Generatorgus
Senior Member
- Joined
- Feb 25, 2010
- Messages
- 362
- Reaction score
- 166
Since I already have the exhaust and water outlets made with a rounded rim on the tube part, I wanted to keep with that theme, so the elbow I dug out of the fitting bins would be the model.
First thing was to make a small rounding tool out of a water hardening drill rod.
Simple enough.
I was only cutting brass but I figured I might as well harden it.
Quote: "I new better but did it anyway."
First lesson learned that day was not to use the dogs Styrofoam water dish for cooling a red hot piece of steel.
The rim was burned with the torch when I pulled it off of the workbench because the water was running all over my welder.
That lesson duly noted I got busy making the half elbow pieces.
I first tried making the rim then turning the minor diameter and drilling a pilot hole.
Poor plan, it would be difficult be difficult to hold while cutting the miter, which I intended to do with an end mill.
After figuring that out I decided to make another rim farther down the same piece which was a piece of brass bolt. That ended unhappily. Holding a work piece by the threads is something I should do less often or not at all.
New plan. Drill the pilot hole, turn the small end , cut the miter with the slitting saw. (Note: In an earlier post I was complaining about the screw on thearbor being siezed. While doing this cutoff, a bit of chatter loosened it up, maybe I won't can it after all.)
Then back in the lathe to make the rim and part it off.
For this and being the frugal person I am and not having a piece of 3/8 brass rod on hand, I sacrificed a couple of ½ brass screws that I have a few dozen of for quite a while and havent ever used one.
For times later I had this, ready for the torch.
First thing was to make a small rounding tool out of a water hardening drill rod.
Simple enough.
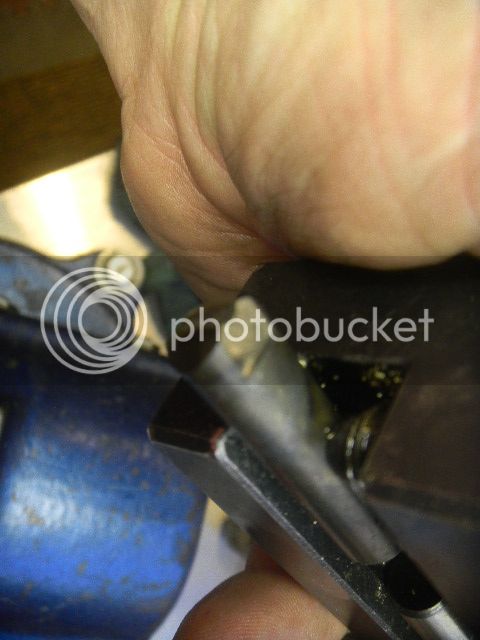
I was only cutting brass but I figured I might as well harden it.
Quote: "I new better but did it anyway."
First lesson learned that day was not to use the dogs Styrofoam water dish for cooling a red hot piece of steel.
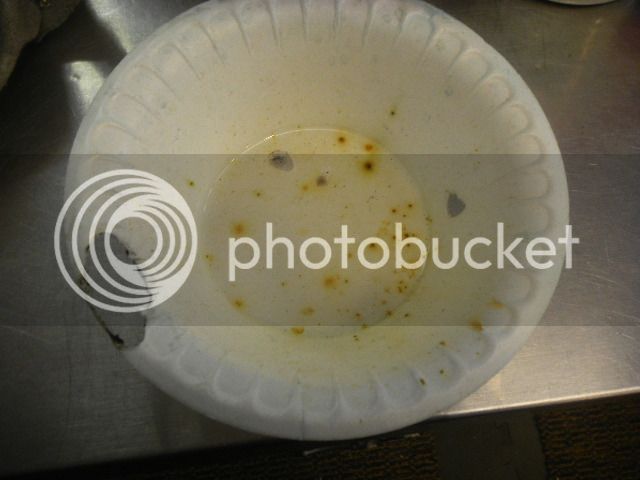
The rim was burned with the torch when I pulled it off of the workbench because the water was running all over my welder.
That lesson duly noted I got busy making the half elbow pieces.
I first tried making the rim then turning the minor diameter and drilling a pilot hole.
Poor plan, it would be difficult be difficult to hold while cutting the miter, which I intended to do with an end mill.
After figuring that out I decided to make another rim farther down the same piece which was a piece of brass bolt. That ended unhappily. Holding a work piece by the threads is something I should do less often or not at all.
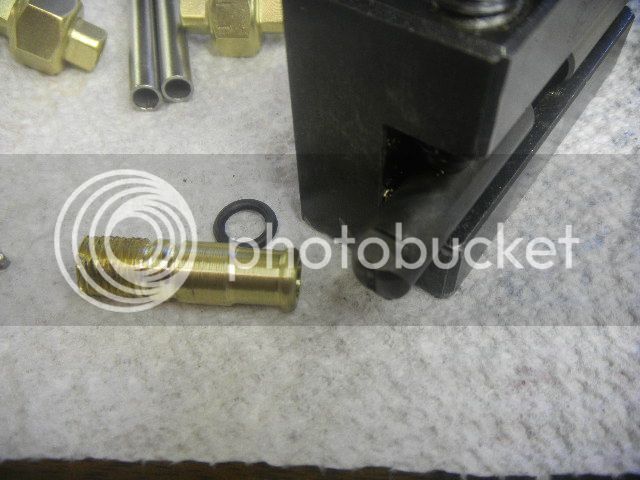
New plan. Drill the pilot hole, turn the small end , cut the miter with the slitting saw. (Note: In an earlier post I was complaining about the screw on thearbor being siezed. While doing this cutoff, a bit of chatter loosened it up, maybe I won't can it after all.)
