Oh no, why have I started another project before i've finished the previous two? Well, it was Jan Ridder's fault again! He recently posted his Micro Stirling Engine on his website - I had to see it so asked for the plans, which he was very kind to send to me. The problem is, I just don't like making stuff from other peoples plans blindly! It never seems to suit my materials or processes so I have to change things - but I probably go too far.
This time I've tried to combine the best ideas from Jan's and another engine I found on youtube - see below:
http://heetgasmodelbouw.ridders.nu/Webpaginas/pagina_stirling_1_euro_10/frameset.htm
[ame]http://www.youtube.com/watch?v=dAV_nWTwWR4[/ame]
Mine is going to end up a little larger than these two mainly to make things a bit easier for myself and what I have to hand, it should also give it a slightly better chance of running.
I have done the CAD model which took a bit of working out and have now completed the 2D drawings. I did calculations to ensure the ratio of swept volumes between displacer piston and power piston are almost the same - this is quite important as it largely governs the temperature difference the engine can run on, of course there are a lot of other factors but I think this engine should work.
Please see attachment for the 3D model.
Tonight I started cutting first metal - A slightly frustrating night but it has yielded 1 component - I started off collecting some materials together but then got bored of that so started turning the bottom displacer cover or hot plate as I've called it on my drawings. I quickly realised that because of the thin register I need to turn that and part it off a longer piece of stock. I have some cast gunmetal that I'm using. The slither that I had planned to use has now ended up as the flywheel! This means I've already deviated from my drawings, when I felt the weight of the aluminium I'd planned to use for the flywheel I thought it was too light, so I thought I'd use the cast gunmetal and thicken it up by 1/16" to 1/4" thick. The diameter has ended up as 1.22" or something rather than the 1.5" I had originally planned. Actually, this now seems a bit heavier than I thought so may have to do the ally one after all but maybe keep the 1/4" thickness, then it might be heavy enough.
Anyway, here it is:
The cake is 2nd hand, my 2 year old son licks the icing off but he didn't do a very good job on this one so waste not want not!
Feel a bit disappointed that that's all I managed in a night but at least it's done. As I said, it deviates from the drawing in size and material. I couldn't be bothered to find / change tools etc either so the recess isn't quite right. I think I will modify the drawing just to widen the alloy flywheel. Unless this one works then I'll change it to brass. The plan is just to loctite it to the crankshaft - just easier for this little engine, it'll have no power so won't come loose.
This is probably the 2nd most complex part on the engine so at least it's a start.
Nick
View attachment Assembly.pdf
This time I've tried to combine the best ideas from Jan's and another engine I found on youtube - see below:
http://heetgasmodelbouw.ridders.nu/Webpaginas/pagina_stirling_1_euro_10/frameset.htm
[ame]http://www.youtube.com/watch?v=dAV_nWTwWR4[/ame]
Mine is going to end up a little larger than these two mainly to make things a bit easier for myself and what I have to hand, it should also give it a slightly better chance of running.
I have done the CAD model which took a bit of working out and have now completed the 2D drawings. I did calculations to ensure the ratio of swept volumes between displacer piston and power piston are almost the same - this is quite important as it largely governs the temperature difference the engine can run on, of course there are a lot of other factors but I think this engine should work.
Please see attachment for the 3D model.
Tonight I started cutting first metal - A slightly frustrating night but it has yielded 1 component - I started off collecting some materials together but then got bored of that so started turning the bottom displacer cover or hot plate as I've called it on my drawings. I quickly realised that because of the thin register I need to turn that and part it off a longer piece of stock. I have some cast gunmetal that I'm using. The slither that I had planned to use has now ended up as the flywheel! This means I've already deviated from my drawings, when I felt the weight of the aluminium I'd planned to use for the flywheel I thought it was too light, so I thought I'd use the cast gunmetal and thicken it up by 1/16" to 1/4" thick. The diameter has ended up as 1.22" or something rather than the 1.5" I had originally planned. Actually, this now seems a bit heavier than I thought so may have to do the ally one after all but maybe keep the 1/4" thickness, then it might be heavy enough.
