A couple of months ago, I seen on one of the forums I visit that someone had cut a worm gear by mounting a tap in the chuck of a lathe and letting an aluminum blank rotate against the rotating tap. The tap caused the blank to revolve, and with some pressure from the cross feed on the lathe actually cut "teeth" into the blank. There is still 20" of snow outside (although it is melting ) so I decided to play inside today and try this for myself. First I turned a blank to an arbitrary 1.25" outer diameter x 7/16" thick. Then I made a holder to mount it in with a piece of 5/16" cold rolled steel for an "axle", and this in turn was mounted into one of the tool=holders for my AXA toolpost.
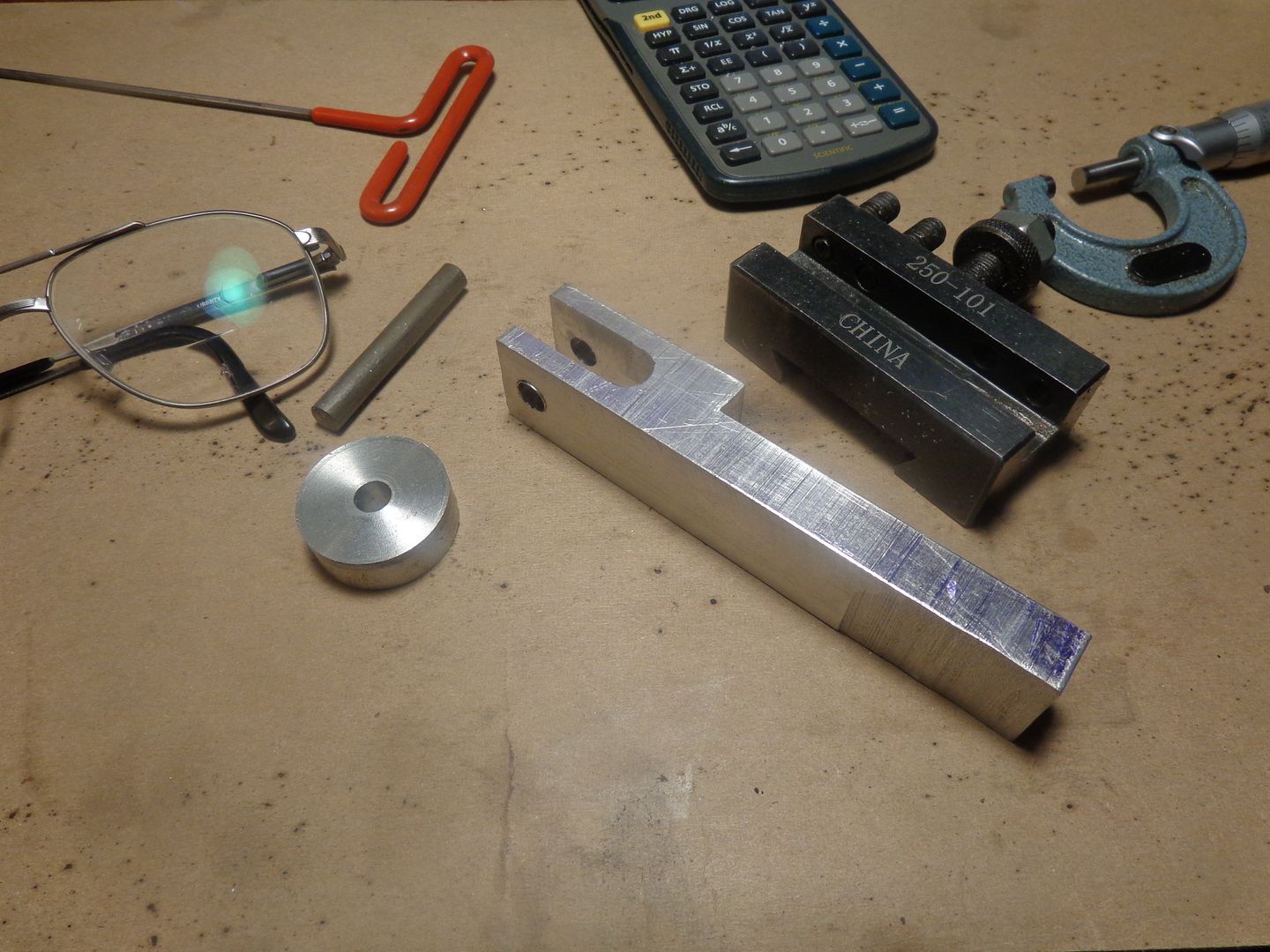
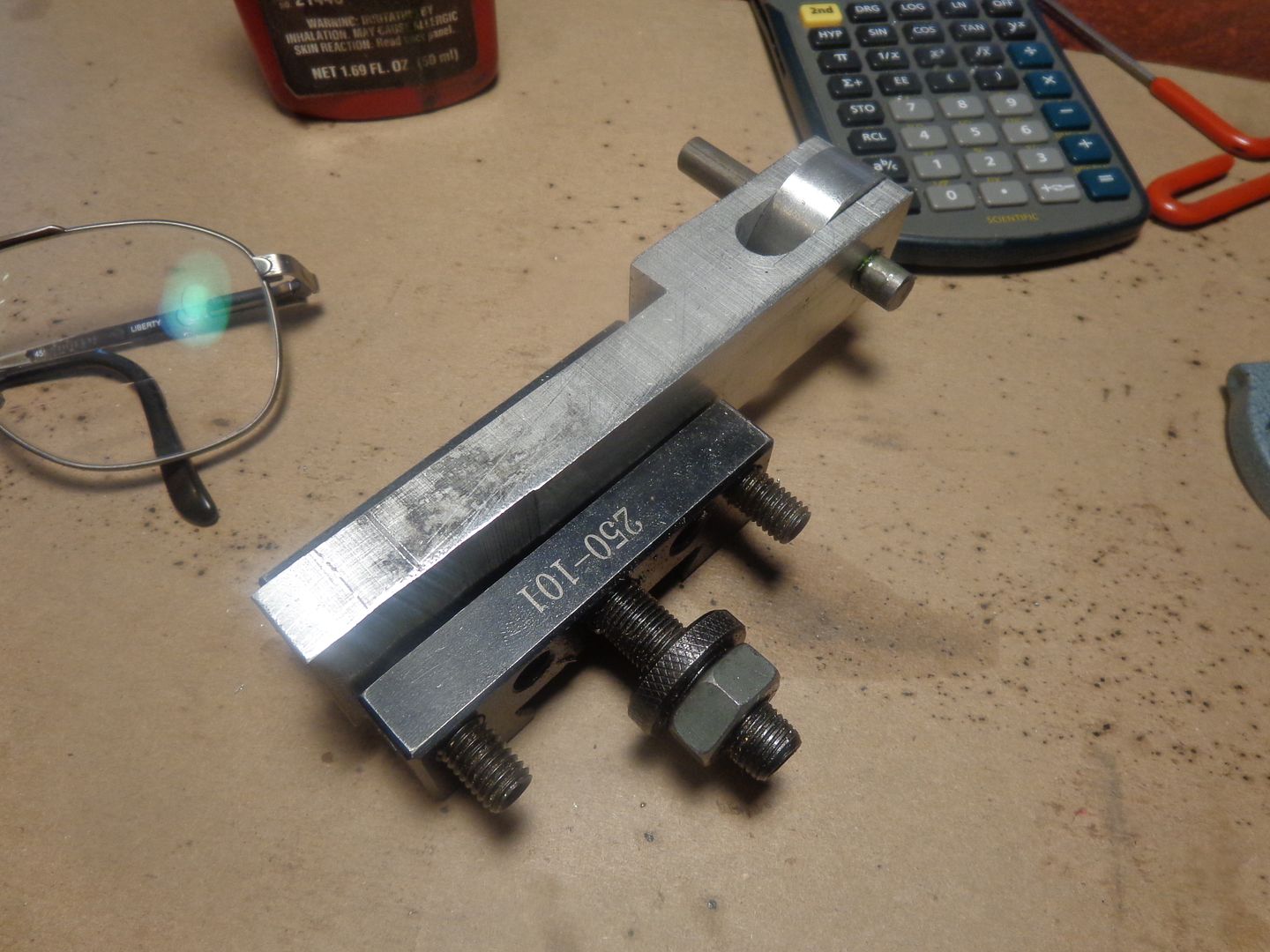