Tony Bird
Senior Member
Hi,
Last weekend while at a Model Engineering Exhibition I bought from Blackgate Engineering drawings and casting to make a Weir type pump. It is the first time in many years that I have used castings in a model, mostly I fabricate. What did I get for a little over £30? Well drawings along with six Gunmetal castings, some '0' rings and springs.
The drawings were copied cut down in size and laminated. The castings were measured to check that it was possible to machine them to size. All of the castings except for one were generous in size. The cylinder casting in its rogh state was a little under size in width. This wouldn't be a problem. So a start was made roughing out the castings before getting down to exact sizes.
Photographs of rough out the castings.
Wax chucks were used for the flat bits.
Some more photographs to follow.
Regards Tony.
Last weekend while at a Model Engineering Exhibition I bought from Blackgate Engineering drawings and casting to make a Weir type pump. It is the first time in many years that I have used castings in a model, mostly I fabricate. What did I get for a little over £30? Well drawings along with six Gunmetal castings, some '0' rings and springs.
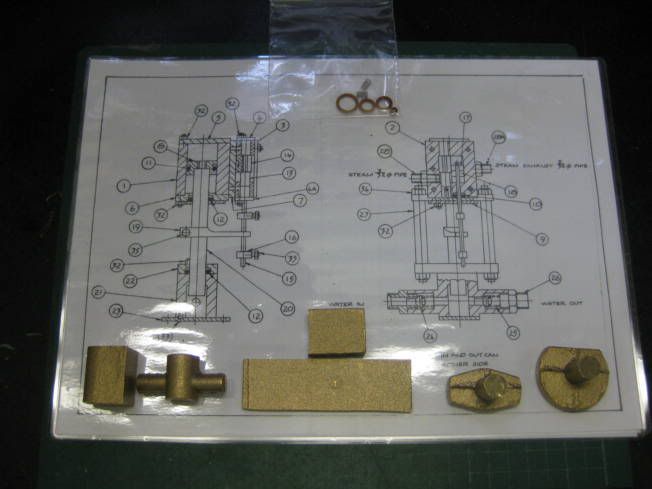
The drawings were copied cut down in size and laminated. The castings were measured to check that it was possible to machine them to size. All of the castings except for one were generous in size. The cylinder casting in its rogh state was a little under size in width. This wouldn't be a problem. So a start was made roughing out the castings before getting down to exact sizes.
Photographs of rough out the castings.
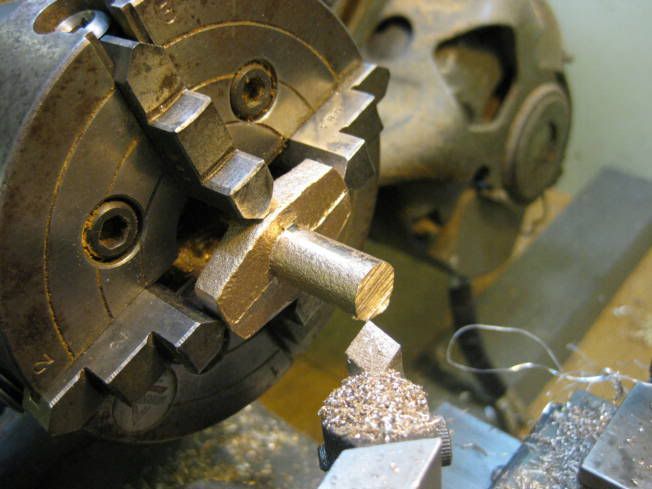
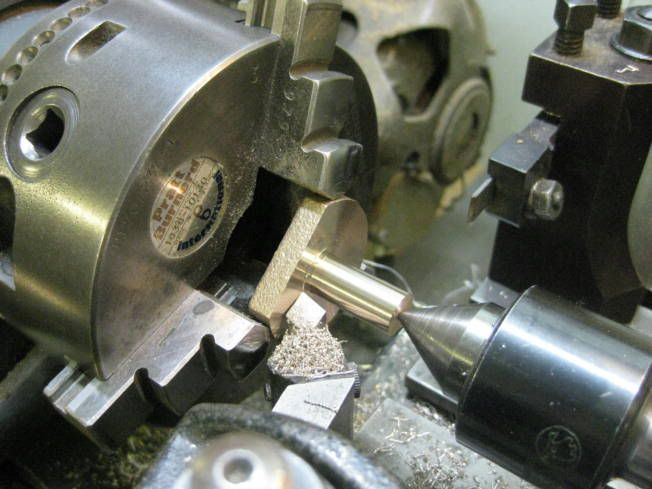
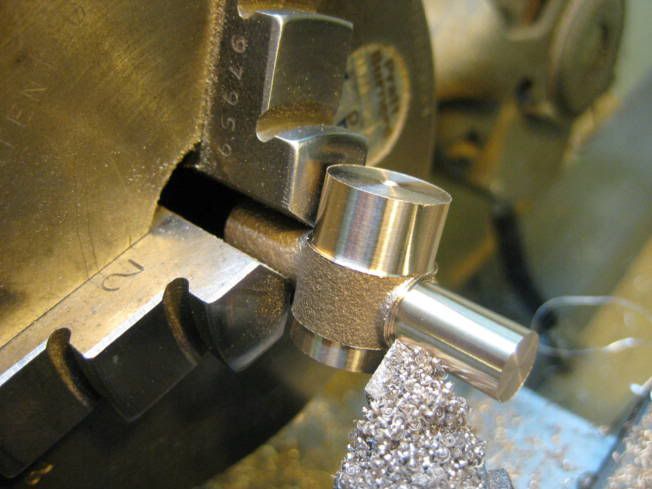
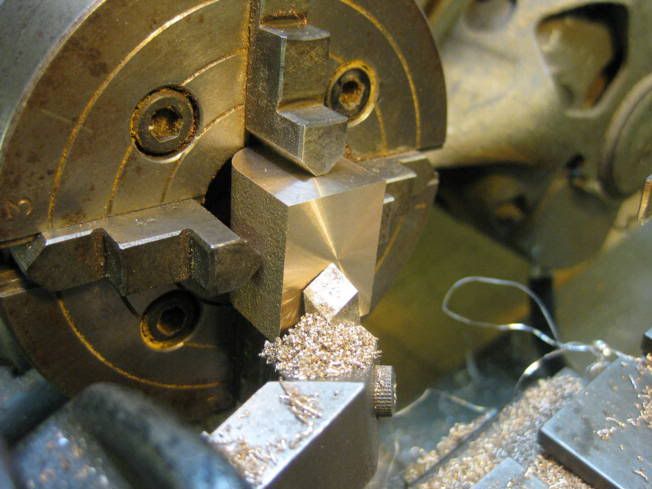
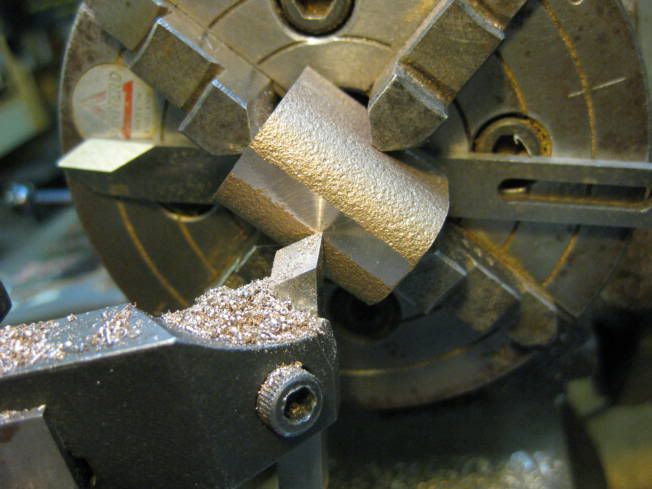
Wax chucks were used for the flat bits.
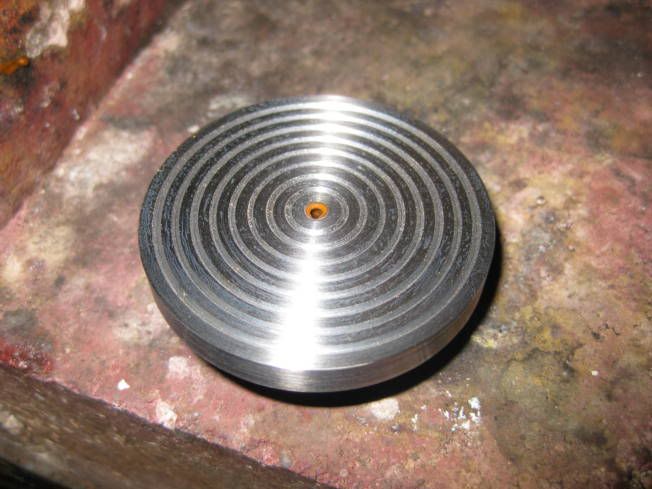
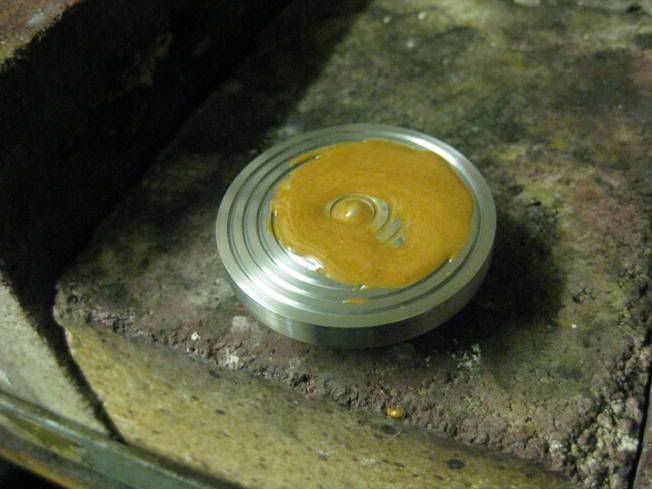
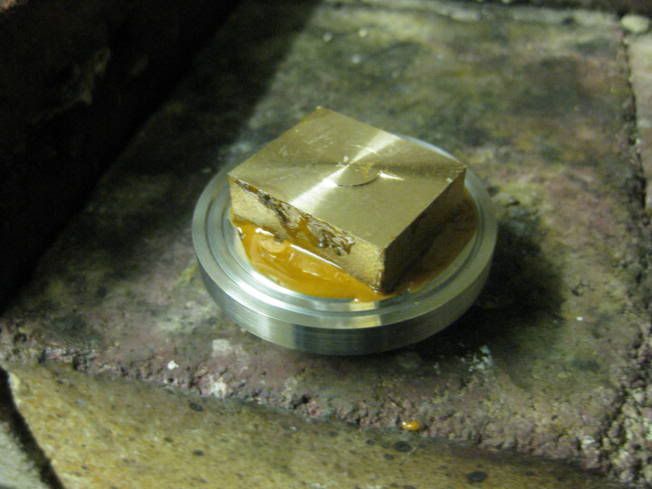
Some more photographs to follow.
Regards Tony.