Then back in the lathe to make the rim and part it off.
For this and being the frugal person I am and not having a piece of 3/8 brass rod on hand, I sacrificed a couple of ½ brass screws that I have a few dozen of for quite a while and havent ever used one.
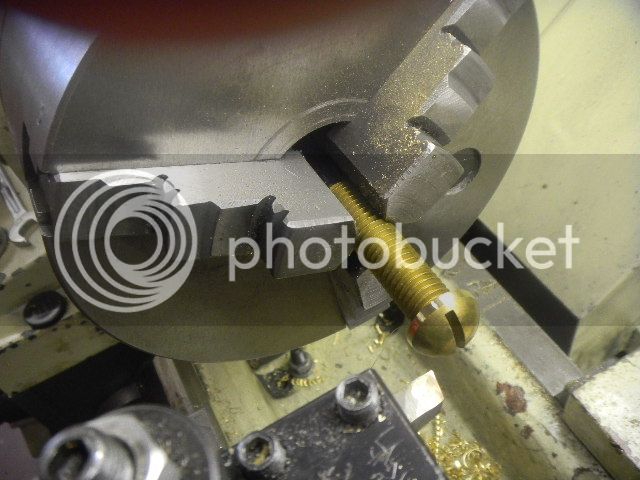
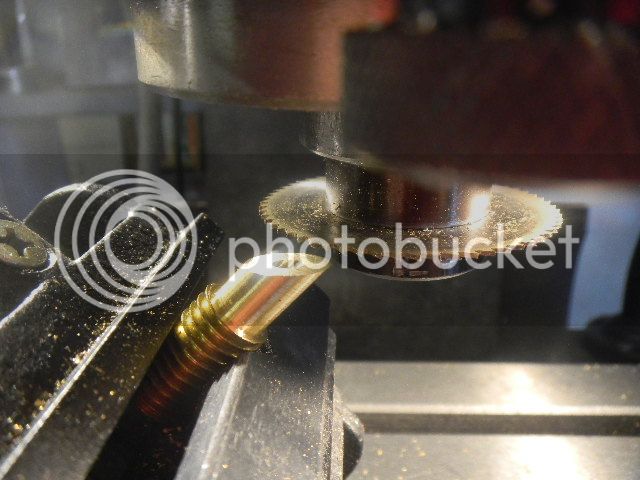
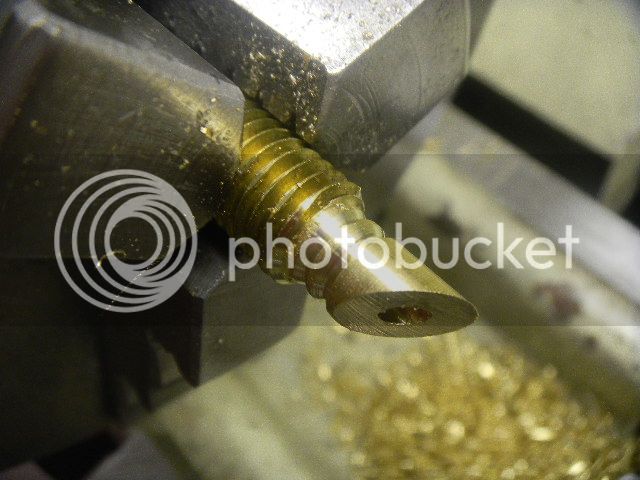
For times later I had this, ready for the torch.
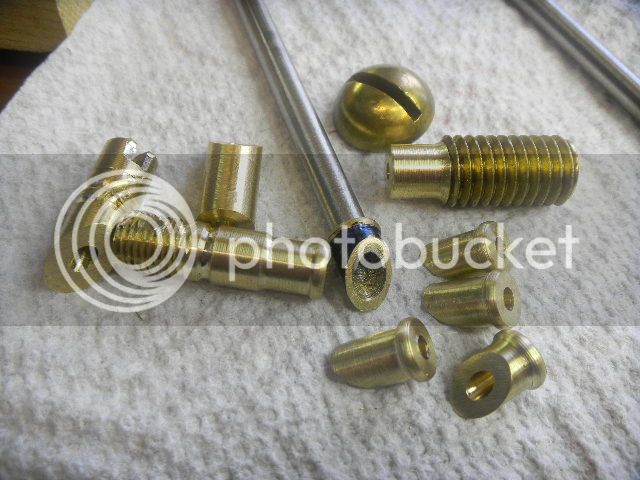