arnoldb
Well-Known Member
- Joined
- Apr 8, 2009
- Messages
- 1,792
- Reaction score
- 12
Elmer's Kimble engine has been on my to-do list for quite a while, and have literally been nagging at me to be built.
I can't seem to find any other build logs on it, and have only found one short Youtube video of one, so this is a bit of a journey into the unknown. The engine seems relatively straight-forward to build, but thinking through the processes, there are a couple of potential gotcha's - most notably that everything thing must be kept very square to prevent binding.
I have found one measurement wrong on the plans so far as well. The sizes for the mortise and tenon joint on the vane shaft does not match... A 1/4" tenon will not go into a 3/16" mortise, so those sizes I'll adjust as needed.
As usual, I'll be using whatever material I have on hand during the build - and will deviate a little from the plans in areas where dimensions does not matter.
I started on the sub-base and base today. The plans call for a 1/8" sub-base and 1/2" base, so I settled for two bits of 10mm hot rolled steel bar :big: :
The thicknesses are not important - as long as they are thick enough together to accommodate the flywheel swing.
Both bits were sawed and then milled to size, and the flat faces roughly fly-cut to get rid of all the mill scale:
A bit of lay-out on the base:
Then I clamped it to the sub-base and started drilling 3mm clearance holes for all the mounting bolts:
I wasn't feeling in the mood to mill out the entire flywheel cut-out, so I chain-drilled the end, pushed some pins through the holes to keep things matched up and then used the band saw to cut down the sides leaving about 0.5mm of metal to remove with the mill:
I just kept a careful eye on the cut to make sure it didn't stray too far. Because of the angle of the saw head, I had to stop early, and finish off the last short sections of the cuts with the saw in vertical mode.
Now, who says a shifting spanner has no place in the shop ;D - I used a small one to break out the unwanted sections from the cuts:
The cut-outs were cleaned up with a 4mm end mill; I just milled to split the mark-out line on the base:
My 4mm end mills are too short to do both the base and sub-base at the same time, so I used pins to align the base with the sub-base again and used a sharp scribe to mark the sub-base off the milled-out section from the base. Then I just milled the sub-base to those lines as well.
Stopped here for today:
Regards, Arnold
I can't seem to find any other build logs on it, and have only found one short Youtube video of one, so this is a bit of a journey into the unknown. The engine seems relatively straight-forward to build, but thinking through the processes, there are a couple of potential gotcha's - most notably that everything thing must be kept very square to prevent binding.
I have found one measurement wrong on the plans so far as well. The sizes for the mortise and tenon joint on the vane shaft does not match... A 1/4" tenon will not go into a 3/16" mortise, so those sizes I'll adjust as needed.
As usual, I'll be using whatever material I have on hand during the build - and will deviate a little from the plans in areas where dimensions does not matter.
I started on the sub-base and base today. The plans call for a 1/8" sub-base and 1/2" base, so I settled for two bits of 10mm hot rolled steel bar :big: :
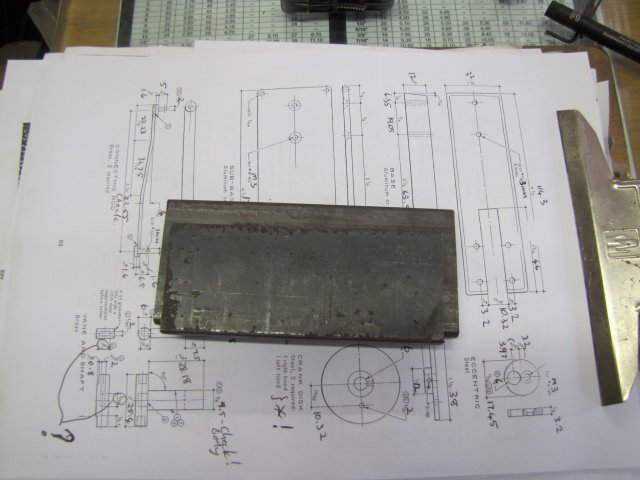
The thicknesses are not important - as long as they are thick enough together to accommodate the flywheel swing.
