With a little judicious grinding, I can get most of the profile required in two steps, as per the drawing---
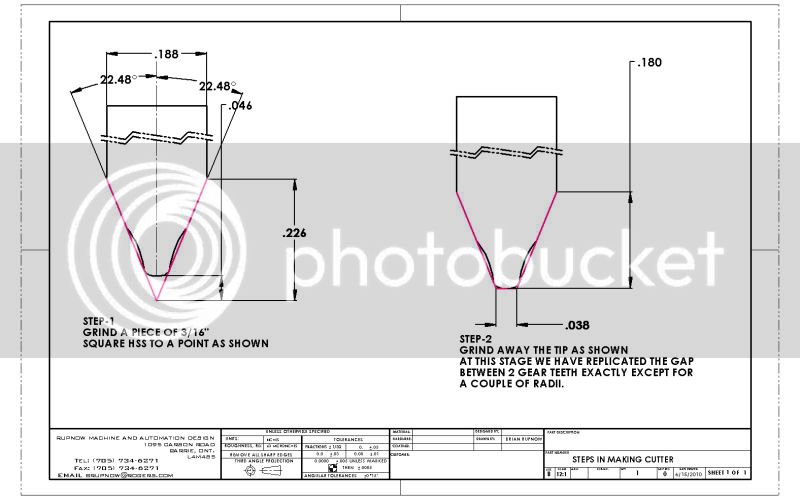
Brian Rupnow said:So, Captain Gerry---Am I close so far to what you did?---And if I am, how much relief angle did you add in?-----and did you add relief angles to the large radii???----Brian
Dan Rowe said:Kvom, The plates I have for my RT do not have every division between 2 and 100. It has most of them but not all so if an odd prime number gear was needed the only option would be by degrees.
Enter your email address to join: