Okay---the jury has decided. It is going to be an aluminum cylinder with pressed in steel pivots. I have had to do a few strange and wonderful things to accomplish this. The engine as originally designed had a 4.5:1 compression ratio, and a 1" bore. I determined that when the piston is at top dead center, it stops .050" before the side of the pivot hole in the side of the cylinder. So--I reduced the diameter of the bore to 7/8" from the outboard end of the cylinder to .025" past the hole for the pivot. That gives me an extra .062" of wall thickness to hold the pressed in pivot pins in place, and still leaves .025" clearance between the top of the point where the 1" diameter piston stops it's upward travel and the beginning of the reduced bore diameter. This of course increased the compresion ratio to a higher number. Fortunately, the original design had the inside of the cylinder head extending down into the cylinder itself by a considerable amount. I was able to shorten this intrusion into the cylinder by a sufficient amount to restore the compression ratio to what it should be.
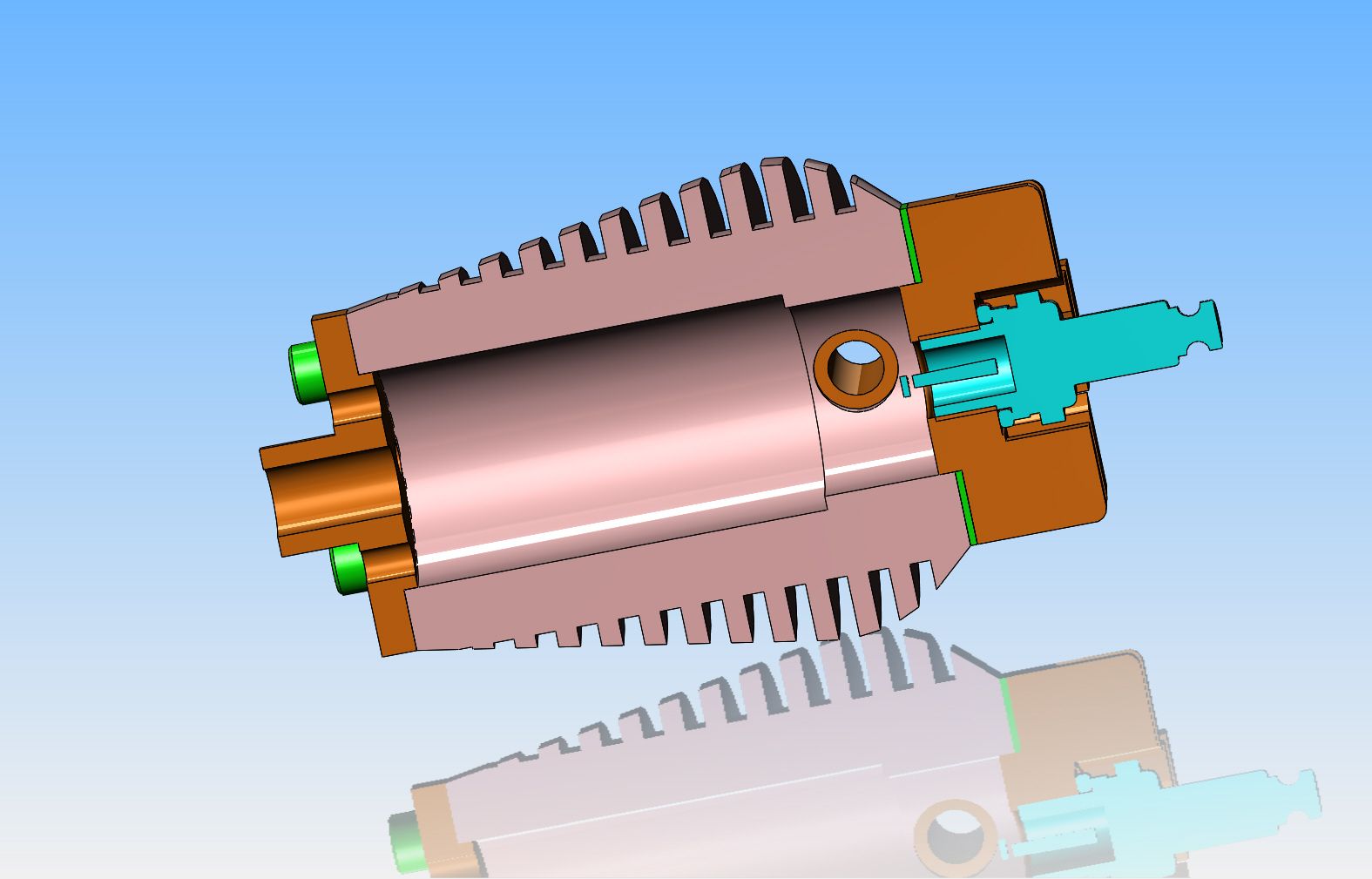