- Joined
- Jan 17, 2009
- Messages
- 887
- Reaction score
- 81
Hi Chaps
This is a slight diversion from my Loco build but I've been wanting to build a finger engine for some time and kept my eys open for ideas that would add a bit of interest to the build. I saw thread on her where the chap added some engine turning to a horizontal engine that looked real nice this set the little grey cells going. :scratch:. Then on one of my scouting trips to the scrappy I spotted these
The scrap man saw scrap I saw flywheels.
First job clean up one of those discs
Then grind up a form tool out of a broken cutter, to use as a flycutter.
Then set my indexer over 5 deg, and mount a chunk of 2 3/4" dia ally in the chuck, that ally is way too long but I didn't want to cut it down and wast material as I'm planning on using it on another job.
This is the set up for flycutting flutes across the face with that formed flycutter. Th angle plate is to support the bar against the push from the cutter.
And this is the result 36 flutes across the face of the bar.
And this is what it will look like as a fly wheel hub.
Have fun
Stew
View attachment Potty Finger Engine Sh1-Model.pdf
View attachment Potty Finger Engine Sht 2-Model.pdf
View attachment Potty Finger Engine Sht 3-Model.pdf
View attachment Potty finger Engine Sht 4-Model.pdf
This is a slight diversion from my Loco build but I've been wanting to build a finger engine for some time and kept my eys open for ideas that would add a bit of interest to the build. I saw thread on her where the chap added some engine turning to a horizontal engine that looked real nice this set the little grey cells going. :scratch:. Then on one of my scouting trips to the scrappy I spotted these
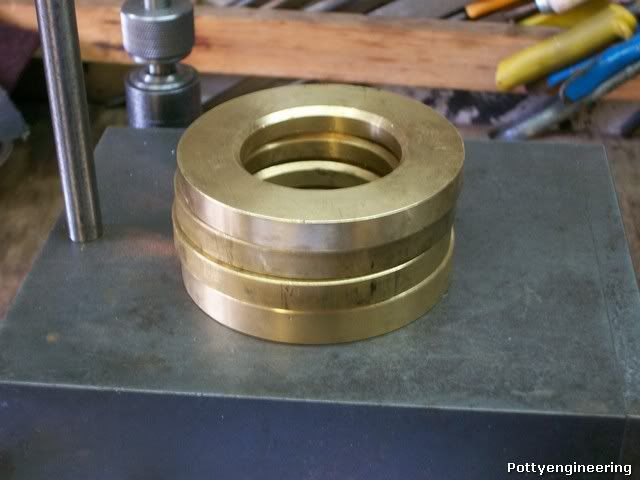
The scrap man saw scrap I saw flywheels.
First job clean up one of those discs
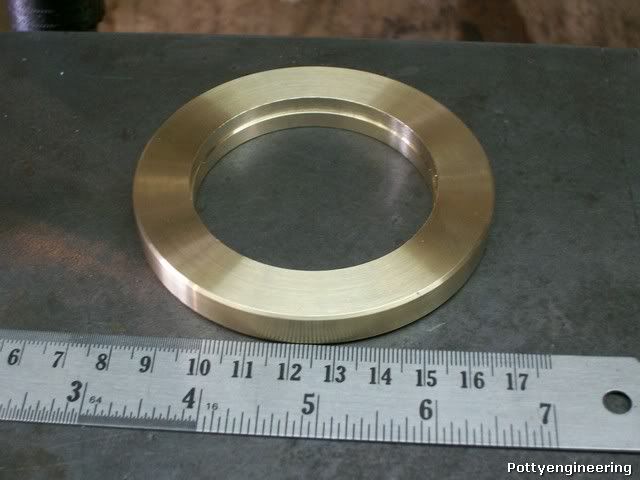
Then grind up a form tool out of a broken cutter, to use as a flycutter.
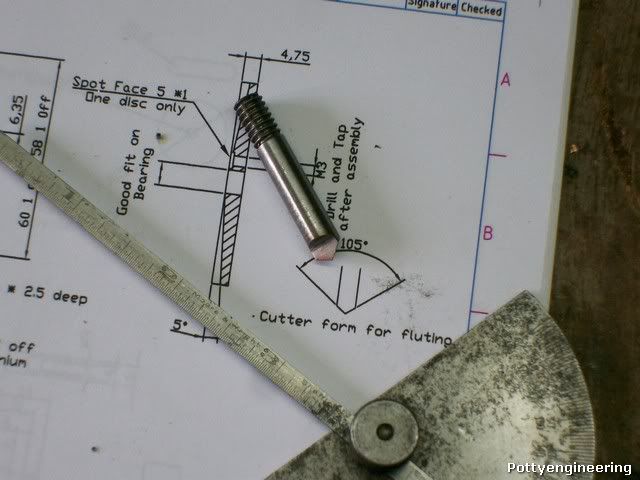
Then set my indexer over 5 deg, and mount a chunk of 2 3/4" dia ally in the chuck, that ally is way too long but I didn't want to cut it down and wast material as I'm planning on using it on another job.
