Al. Conn. Rods
Heres the blank, not quality aluminium, but the plate should do for the job.
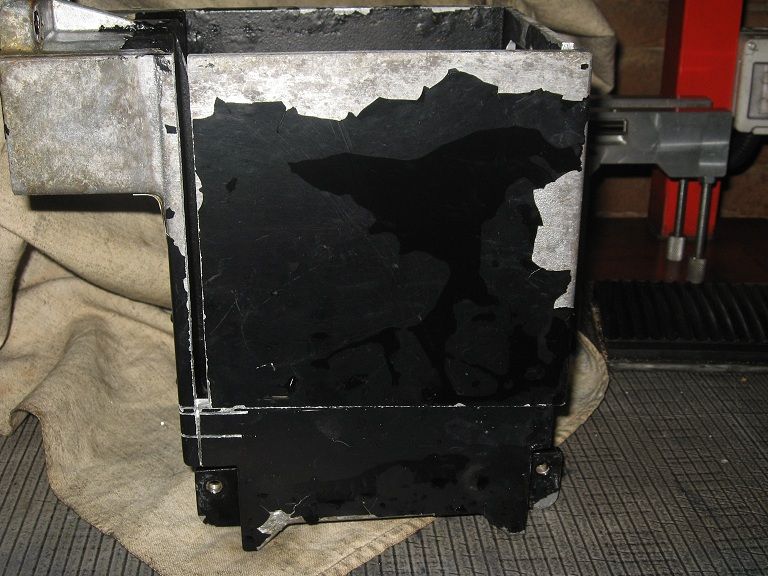
Chain drilled
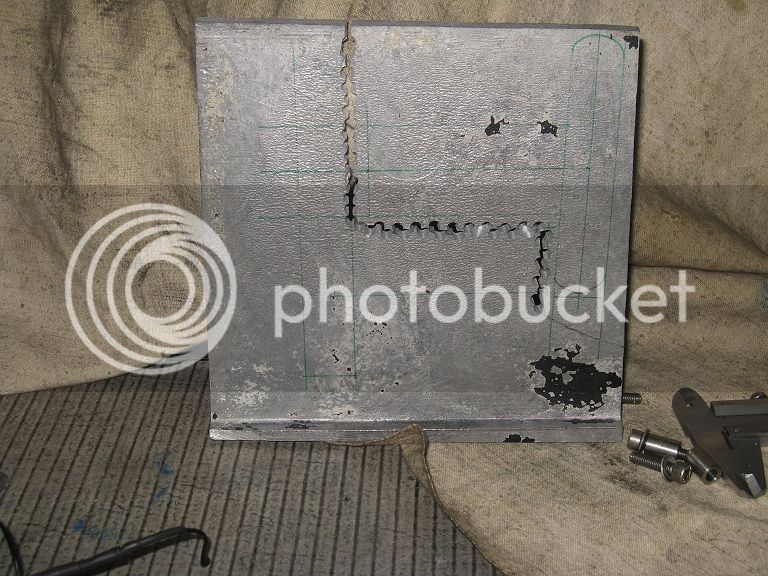
Using the vice as it were an angle plate
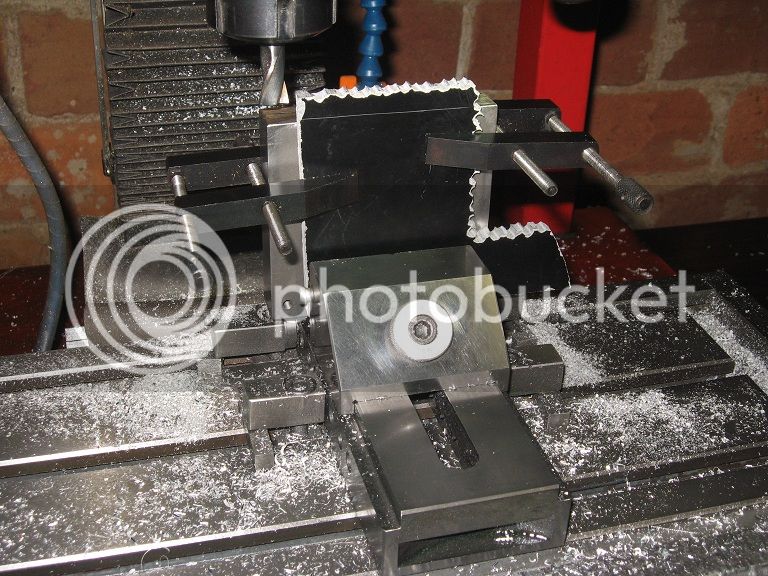
Overtightening a toolmakers clamp: cracks among the marker lines.