Both bits were sawed and then milled to size, and the flat faces roughly fly-cut to get rid of all the mill scale:
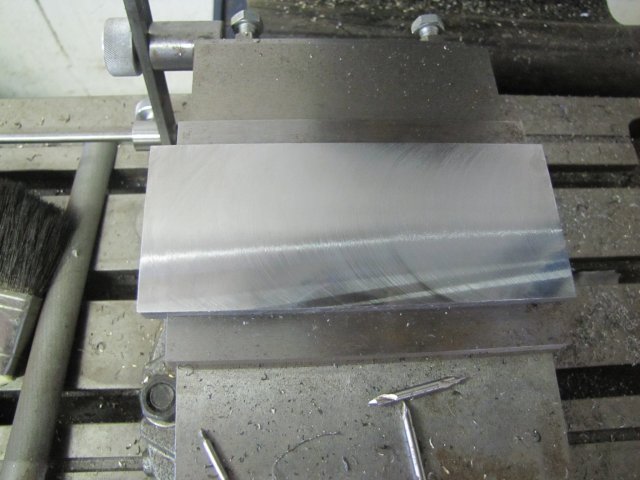
A bit of lay-out on the base:
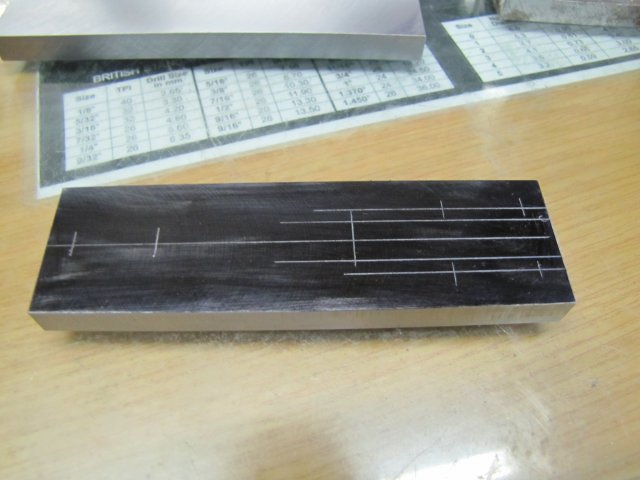
Then I clamped it to the sub-base and started drilling 3mm clearance holes for all the mounting bolts:
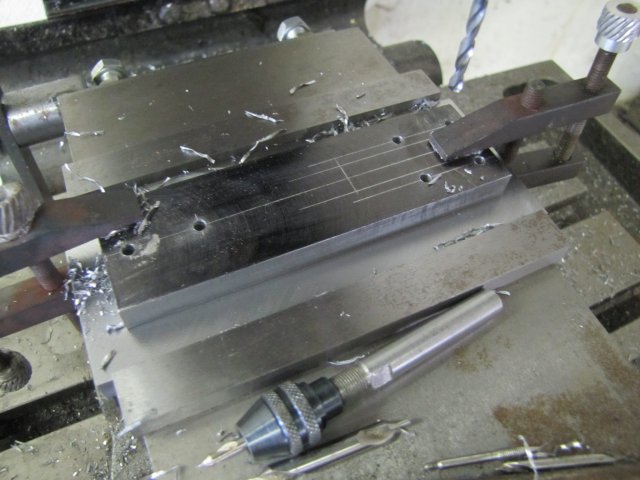
I wasn't feeling in the mood to mill out the entire flywheel cut-out, so I chain-drilled the end, pushed some pins through the holes to keep things matched up and then used the band saw to cut down the sides leaving about 0.5mm of metal to remove with the mill:
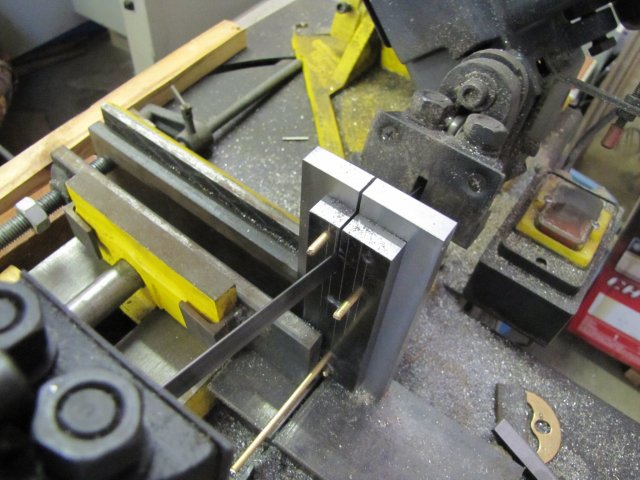
I just kept a careful eye on the cut to make sure it didn't stray too far. Because of the angle of the saw head, I had to stop early, and finish off the last short sections of the cuts with the saw in vertical mode.