Anyway, here it is:
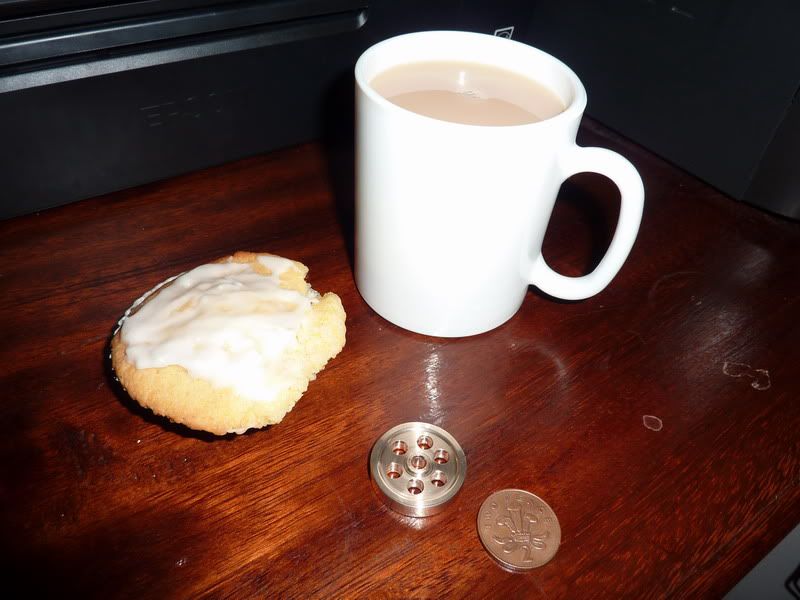
The cake is 2nd hand, my 2 year old son licks the icing off but he didn't do a very good job on this one so waste not want not!
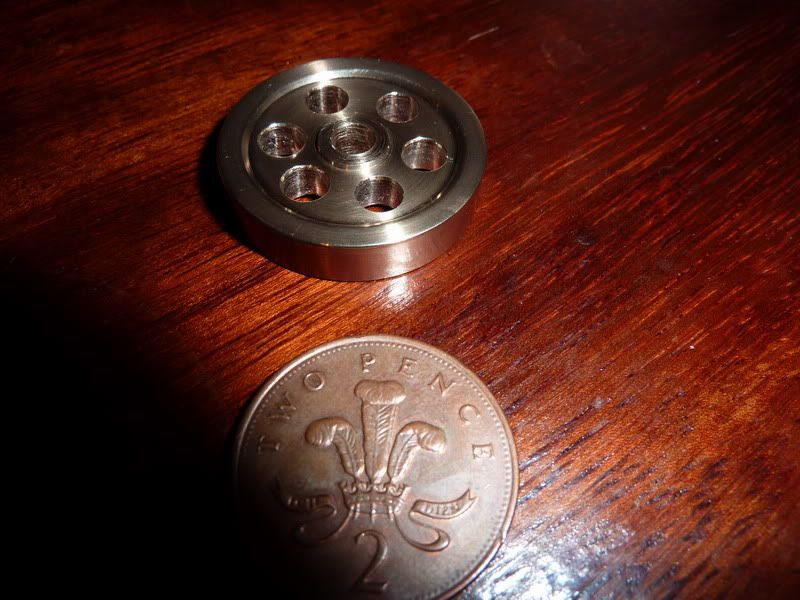
Feel a bit disappointed that that's all I managed in a night but at least it's done. As I said, it deviates from the drawing in size and material. I couldn't be bothered to find / change tools etc either so the recess isn't quite right. I think I will modify the drawing just to widen the alloy flywheel. Unless this one works then I'll change it to brass. The plan is just to loctite it to the crankshaft - just easier for this little engine, it'll have no power so won't come loose.
This is probably the 2nd most complex part on the engine so at least it's a start.
Nick
View attachment Assembly.pdf