Hello all,
Well I took the plunge and bought an Economy casting kit. Been doing fine so far until the cylinder and hopper.
The first problem was boring the cylinder. Tried first with the work in the lathe and the boring head in the tailstock. To much chatter, so I honed the chatter marks out and rethought things, and ended up with the boring head in the mill, with much better results.
My first question. The bore spec is 1.125. How far should I bore before using a 1 1/8 chucking reamer?
The second problem is locating the cylinder in the hopper. The holes are egged shaped on both ends. I know the dimension from the bottom up to the center line, and the dimension side to side for centerline, but with an egg shaped hole, how do I find center to start boring for the cylinder sleeve??
I've looked and thought about it for a while now, but can't see the forest for the trees. Don't want to blow it on such an important placement.
Thanks in advance
Lance
Well I took the plunge and bought an Economy casting kit. Been doing fine so far until the cylinder and hopper.
The first problem was boring the cylinder. Tried first with the work in the lathe and the boring head in the tailstock. To much chatter, so I honed the chatter marks out and rethought things, and ended up with the boring head in the mill, with much better results.
My first question. The bore spec is 1.125. How far should I bore before using a 1 1/8 chucking reamer?
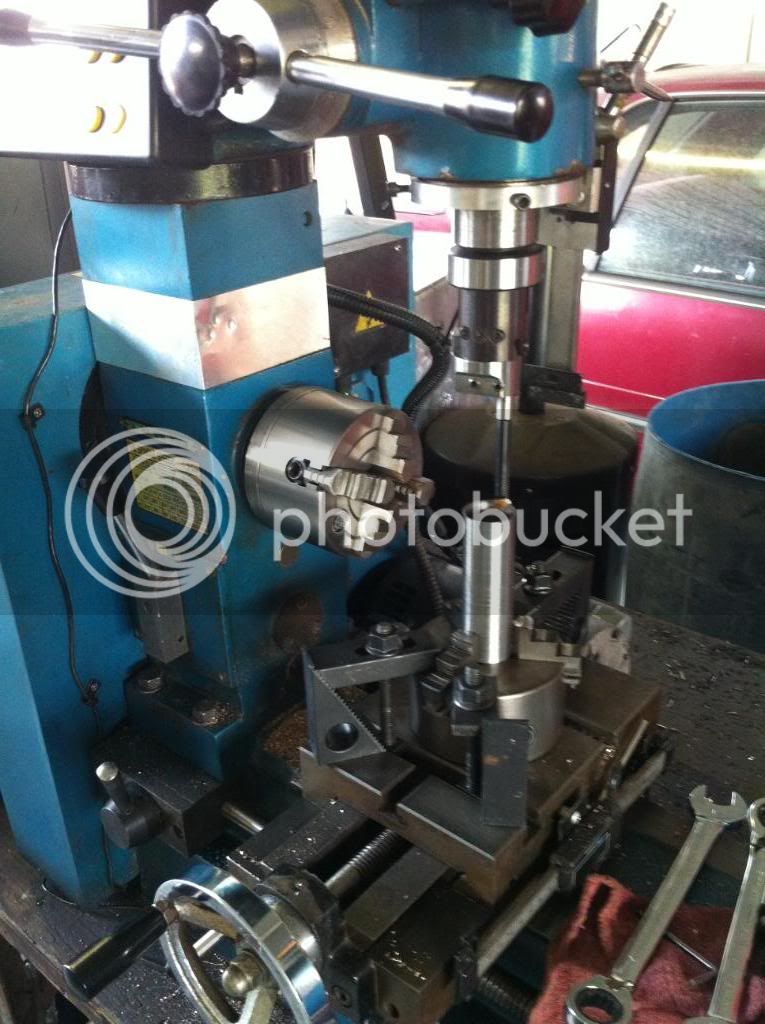
The second problem is locating the cylinder in the hopper. The holes are egged shaped on both ends. I know the dimension from the bottom up to the center line, and the dimension side to side for centerline, but with an egg shaped hole, how do I find center to start boring for the cylinder sleeve??
Thanks in advance
Lance
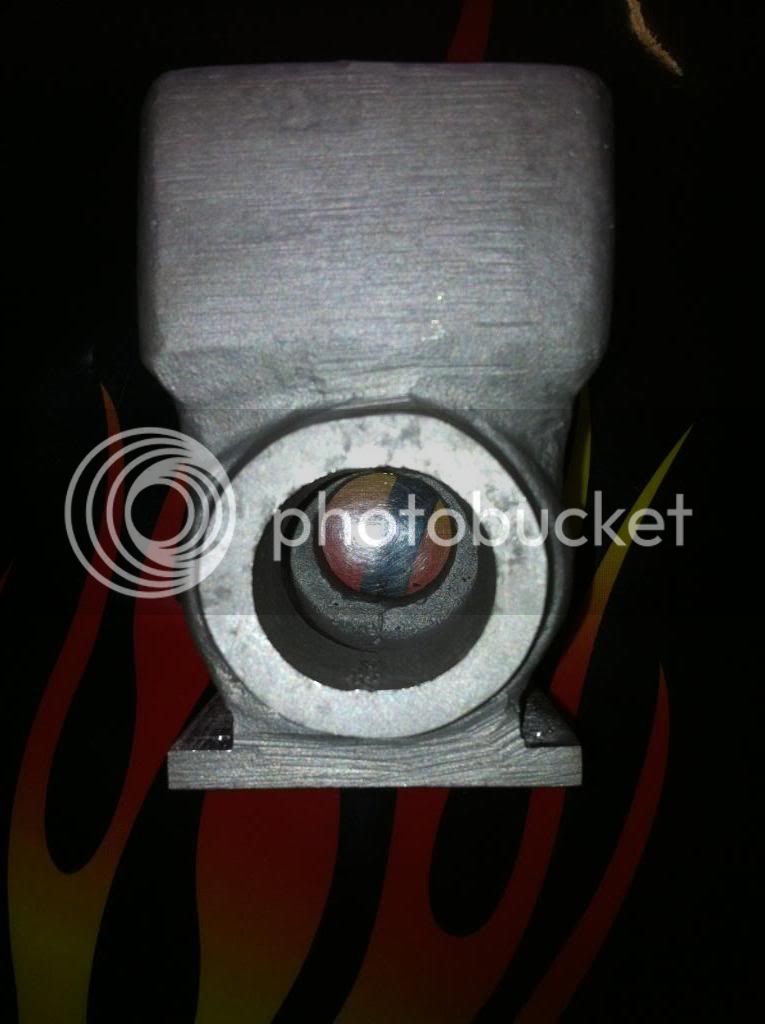