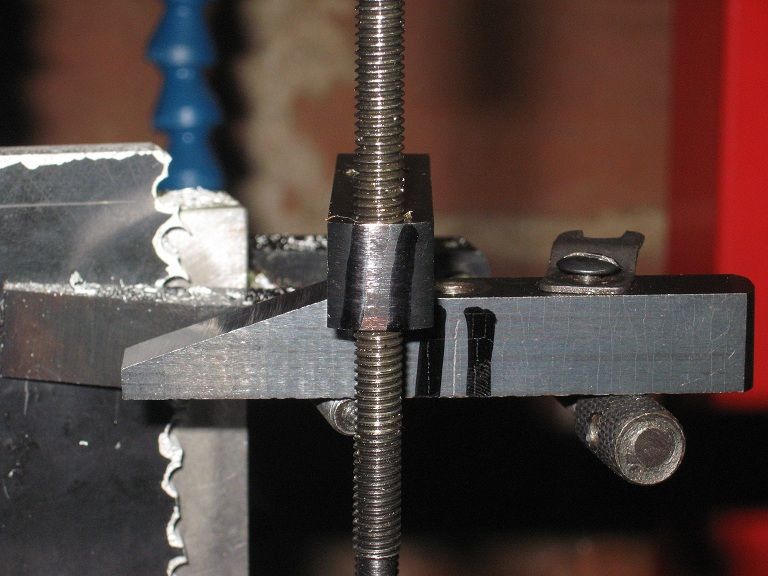
Bearing areas completed.
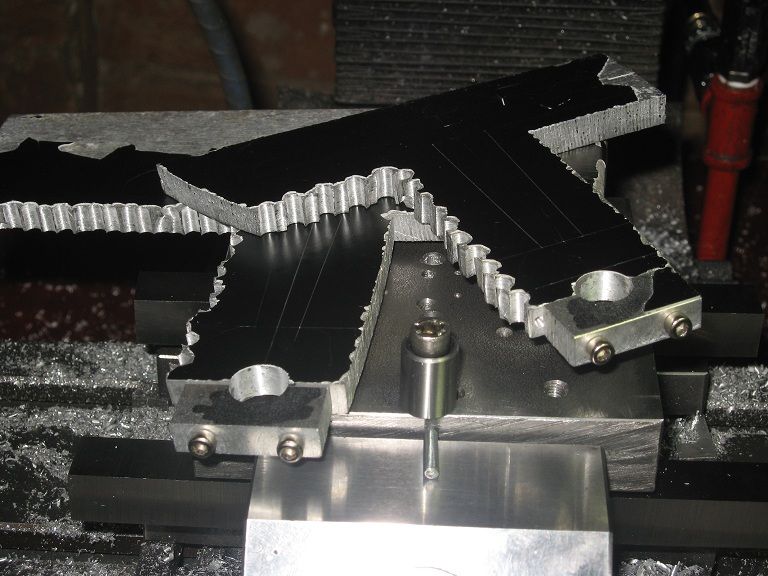
On the holding plate I had made before. A strip of paper (half circle) between the bearing feet
and the rod secured a firm hold without affecting the distance among the centers.
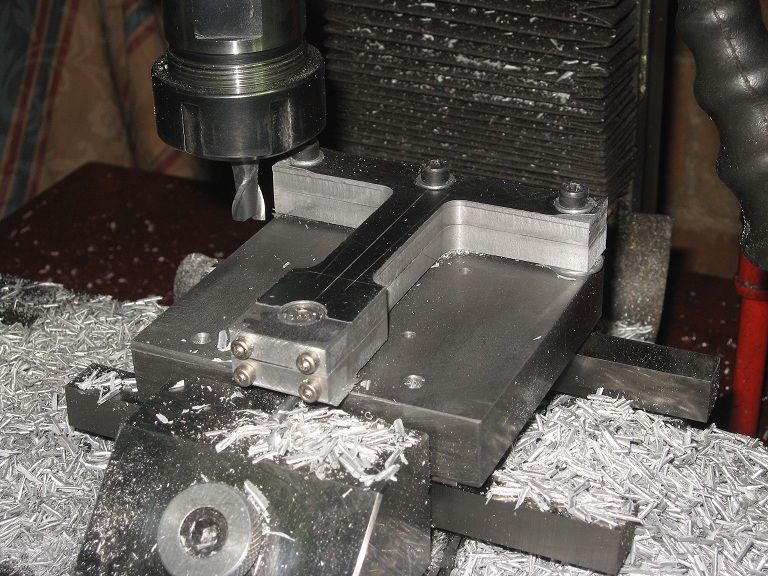
Constructed crankshaft (continued)
Chamfering the holes, using a wood board as support: the tool would surely grab the hard material (it did),
sharp edges, : rather keep fingers far from that area.
