Hmmm--Not a particularly good start to the morning!! My new Powerfist brake cylinder hone which is supposed capable of fitting 3/4" to 1 1/8" brake cylinder bores---There is no way in Hell that it is going to fit into a 3/4" bore. RATS!!! I guess these cylinders will move directly from "reamed" to "lapped"
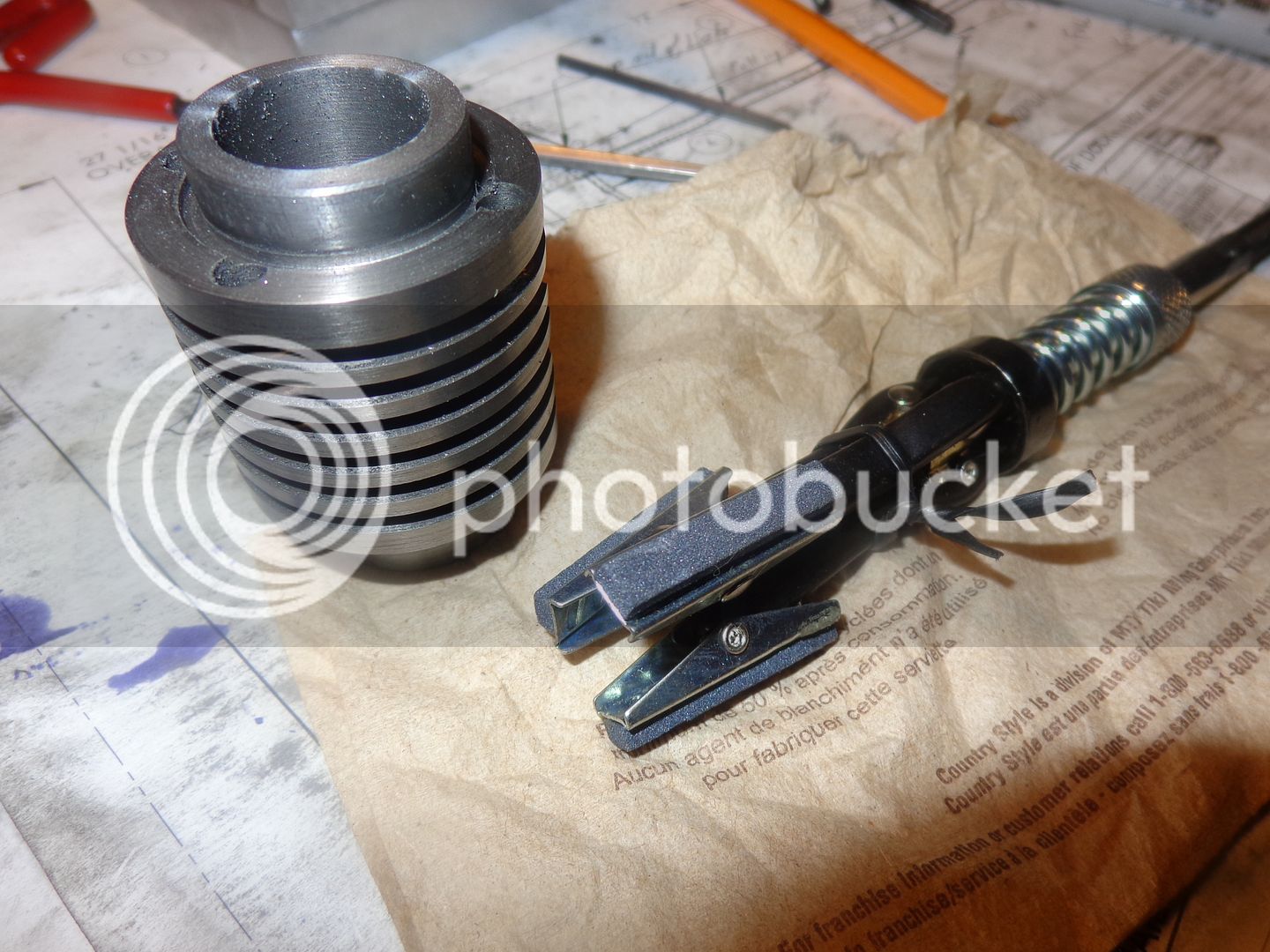