This is all Chucks fault!!! He's got me thinking about this, and I can't get it out of my head. This is an air cylinder that has a lot in common with a cannon. It is horribly dangerous, and loud, and may have no practical application in "model world".---BUT---If you could use it on an air powered hit and miss engine like Chuck has designed, it would make an awesome hit and miss engine. Basically, what happens is that when air is applied to the cap end of the cylinder, it pressurizes all of the air chambers built into the cylinders body. A small amount of this air is bled off into the top of the cylinder itself to get the piston to start moving. I have shown an adjustment screw to control how much air bleed. The piston begins to move, and after about 0.100" of travel, the piston skirt uncovers the 8 radial "air dump" holes in the cylinder wall. All of the pressure stored in those chambers rushes into the cylinder and the piston takes off at about 3000 miles per hour. This type of cylinder is not used to power rotating machinery, but is used to drive some type of Impact device, like nail guns, jack hammers, etcetera. However---If you could build a model hit and miss engine with a large enough pair of flywheels to soak up that tremendous shot of kinetic energy it would be awesome!!! These things are very dangerous, and if someone builds one and manages to hurt or kill himself or anybody else with it, I take no responsibility. Remember, there are plans on the internet to build an atomic bomb also, but its not recomended to build one in your home workshop!!! Since I am somewhat intrigued with this (at least enough to spend a morning designing instead of playing outside in the sunshine), I MAY build one myself.----Brian
View attachment ASSY BRIAN IMPACT CYL..PDF
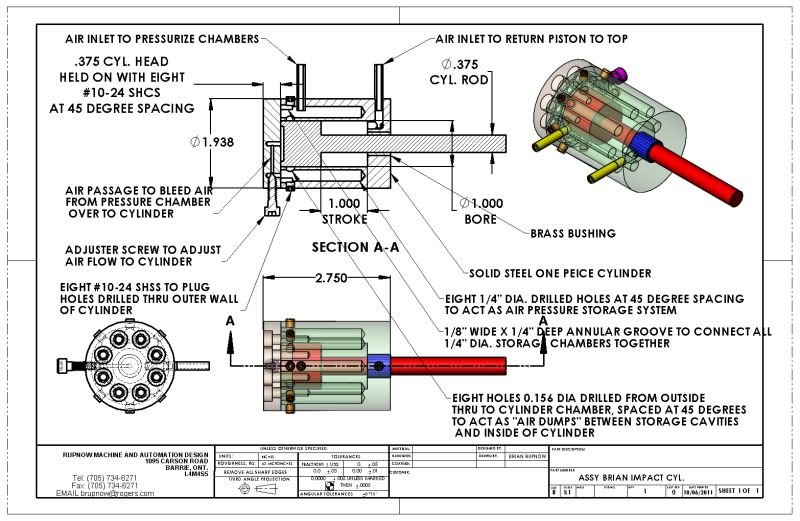
View attachment ASSY BRIAN IMPACT CYL..PDF