' the cutter- and of course it did chatter like hell when it was cutting on the long edge of the tool. I also know I should have used the cross slide adjusted to the cone angle- but I was too lazy to take the support apart for back and forth adjustment and dismount all the chip protection I installed for my DRO only to do a proper setup for making the cone... At the end I removed the chatter-marks with a file. Not very elegant- but it worked... :hDe:
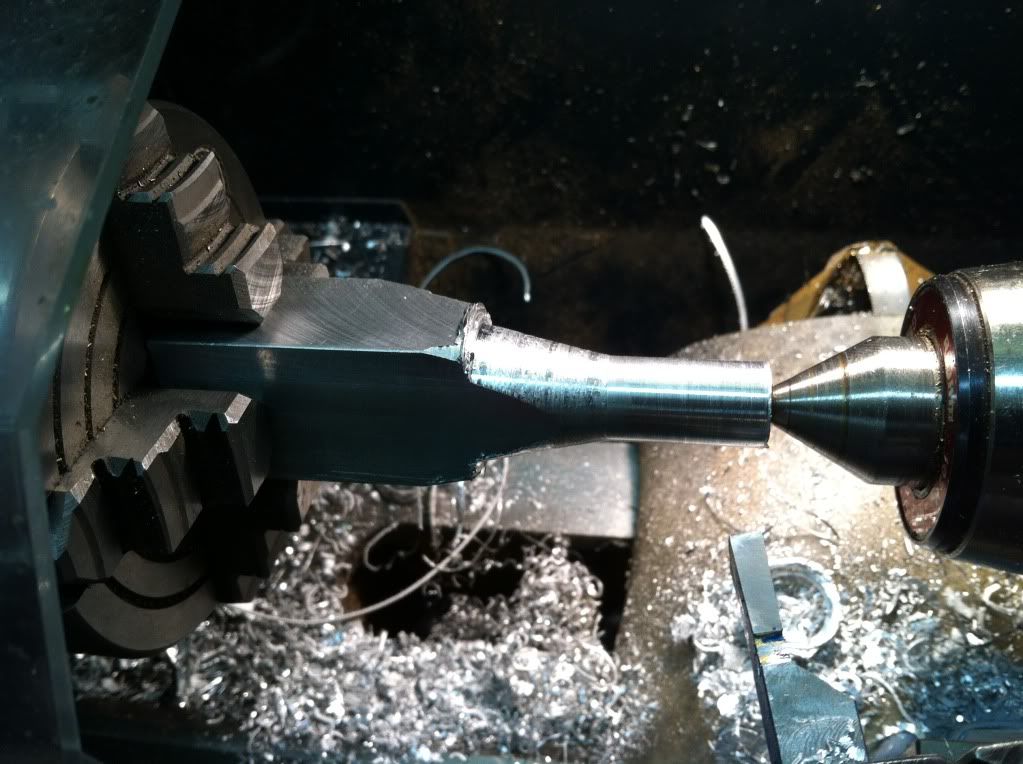
Then drilling the hole and the lathe job for this part is done...
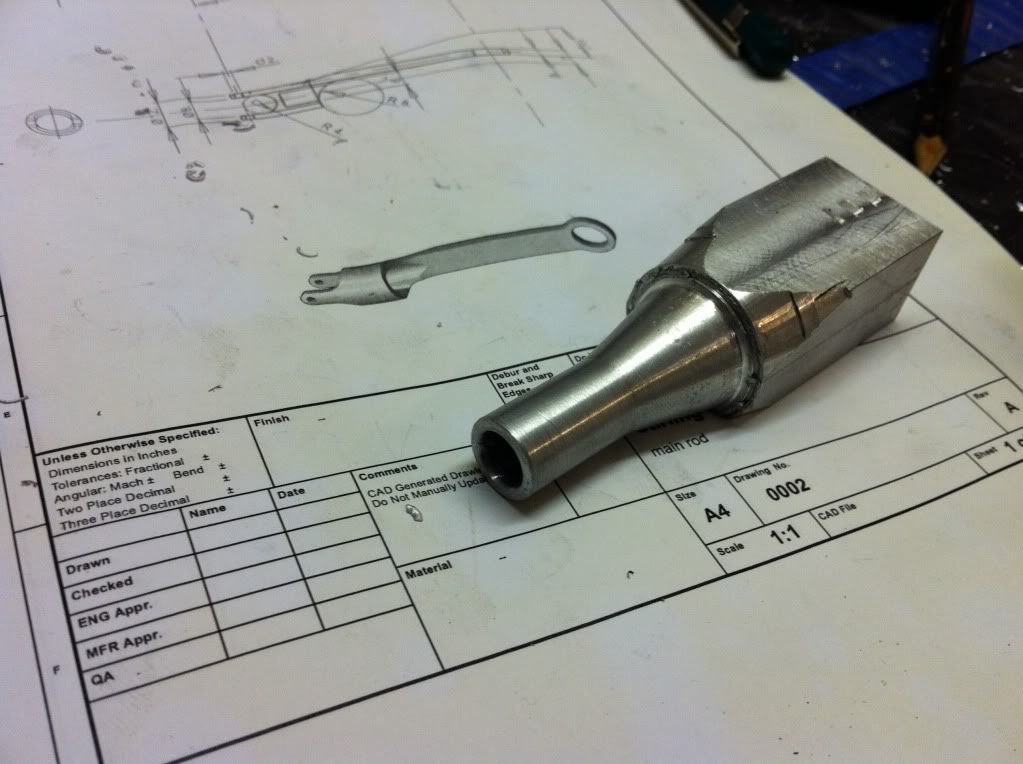
So thats as far as I made it tonight- next fun will be on the mill again...
Cheers, Karsten