- Joined
- Jul 16, 2007
- Messages
- 2,986
- Reaction score
- 1,055
When I first built my 4 cylinder OHV engine I made the simplest exhaust for a few reasons. First, I had tried to bend tubing with automotive type benders and didn't have much luck. Second, I wanted to use stainless steel and trying to bend this material was way more than I had experience for. I have since built a tubing bender for small sized tube and have had fairly good luck but mainly with brass and copper tubing. I ordered some 316 thin walled stainless tubing, .250 OD x .025 wall thickness. This was as close as I could come to my port size although I would have liked a little thicker wall. I think it might have bent smoother but I'll get into that as I go along. The description of the tubing said it could be bent and flared with the 'right' tools. The first set of pictures shows bending the tubing with my small bender. I started out with a 1.00 diameter die but the tubing just wouldn't go around that size so I made a quick new one out of brass. I upped the diameter to 1.50. This seemed to work better although it left a slight flat on the outside. When I removed the tubing from the bender and measured across the bend it was still .253 just like the tubing diameter. I can only surmise that the tubing wasn't soft enough and rather than stretch it just flattened out the outside wall. The inside radius was perfect.
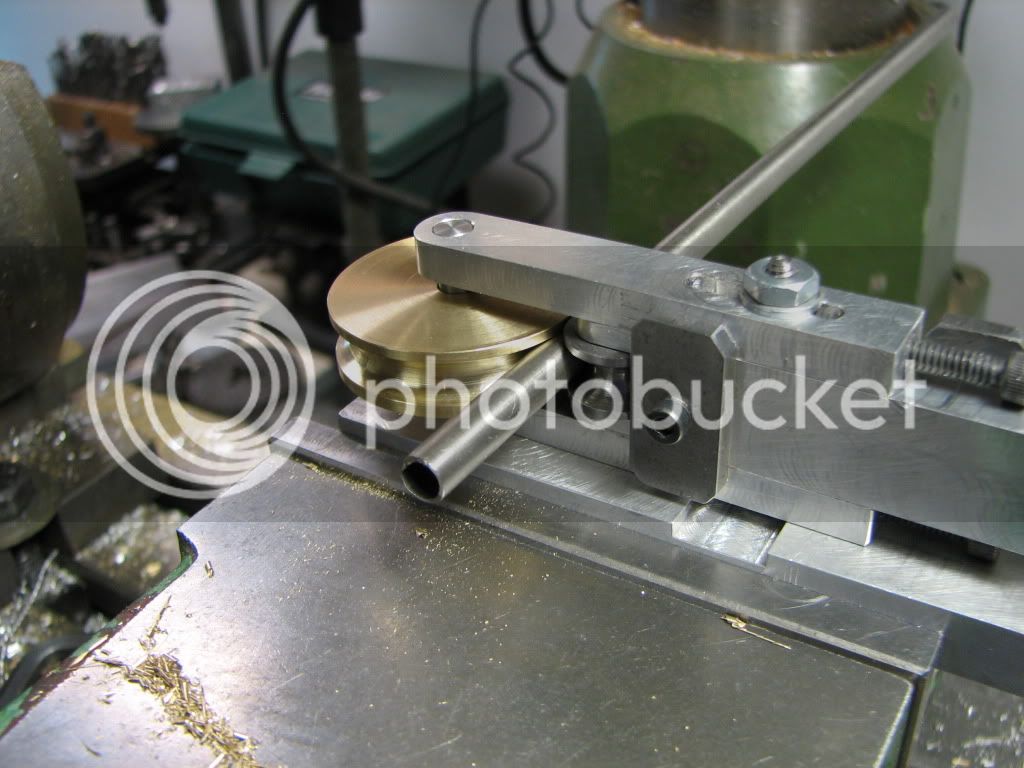
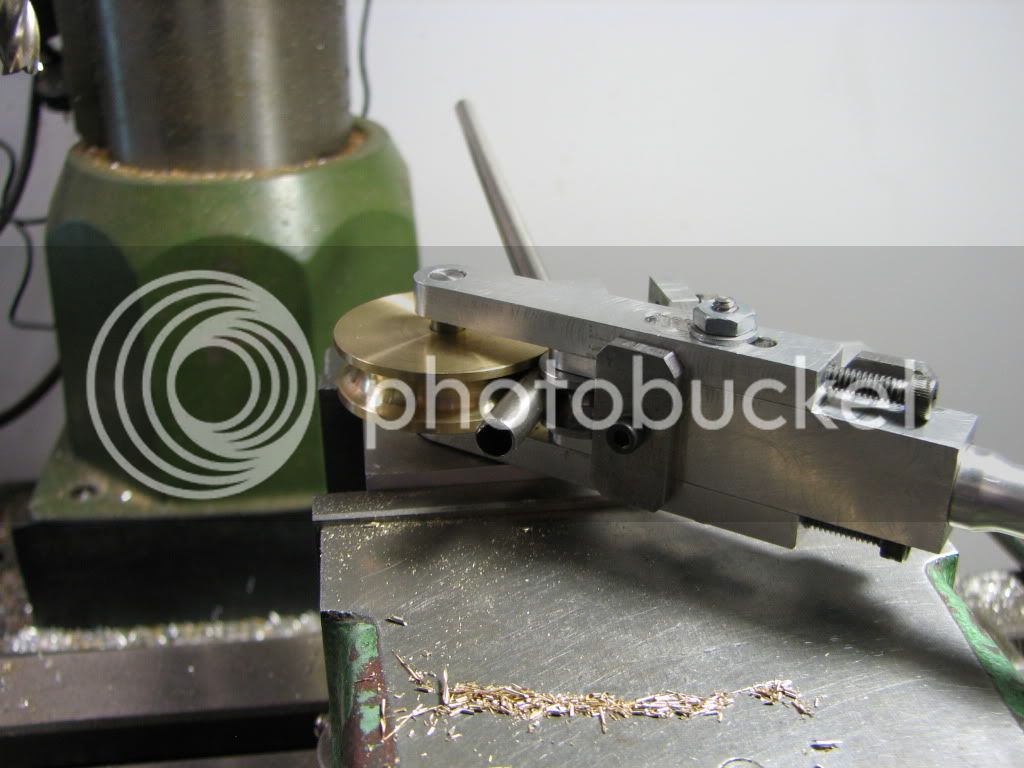
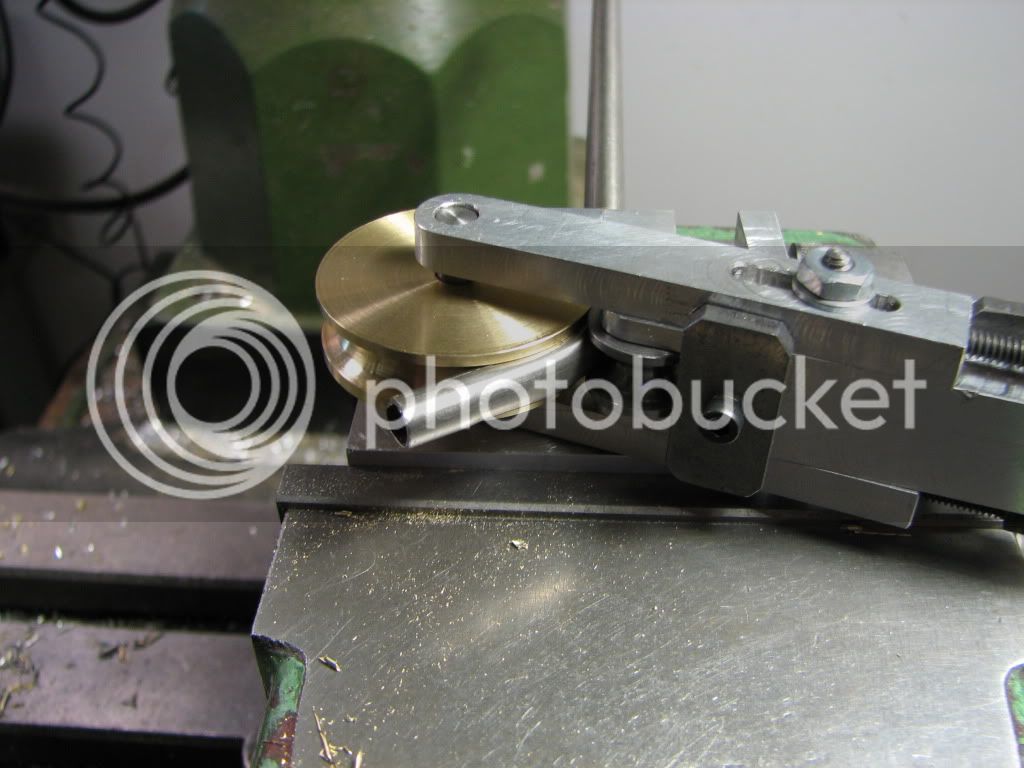
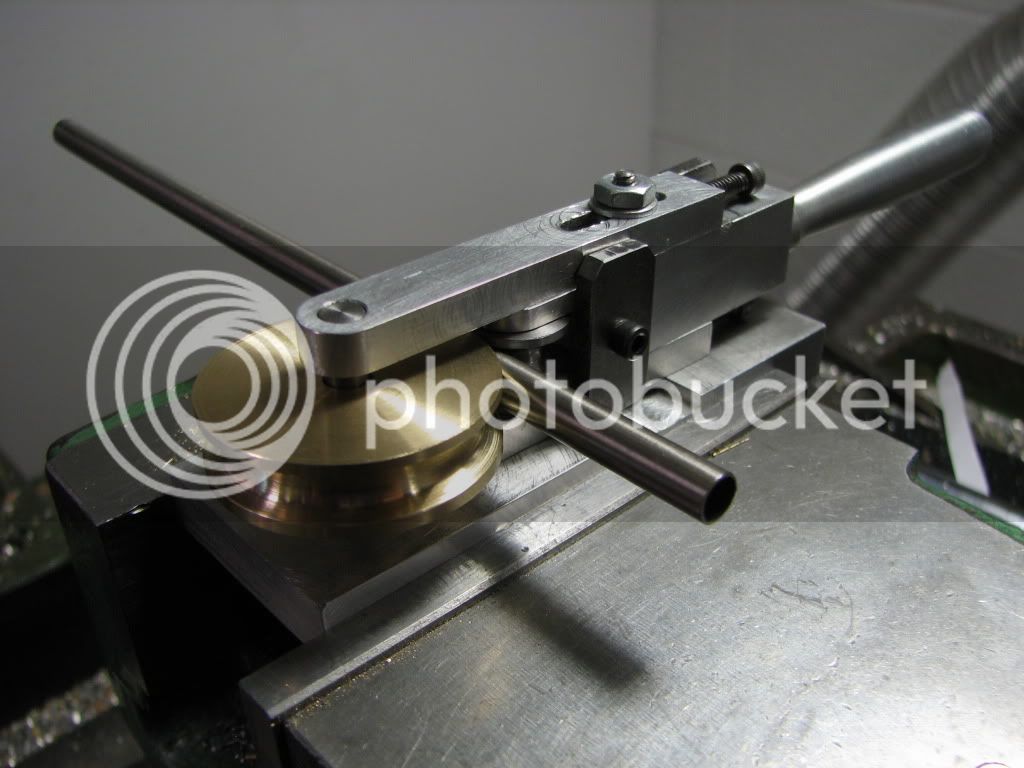