michaelj199
Active Member
- Joined
- Aug 27, 2011
- Messages
- 26
- Reaction score
- 13
I have been working on designing a V8 two stroke glow engine with a .5in bore and stroke. I plan on starting work on this engine as directed project for collage.
since i don't know much cause I'm just starting out in the machining world, i thought id run it buy you guys for your advice. i know i shouldn't be attempting a V8 but what can i say...
It's a very simple (for the most part) design. I'm not going for pretty I'm hope for running.
The engine is Two stroke based off a Detroit diesel. therefor a supercharger. im going with a rotary valve setup for "simplicity". the crank is modular steel discs and drill rod held together by square holes.
more details to come...
since i don't know much cause I'm just starting out in the machining world, i thought id run it buy you guys for your advice. i know i shouldn't be attempting a V8 but what can i say...
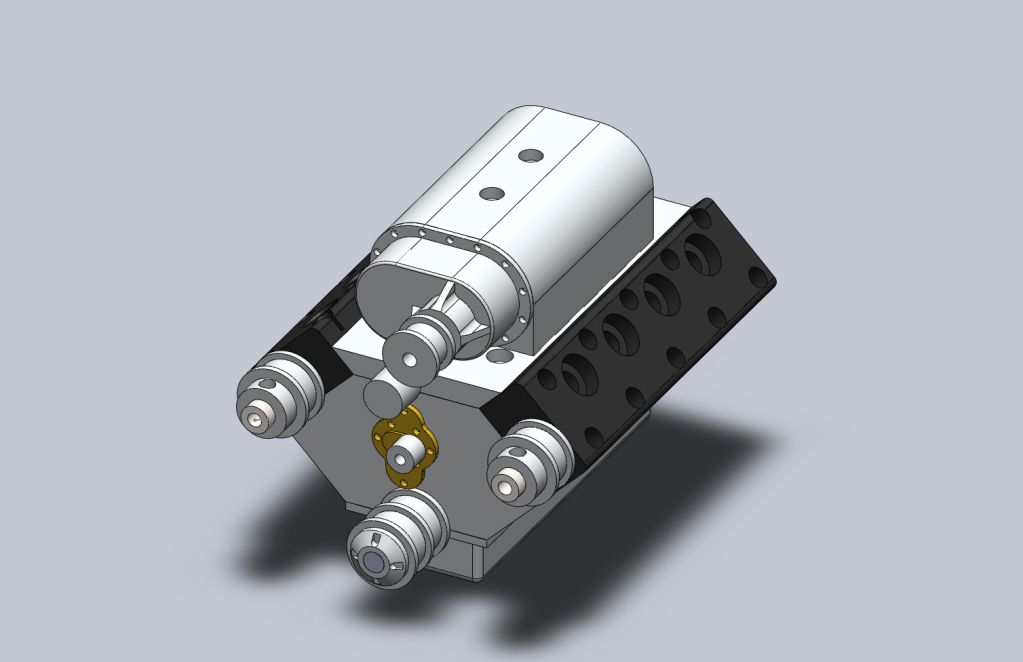
It's a very simple (for the most part) design. I'm not going for pretty I'm hope for running.
The engine is Two stroke based off a Detroit diesel. therefor a supercharger. im going with a rotary valve setup for "simplicity". the crank is modular steel discs and drill rod held together by square holes.
more details to come...
