Connecting Rods Bushings
Had a small chunk of bronze rod with dozens of blow holes in it: the right material to make short bushings (providing Youre positive into discarding two third of the semi-finished parts)
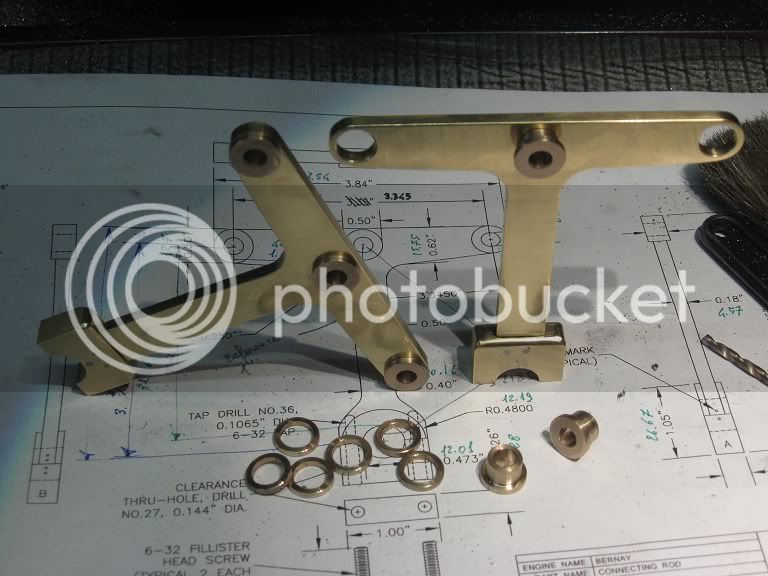
One of the bushings had a too light interference with the hole in the rod: at some point during the reaming it started turning.
When the long line of self expressed comments finally ended, I went for a gentle squeezing of the part into the bench vise:
the deformation I got (on second try) was enough to set it firmly. And that should do.
Then, the sixth of the bushing rings cracked partially while being driven in place: it took quite a while of fiddling with needle files and
sand paper to realize I had that already turned and bored to size rod still set in the lathe chuck, even the hacksaw blade parting tool still
in the post. One minute? Probably less.
First assembly
Now that thing starts looking like an engine!
The two (long, You see) 6mm printer shafts were rather stiff into their bushings: after a while, I removed them one at a time and
hand reamed the bushings in line. Another bit of oil ..hey! It turns smoothly!
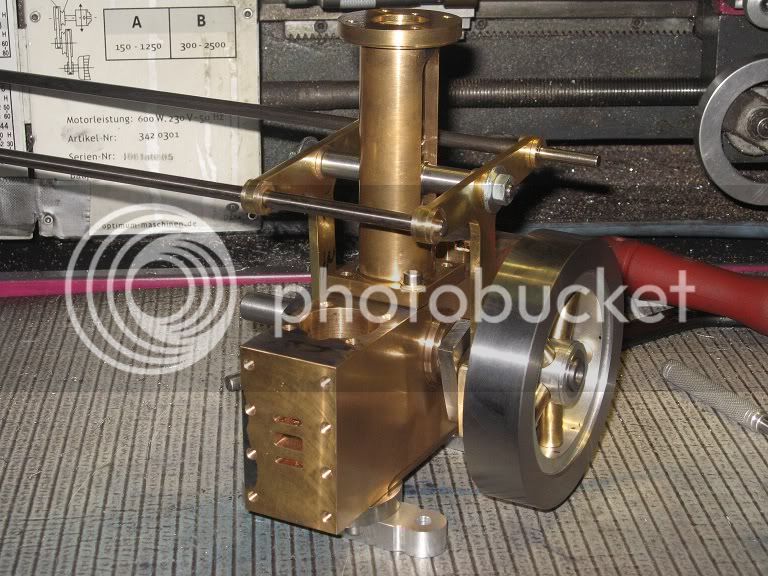
Having (in hindsight, regretfully) spent most of the remaining shop time (and there was still plenty) playing with the moving parts,
I found no points into wasting my dinner time into the same activity
Connecting Rod Shafts (..of course)
They were supposed to be made into two pieces only (to say nothing about the diameter reduction from ½ to 10mm) but I had
a 6mm threaded bar just a little bit too long to fit into the so labeled box. Now, I can close the lid.
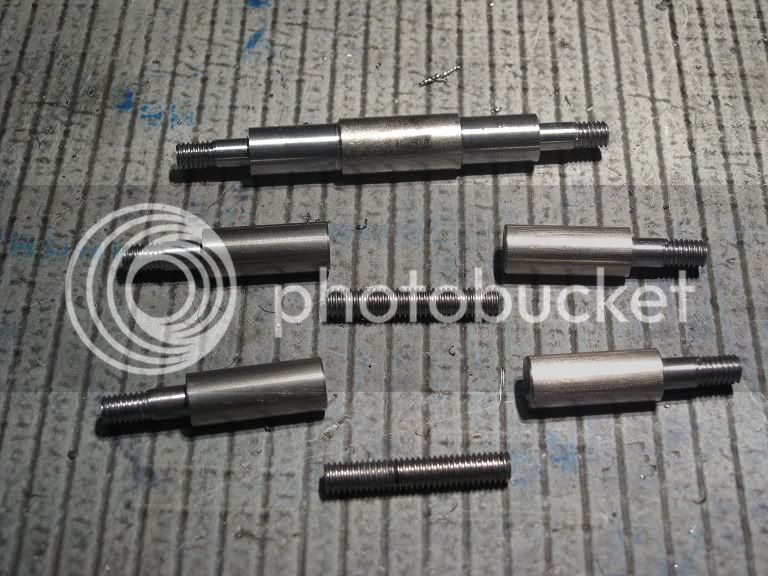
I left them slightly over length, just in case I got a bit creative with the dimensions of the parts they will be fitting to.
As for the missing runout groove clearly not visible on those threads, I decided to postpone that work till I will grind a thin round
nosed grooving tool purposely made for the job, the parting tool being too wide and the hacksaw blade too thin.
As it usually happens on the (frequent) occasions I wander from the drawings, the single-piece crosshead pin and bolt cannot
be set in place unless BOTH the connecting rods were disconnected from the crankshaft.
Not sure it can be seen as an improvement.
Marcello