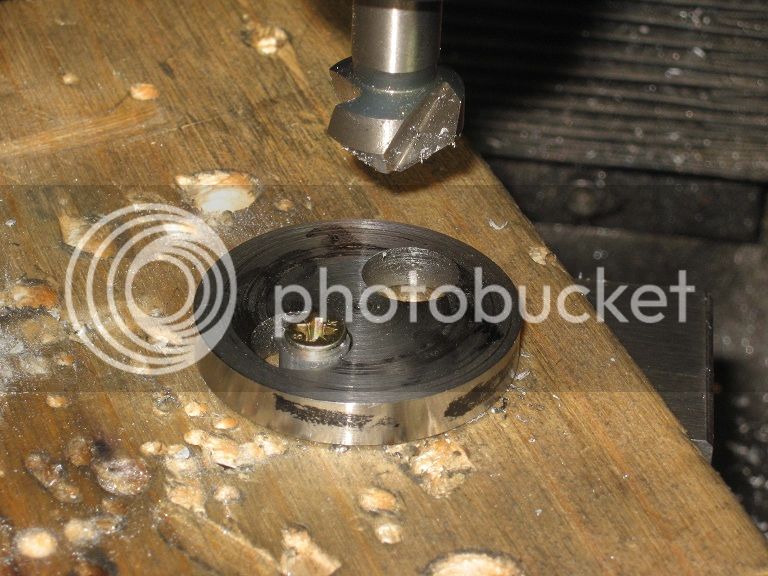
A quick test into hand reaming the 11.5mm holes to 12H7 convinced me to chuck an old 12.06 machine reamer
from the purchased by weight bag.
Back on the holding plate, I screwed in a rod end I had turned to 11.5mm (added a clamp) and reamed one
hole in each of the four throws. Then, replaced the rod end with a 12mm one, and reamed the remaining holes.
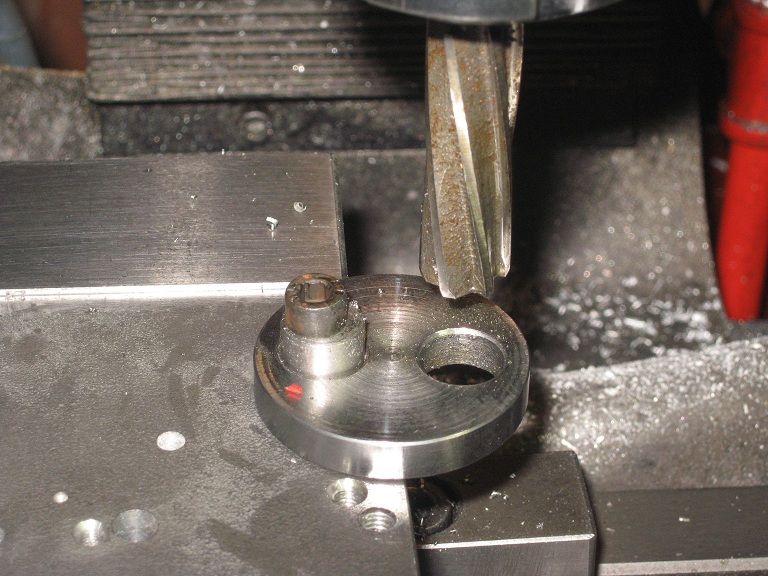
12.06 holes and 11.98 silver steel shafts in need for a press fit joint: solution came throgh knurlink.
Had ideas that straight knurlling would have been the way to go, but the wheels could not stand the work
on silver steel long enough. Had to revert to diamond knurling to complete the job.
