- Joined
- Jun 4, 2008
- Messages
- 3,285
- Reaction score
- 630
My Nema-1 enclosures arrived on Wednesday, so yesterday I took them and the VFD to school. The VFD will be housed in a 12x12x6 enclosure. The unit's dimensions are 3.94W x 5.94H x 5.06D, so plenty of room on all 4 sides for ventilation.
I used a transfer punch to locate two holes and drilled them in the back of the enclosure. The two mounting holes are .20" diameter, so probably M6 screws or 12-28. I'll be heading to the hardware store today for a trial fit.
The VFD's control panel is detachable from the unit and can be remoted via a 10-conductor cable. I decided to make a protective bezel for the control unit that will also serve as a mounting "bracket". I found a piece of 1" aluminum plate in the stock room that was just the right size. Mounted in the vise I used an end mill to true up the edges, then flycut the top.
Next it was time to "calibrate" my 1/8" corner-rounding bit. In order to get a smooth rounded profile with one of these bits, the X and Z offsets from the edge need to be set fairly precisely. To get the offsets, I set the bit so that it's barrel was touching the side and zeroed the X axis on the DRO. Then lowered the quill to that the flat bottom of the mill touched the top of the plate. Then I set the mill so that it was barely cutting the corner and started to make cuts, moving the X and Z in towards the work .01" at a time. Once the bit started to cut a flat edge into the side or top, I knew that I could use the previous setting. It turned out that I needed .15" in on the X and .19" in on the Z to get a good profile. Now I was able to quickly cut the profiles on all 4 of the top edges.
To mount the VFD panel I needed to cut a pocket into the top .65" deep. Measuring the dimensions of the panel and the final dimensions of the aluminum, I was able to calculate the DRO coordinates of each corner. I used a center drill to mark these before cutting; in theory this was unnecessary but I didn't want to mess up the work I;d already done. Having verified that the panel fit neatly within the 4 marked points I cut the pocket first with a 1/2" 2-flute end mill. Of course, I needed to set the DRO coordinates for the corners .25" inside.
My instructor indicated that I could make a plunge cut half the diameter of the mill, so I used three passes to cut the pocket. Then using a 1/4" 2-flute mill I was able to reduce the corner radius so that the panel would fit:
Next I used the 1/4' mill to cut out a hole in order to connect the cable:
The panel is an easy fit, perhaps .10" clearance on each side. It will be held in place with a M4 screw through the back.
I'm not sure where I will mount the panel. I'll decide when the mill is re-assembled and I find an ergonomic spot.
When I got home and opened the box containing the remote cable, I found that I'll need to make the access hole about .25" wider to accomodate the molded plug.
I used a transfer punch to locate two holes and drilled them in the back of the enclosure. The two mounting holes are .20" diameter, so probably M6 screws or 12-28. I'll be heading to the hardware store today for a trial fit.
The VFD's control panel is detachable from the unit and can be remoted via a 10-conductor cable. I decided to make a protective bezel for the control unit that will also serve as a mounting "bracket". I found a piece of 1" aluminum plate in the stock room that was just the right size. Mounted in the vise I used an end mill to true up the edges, then flycut the top.
Next it was time to "calibrate" my 1/8" corner-rounding bit. In order to get a smooth rounded profile with one of these bits, the X and Z offsets from the edge need to be set fairly precisely. To get the offsets, I set the bit so that it's barrel was touching the side and zeroed the X axis on the DRO. Then lowered the quill to that the flat bottom of the mill touched the top of the plate. Then I set the mill so that it was barely cutting the corner and started to make cuts, moving the X and Z in towards the work .01" at a time. Once the bit started to cut a flat edge into the side or top, I knew that I could use the previous setting. It turned out that I needed .15" in on the X and .19" in on the Z to get a good profile. Now I was able to quickly cut the profiles on all 4 of the top edges.
To mount the VFD panel I needed to cut a pocket into the top .65" deep. Measuring the dimensions of the panel and the final dimensions of the aluminum, I was able to calculate the DRO coordinates of each corner. I used a center drill to mark these before cutting; in theory this was unnecessary but I didn't want to mess up the work I;d already done. Having verified that the panel fit neatly within the 4 marked points I cut the pocket first with a 1/2" 2-flute end mill. Of course, I needed to set the DRO coordinates for the corners .25" inside.