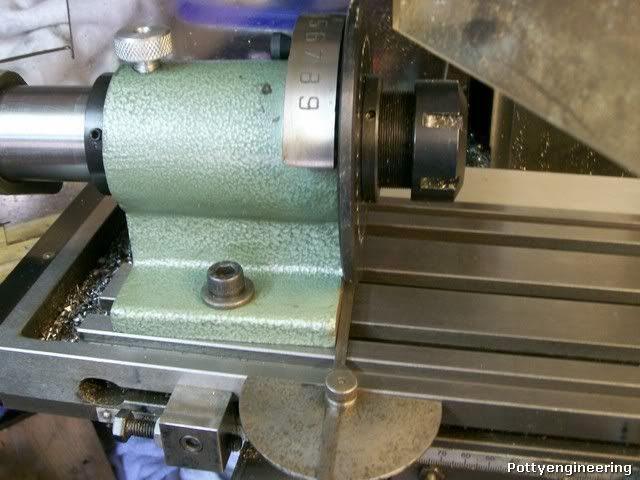
This is the set up for flycutting flutes across the face with that formed flycutter. Th angle plate is to support the bar against the push from the cutter.
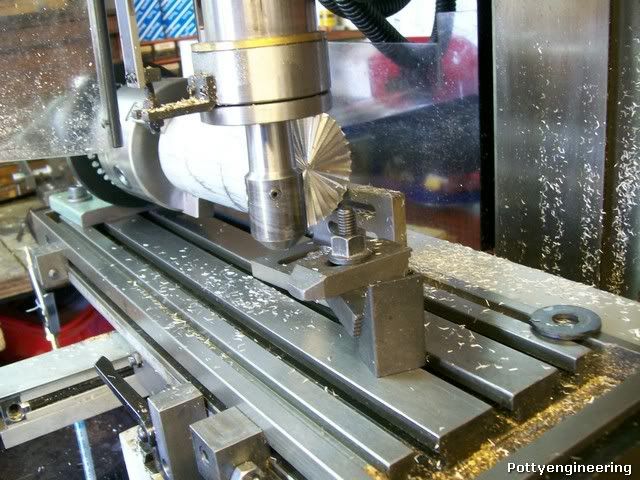
And this is the result 36 flutes across the face of the bar.
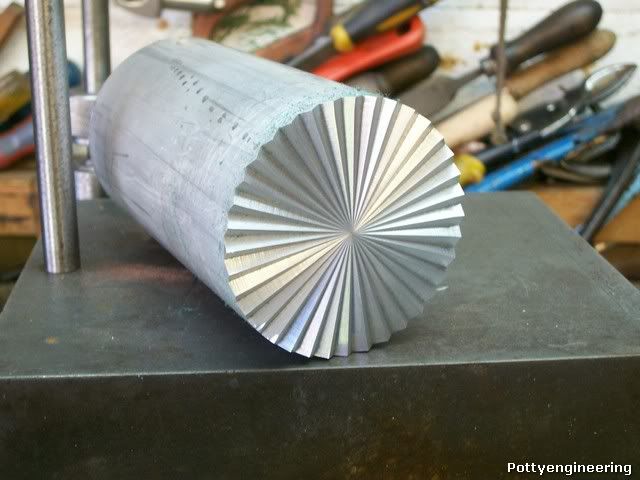
And this is what it will look like as a fly wheel hub.
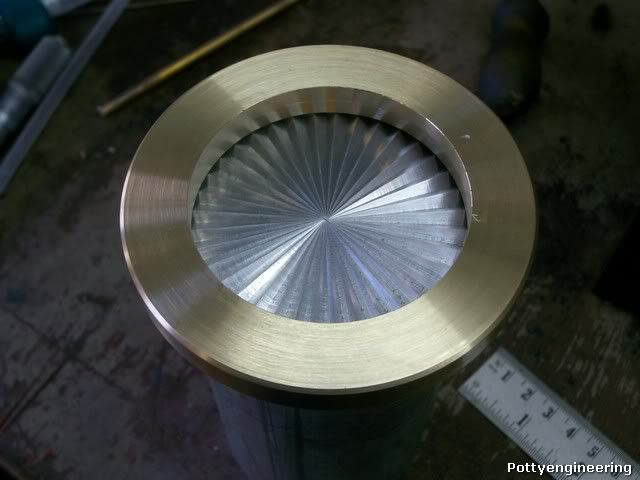
Have fun
Stew
View attachment Potty Finger Engine Sh1-Model.pdf
View attachment Potty Finger Engine Sht 2-Model.pdf
View attachment Potty Finger Engine Sht 3-Model.pdf
View attachment Potty finger Engine Sht 4-Model.pdf