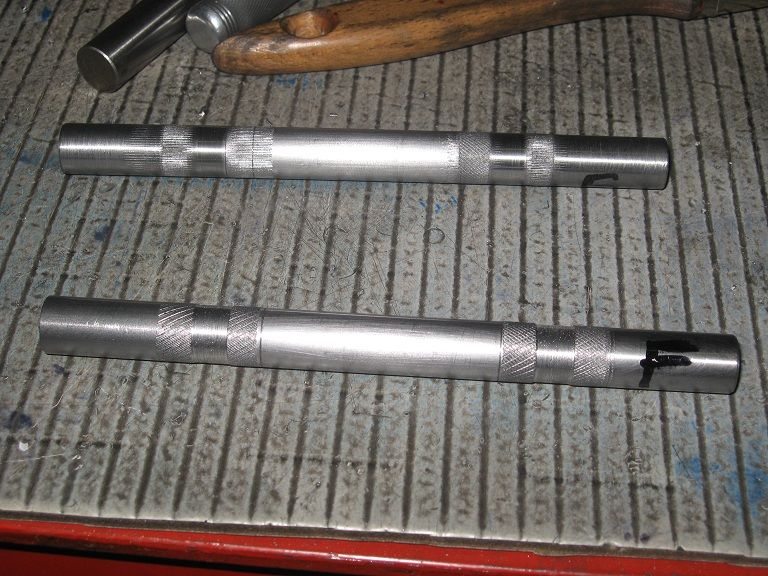
A bit of loctite (permanent thread locker - what I had) may do. Or may not, who knows.
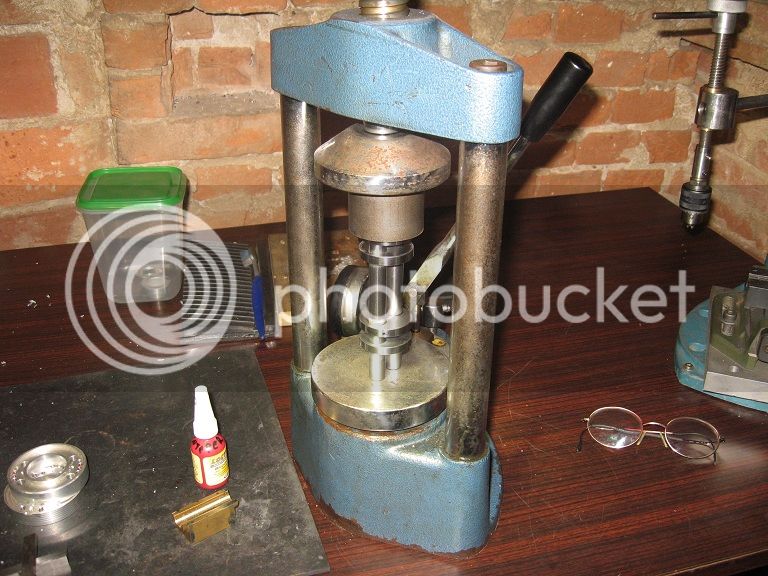
Testing for alignment: no point! I had reduced the ends in one of the two shafts (the ones I will cut!) to
whatever diameter they came, after having used them as test workpieces to try the knurls. Now it rocks,
but thats obvious.
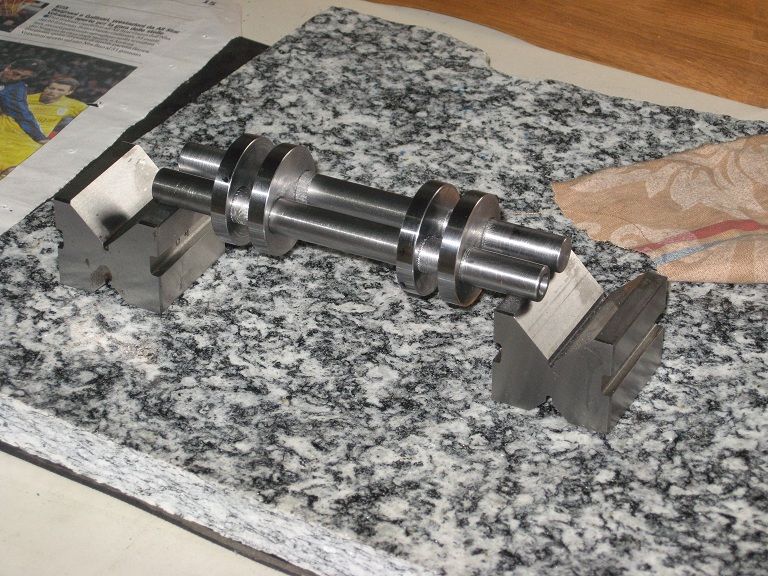
A visual test spinning on the lathe showed no visible wobbles, and thats the point I put it aside waiting for curing.