My instructor indicated that I could make a plunge cut half the diameter of the mill, so I used three passes to cut the pocket. Then using a 1/4" 2-flute mill I was able to reduce the corner radius so that the panel would fit:
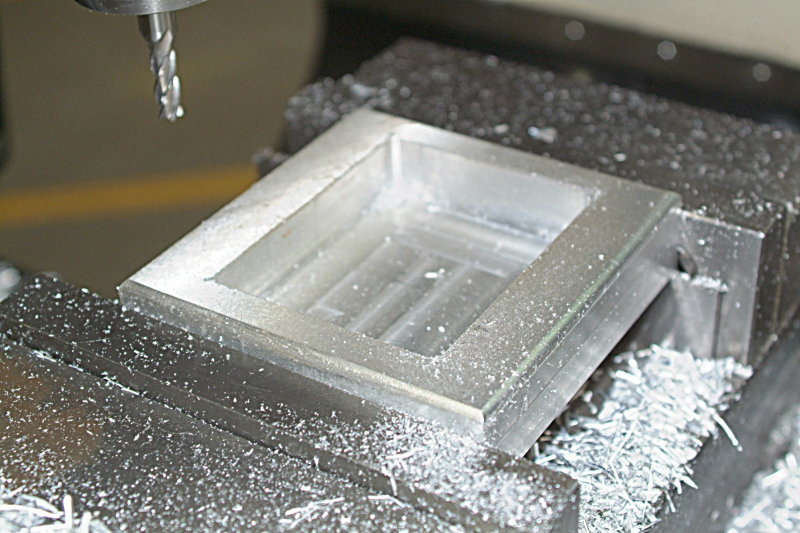
Next I used the 1/4' mill to cut out a hole in order to connect the cable:
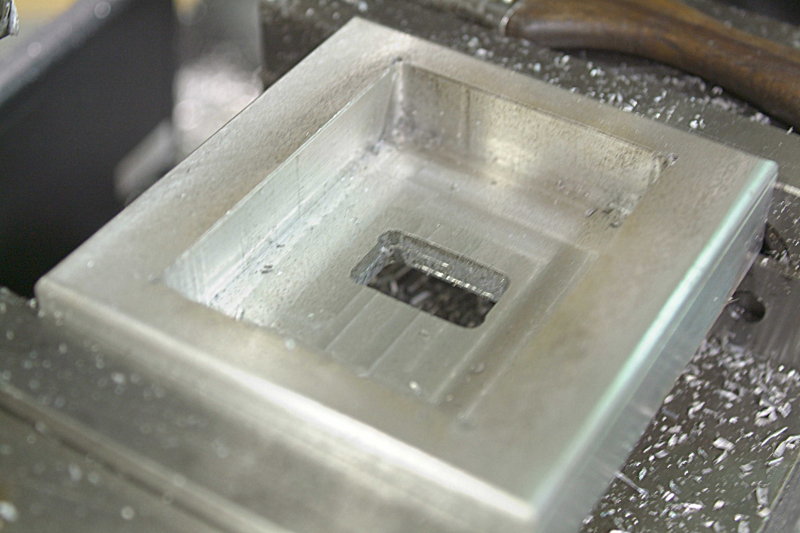
The panel is an easy fit, perhaps .10" clearance on each side. It will be held in place with a M4 screw through the back.
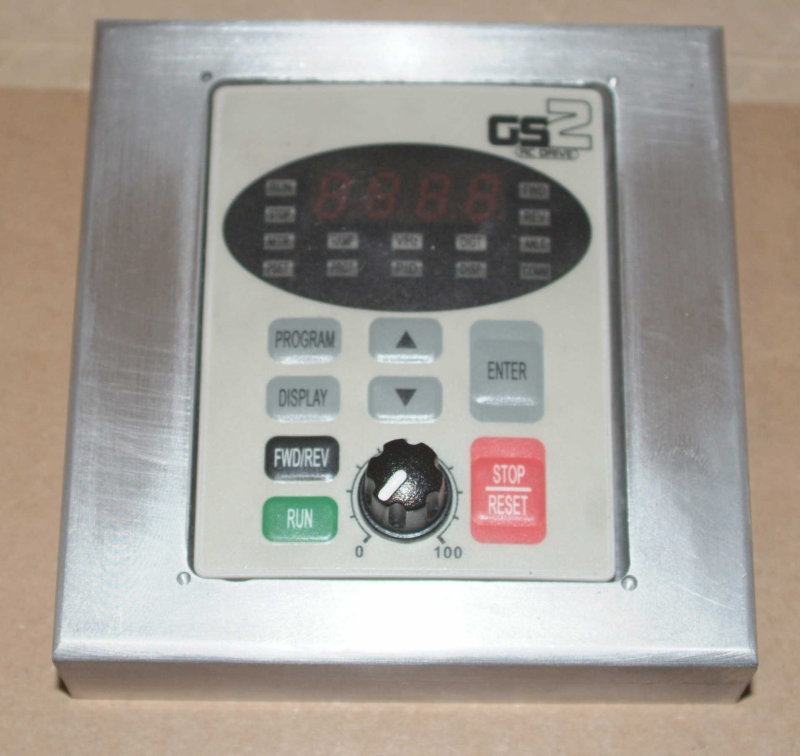
I'm not sure where I will mount the panel. I'll decide when the mill is re-assembled and I find an ergonomic spot.
When I got home and opened the box containing the remote cable, I found that I'll need to make the access hole about .25" wider to accomodate the molded plug.