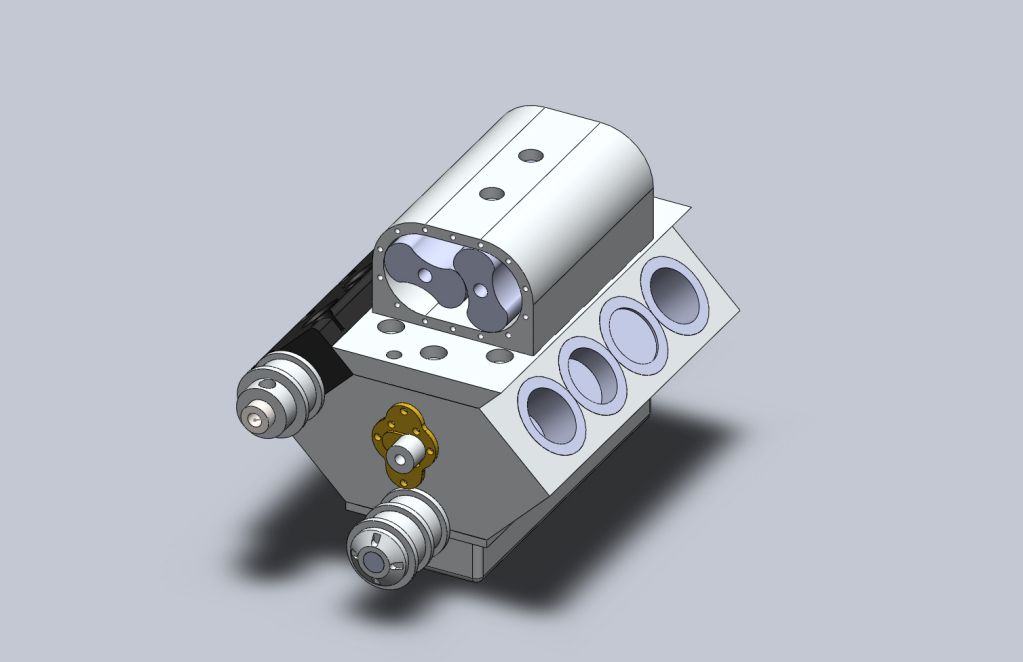
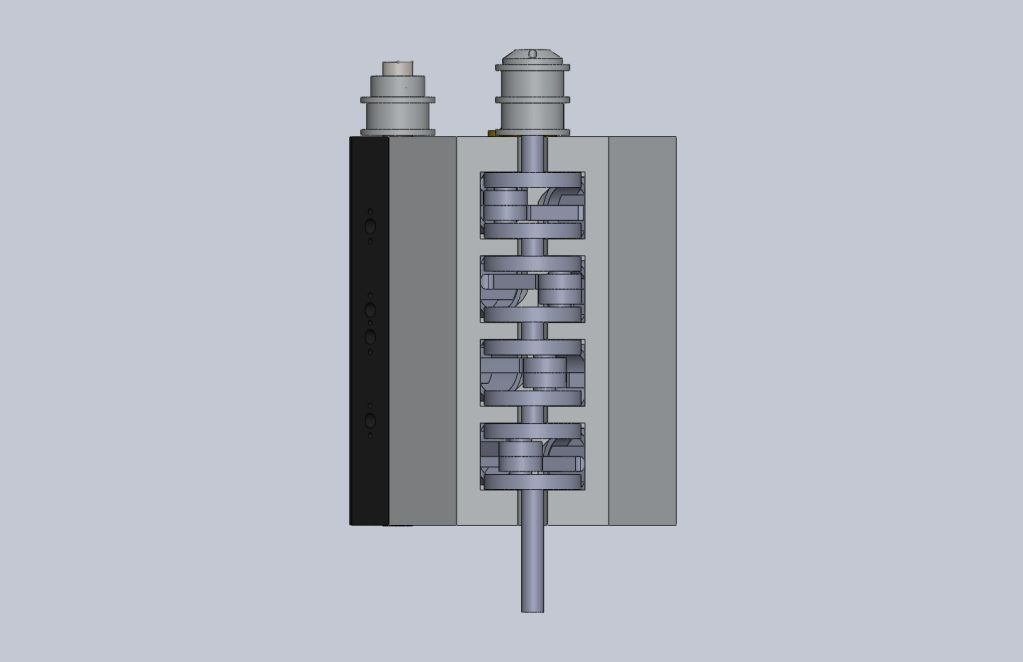
