-And here is the face cam finished, roosting safely where it is intended to go. Will it work?--Well, probably. I won't know until everything else is finished and I try to start the engine. These little hit and miss engines are pretty forgiving.---Brian
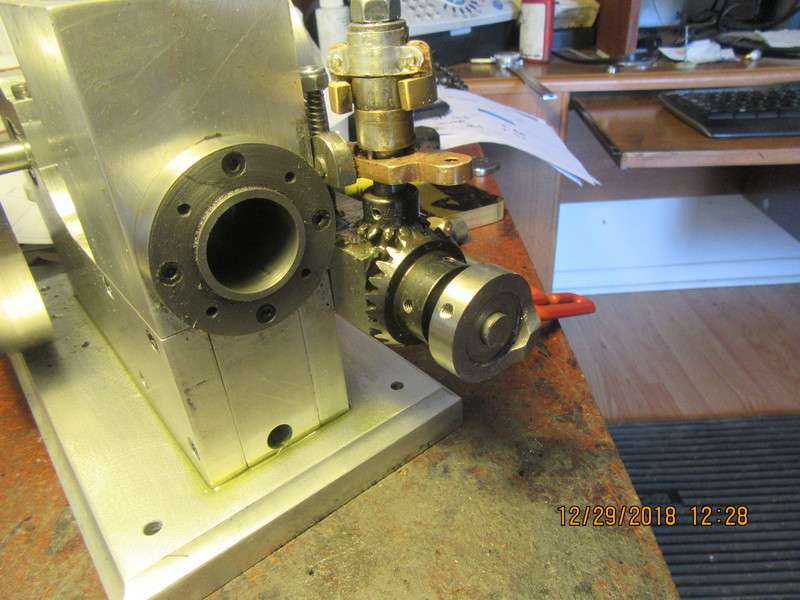