- Joined
- Jan 19, 2010
- Messages
- 1,193
- Reaction score
- 41
Recently I was approached with a request for a customized motorcycle part.
The request involve engraving letters into a brake master cylinder cover. I decided to re-make the entire part out of scrap aluminum.
Originally I told him that since I dont have CNC I would not be able to make nice letters, more like the greek alphabet. He was OK with this, but I was not.
My original plan was to use the rotary table to get the rounded parts of the "R" and "C", and then angle the vice for the angles on the "R" and "M"
This would make a lengthly setup process, and the results might be less than great.
Since I had this first Idea I purchased a DRO, one that has the rounding and inclined milling features, and I used these features to get the "Angles" and "Rounds" of the letters.
Using some creativity, and drawing everything up in CAD to find tool position I came up with a decent result that I am sure he will be happy with.
I painted the milled out surface after sandblasting out the tool marks. I had tape on the raised parts. In the picture there is light scratches on the letters. This was from removing the paint, they will be sanded out once the paint cures fully.
This goes to show that with some creativity and perhaps some mathematical formula, or a DRO with functions, that milling simple raised letters IS possible with manual machinery.
Kel
The request involve engraving letters into a brake master cylinder cover. I decided to re-make the entire part out of scrap aluminum.
Originally I told him that since I dont have CNC I would not be able to make nice letters, more like the greek alphabet. He was OK with this, but I was not.
My original plan was to use the rotary table to get the rounded parts of the "R" and "C", and then angle the vice for the angles on the "R" and "M"
This would make a lengthly setup process, and the results might be less than great.
Since I had this first Idea I purchased a DRO, one that has the rounding and inclined milling features, and I used these features to get the "Angles" and "Rounds" of the letters.
Using some creativity, and drawing everything up in CAD to find tool position I came up with a decent result that I am sure he will be happy with.
I painted the milled out surface after sandblasting out the tool marks. I had tape on the raised parts. In the picture there is light scratches on the letters. This was from removing the paint, they will be sanded out once the paint cures fully.
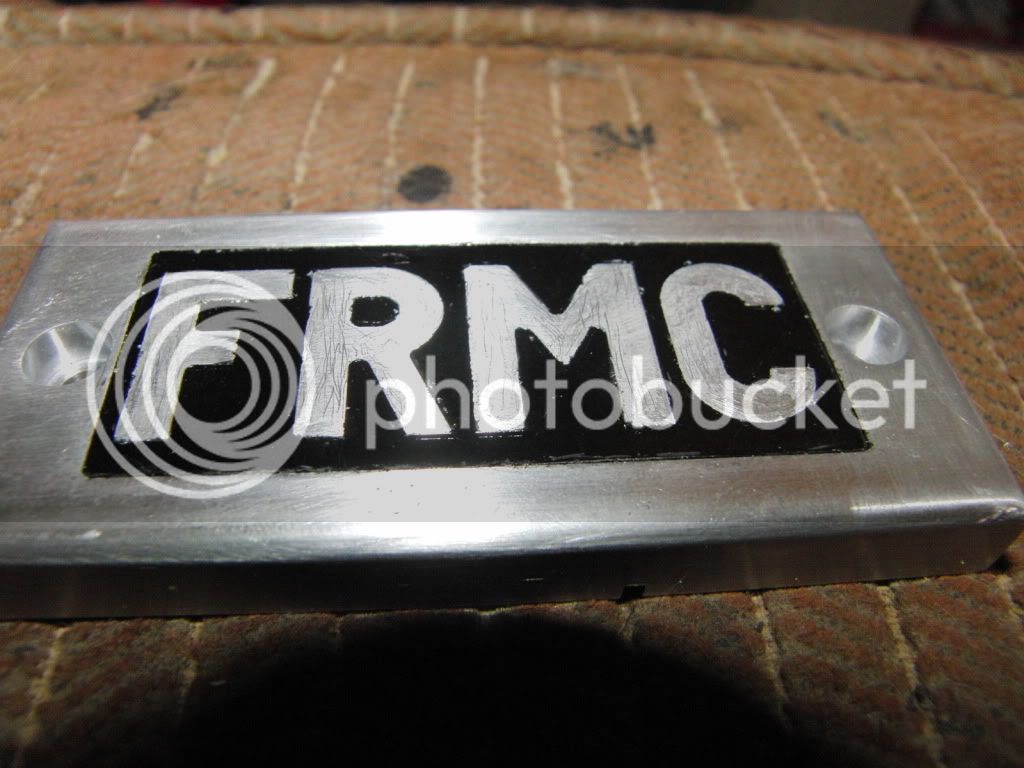
This goes to show that with some creativity and perhaps some mathematical formula, or a DRO with functions, that milling simple raised letters IS possible with manual machinery.
Kel