Now, who says a shifting spanner has no place in the shop ;D - I used a small one to break out the unwanted sections from the cuts:
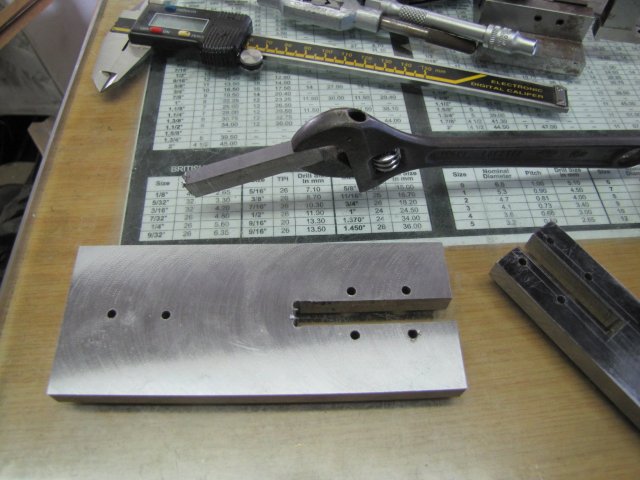
The cut-outs were cleaned up with a 4mm end mill; I just milled to split the mark-out line on the base:
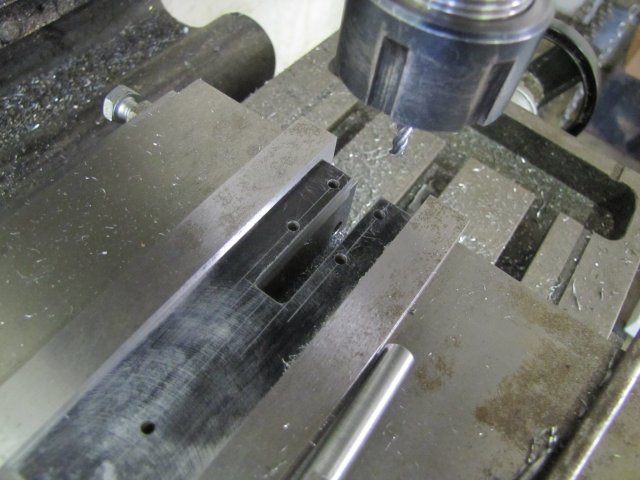
My 4mm end mills are too short to do both the base and sub-base at the same time, so I used pins to align the base with the sub-base again and used a sharp scribe to mark the sub-base off the milled-out section from the base. Then I just milled the sub-base to those lines as well.
Stopped here for today:
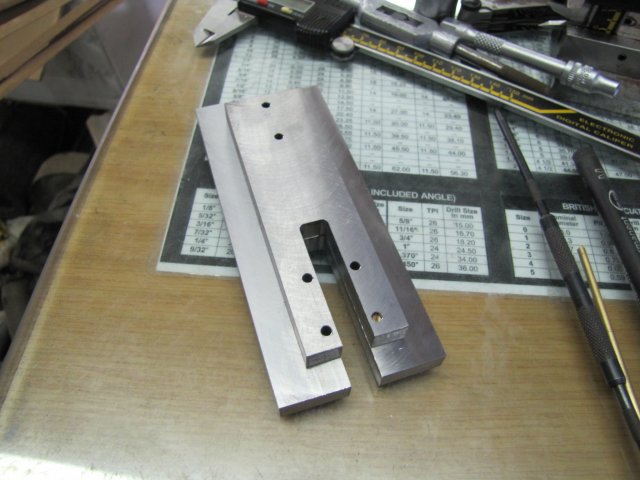
Regards, Arnold