- Joined
- Jun 4, 2008
- Messages
- 3,285
- Reaction score
- 630
Today I started on the steam control block, which is the last component needing to be machined and the last assembly that can be completed until I am able to silver solder pieces together. Here's the block and spool, along with the elements of the eccentric linkage completed since the last photo:
I made several errors in machining the block, none of which I think (hope) will require remaking it.
The first issue was in drilling the mounting holes for the flanges. I was using the vise stop to center all of the holes on the edges, and apparently a piece of swarf or something got between the block and the vise jaw, causing these holes to be slightly off center. To work around this, I will need to offset the mounting holes in the two flanges, but this seems reasonably easy to do.
The second issue was in the size of the 4 steam holes. I just scaled these up from the 4mm plan spec, which means I drilled them 15/64. I should have realized that I would be soldering 1/4" tube into these holes. Since I machined the block out of 2" round stock, the block is slightly smaller than the plan scale would require (1.4" each side vs. 1.47"). This means that the holes are closer to the edge, and enlarging them would make them even closer. However, it appears that I can enlarge the holes to 1/4" while keeping enough material between the hole and the edge.
Finally, I made the center hole overlarge. I entended to drill it to 1/2" and then bore to .59". To save time I drilled the hole using a 1/2" endmill. At least the shank was 1/2" but the flutes made it a 5/8" endmill. So after boring, the hole ended up with a diameter of .645". This can seemingly be handled by making the spool larger to fit, and that's what I did. I also made the spool shaft slightly oversize at 1/4" as I need to find an o-ring with a matching ID. Once I get the O-ring the front and back caps can be machined.
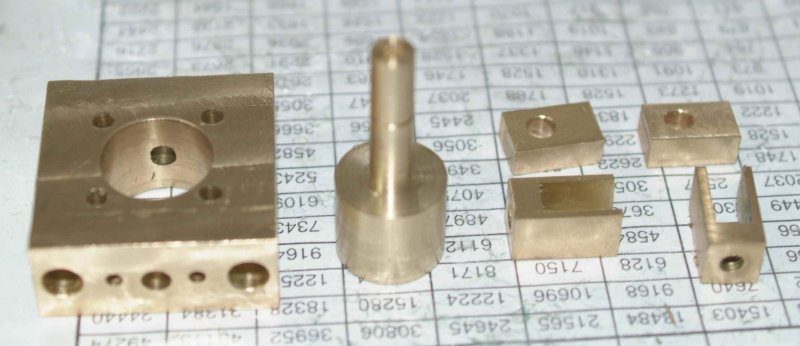
I made several errors in machining the block, none of which I think (hope) will require remaking it.
The first issue was in drilling the mounting holes for the flanges. I was using the vise stop to center all of the holes on the edges, and apparently a piece of swarf or something got between the block and the vise jaw, causing these holes to be slightly off center. To work around this, I will need to offset the mounting holes in the two flanges, but this seems reasonably easy to do.
The second issue was in the size of the 4 steam holes. I just scaled these up from the 4mm plan spec, which means I drilled them 15/64. I should have realized that I would be soldering 1/4" tube into these holes. Since I machined the block out of 2" round stock, the block is slightly smaller than the plan scale would require (1.4" each side vs. 1.47"). This means that the holes are closer to the edge, and enlarging them would make them even closer. However, it appears that I can enlarge the holes to 1/4" while keeping enough material between the hole and the edge.
Finally, I made the center hole overlarge. I entended to drill it to 1/2" and then bore to .59". To save time I drilled the hole using a 1/2" endmill. At least the shank was 1/2" but the flutes made it a 5/8" endmill. So after boring, the hole ended up with a diameter of .645". This can seemingly be handled by making the spool larger to fit, and that's what I did. I also made the spool shaft slightly oversize at 1/4" as I need to find an o-ring with a matching ID. Once I get the O-ring the front and back caps can be machined.