Tin Falcon
Well-Known Member
- Joined
- Jul 9, 2007
- Messages
- 7,207
- Reaction score
- 788
I have been thinking about getting one of these for a few months now.
My son has been doing a bit of work on his ford ranger pressing out/in ball joints and such. and I can thing of few creative hobby uses so we picked one up today. Easy to transport in just about any vehicle it fit in the trunk of my midsize for sedan. It comes in three cartons. and assembled in I am geuseing a half hour. My son put it to use popping out a ball joint. he is chipping in on the cost of it.
12 Ton Shop Press
Central Hydraulics - Item#33497
Photo link to Harbor freight tools.
tin
My son has been doing a bit of work on his ford ranger pressing out/in ball joints and such. and I can thing of few creative hobby uses so we picked one up today. Easy to transport in just about any vehicle it fit in the trunk of my midsize for sedan. It comes in three cartons. and assembled in I am geuseing a half hour. My son put it to use popping out a ball joint. he is chipping in on the cost of it.
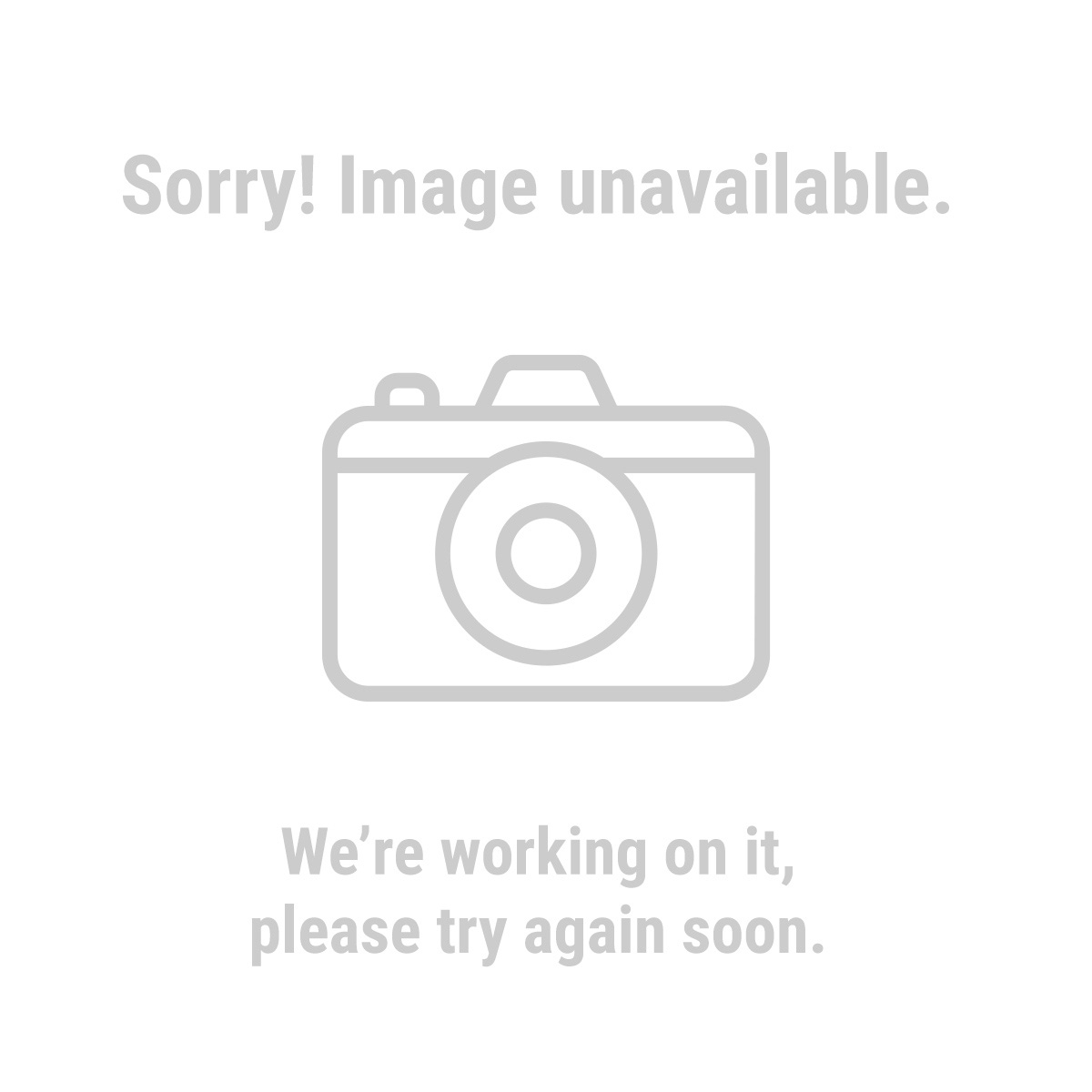
12 Ton Shop Press
Central Hydraulics - Item#33497
Photo link to Harbor freight tools.
tin