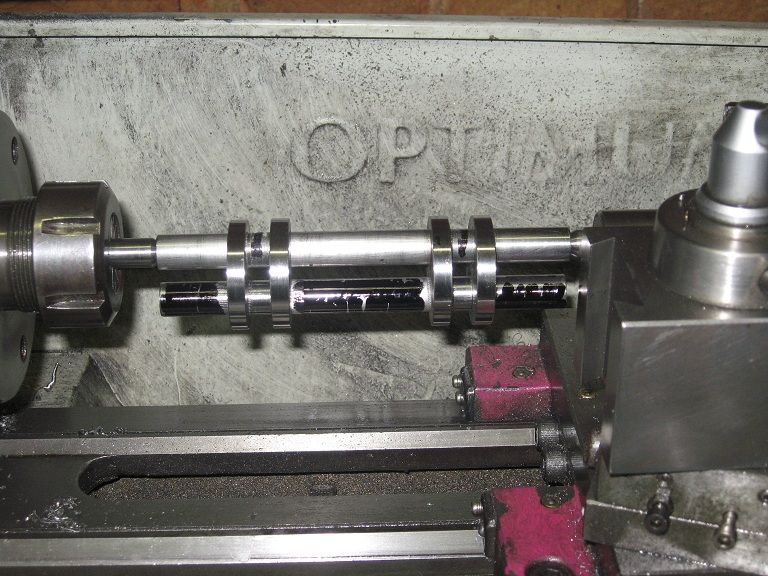
Al. Conn. Rods(continued)
On the rotary table, to round the ends of the bearing areas.
The single-screw hold worked better than expected: I had only one slip, when milling to full depth the arcs
around the bearing area.
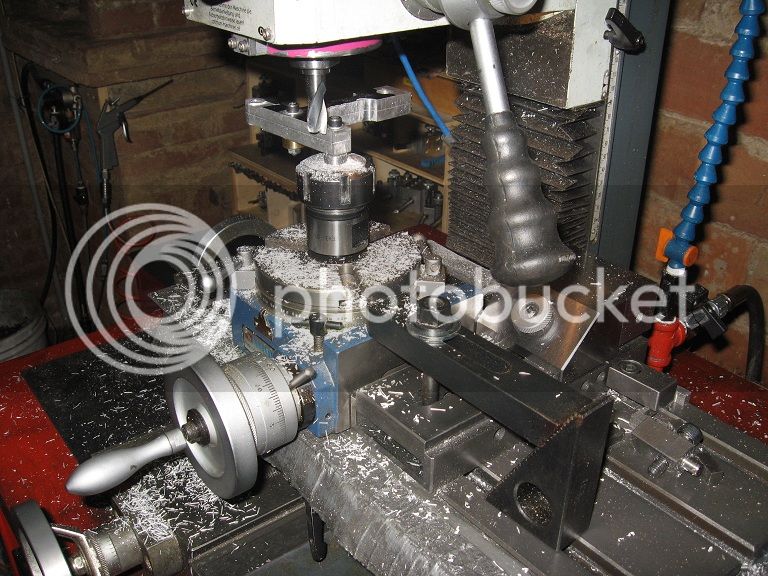
Rounding completed on both sides, end of workshop time. Will get back to them for finishing.
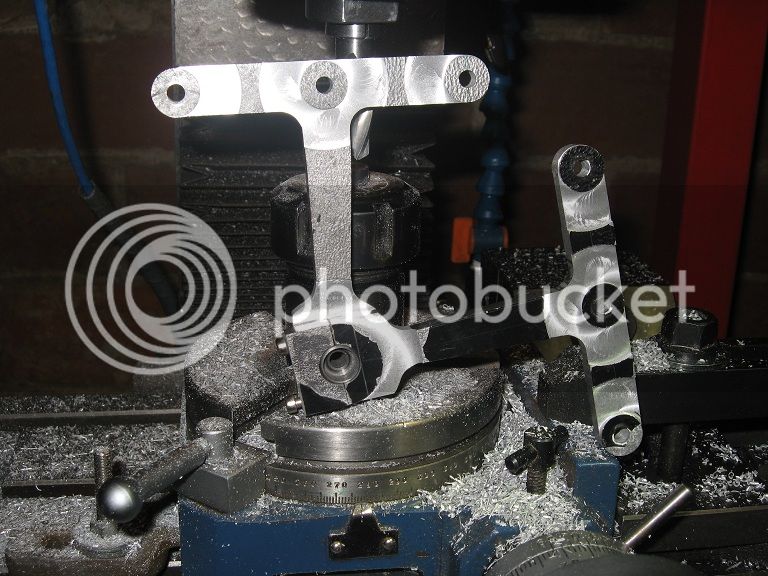
Marcello