This was a standard 14" abrasive cut off saw, originally mounted on a small pressed metal base. A few years ago I got tired of kneeling on the floor to cut up RHS, so I dispensed with the pressed metal base and made up this trolley for the saw.
There is a drop down handle at the left hand end so I can wheel the trolley around wheelbarrow fashion.
While I was at it I made the back guide about 2' long and fitted 2 screw clamps, this helps keep long lengths of material square to the saw. Plus a tray underneath to hold small offcuts
There is a drop down handle at the left hand end so I can wheel the trolley around wheelbarrow fashion.
While I was at it I made the back guide about 2' long and fitted 2 screw clamps, this helps keep long lengths of material square to the saw. Plus a tray underneath to hold small offcuts
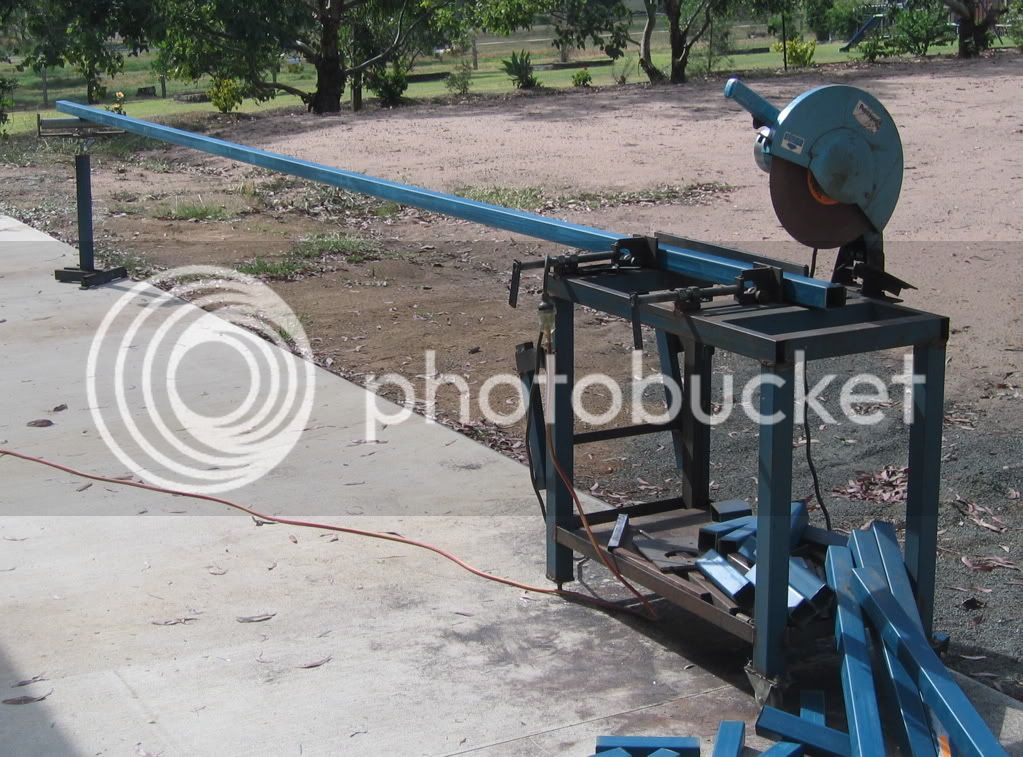