If you were wondering how I was going to cut that 22.5 degree angle, with a relief----Heck, even in case you weren't wondering--here's how I do it. The pedestal in front of my grinder is fixed at a permanent 7 degree angle. It has two 3/4" wide slots in it that are parallel to the sides of the grinding wheel. I take a piece of 3/4" square aluminum stock, set it up in my mill with my swivell based vice, and mill a slot (2 slots actually) through it 3/16" wide at 22.5 degrees. This lets me nest the HSS in the 3/16" slot in the 3/4" square bar, which in turn sets in the slots in the pedestal, and presents the HSS at a perfect angle to grind 22.5 degrees with a 7 degree relief angle. When one side is done, I flip the guide around, set it in the other slot, and grind the other side of the HSS.
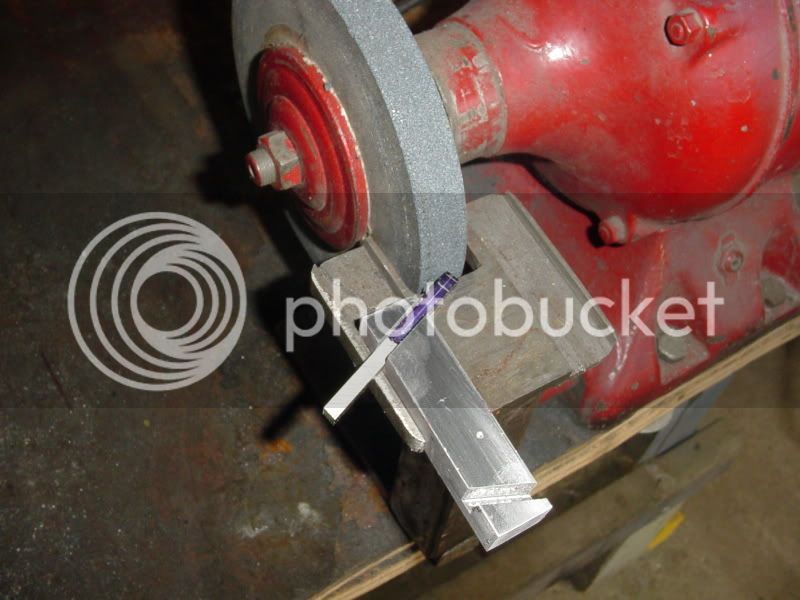
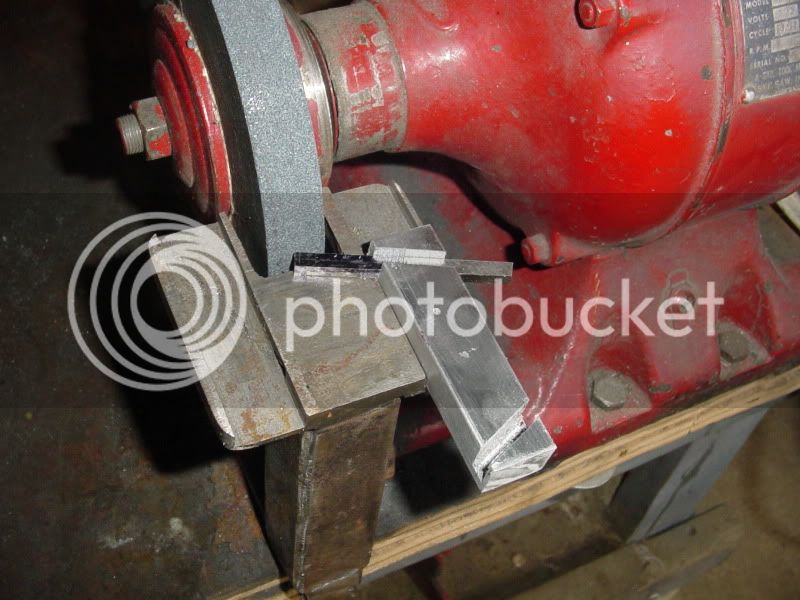