Sometime to day I hope to visit one of my suppliers and pick up some suitable head gasket material and some high temp sealing compound for the two bolts that have their heads exposed in the combustion chamber. I don't want to hone/lap the cylinder until after I have permanently locked the cast iron cylinder and the valve body (which I have been mistakenly been referring too as the "combustion chamber") together. In the meantime, I have just rattled off a quick detail of the valve. I see some people make valves out of stainless steel and other exotic materials, however I have always used just plain old garden variety cold rolled steel and never has a valve fail.
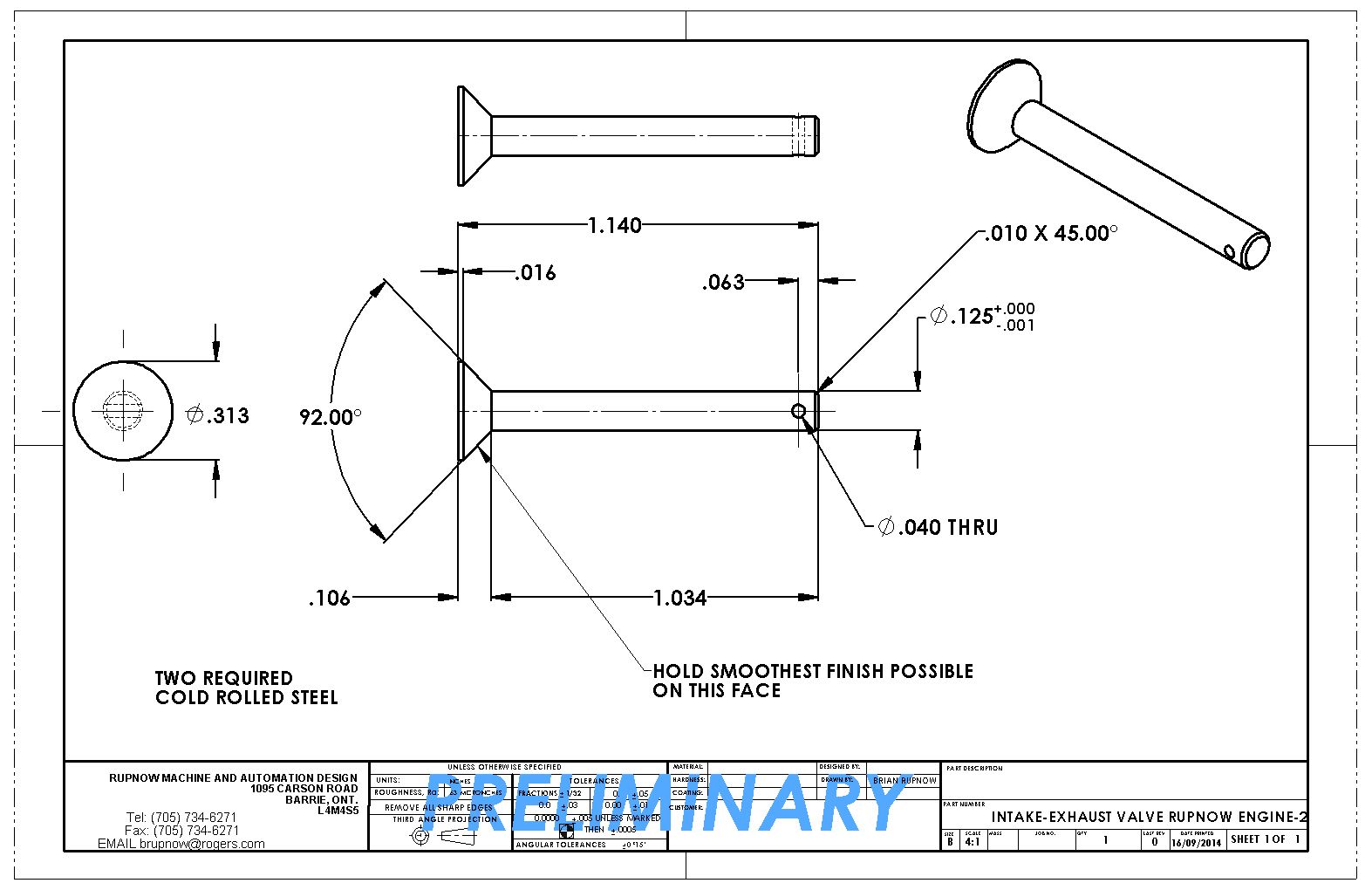