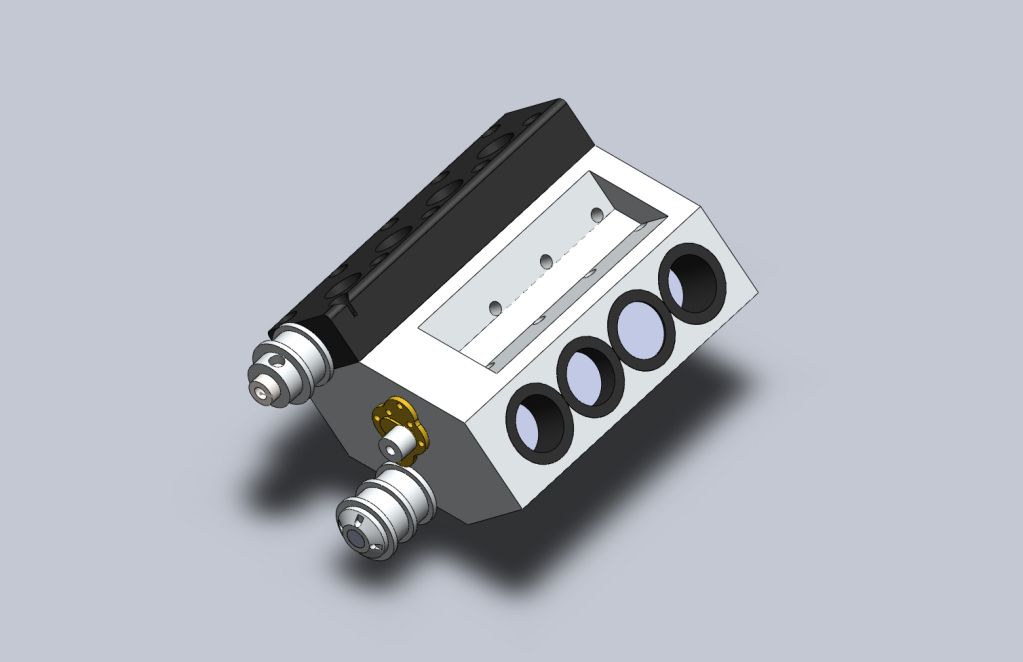
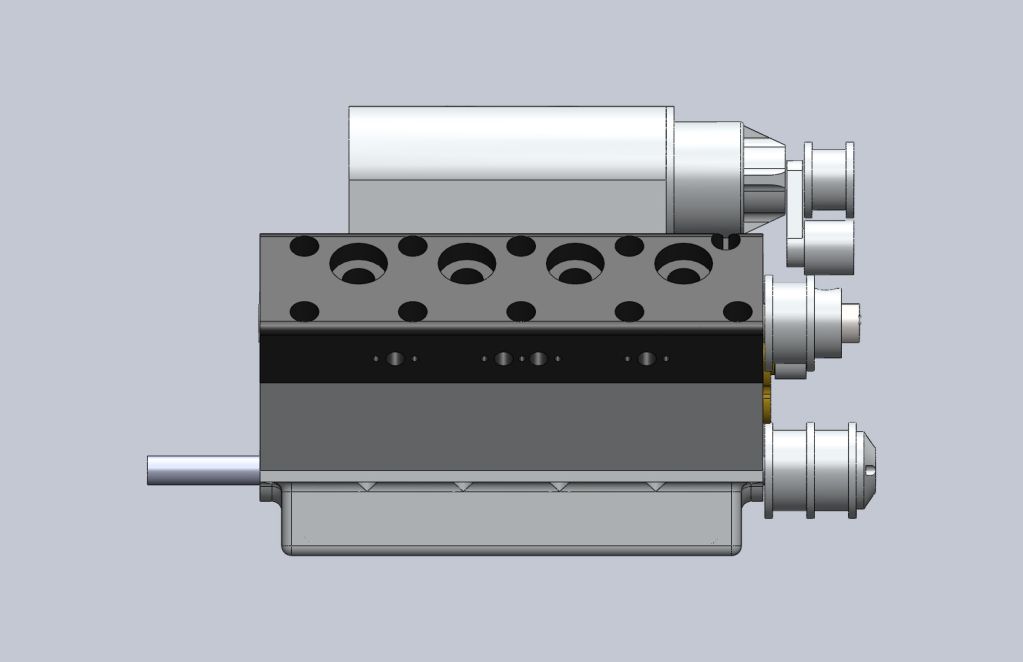