This afternoon seen the lubrication piping finished up, and the tie from the carburetor body over to the oil filler pipe to steady everything up finished and installed. Nothing cosmetic really done yet, everything is still a 'work in progress'.
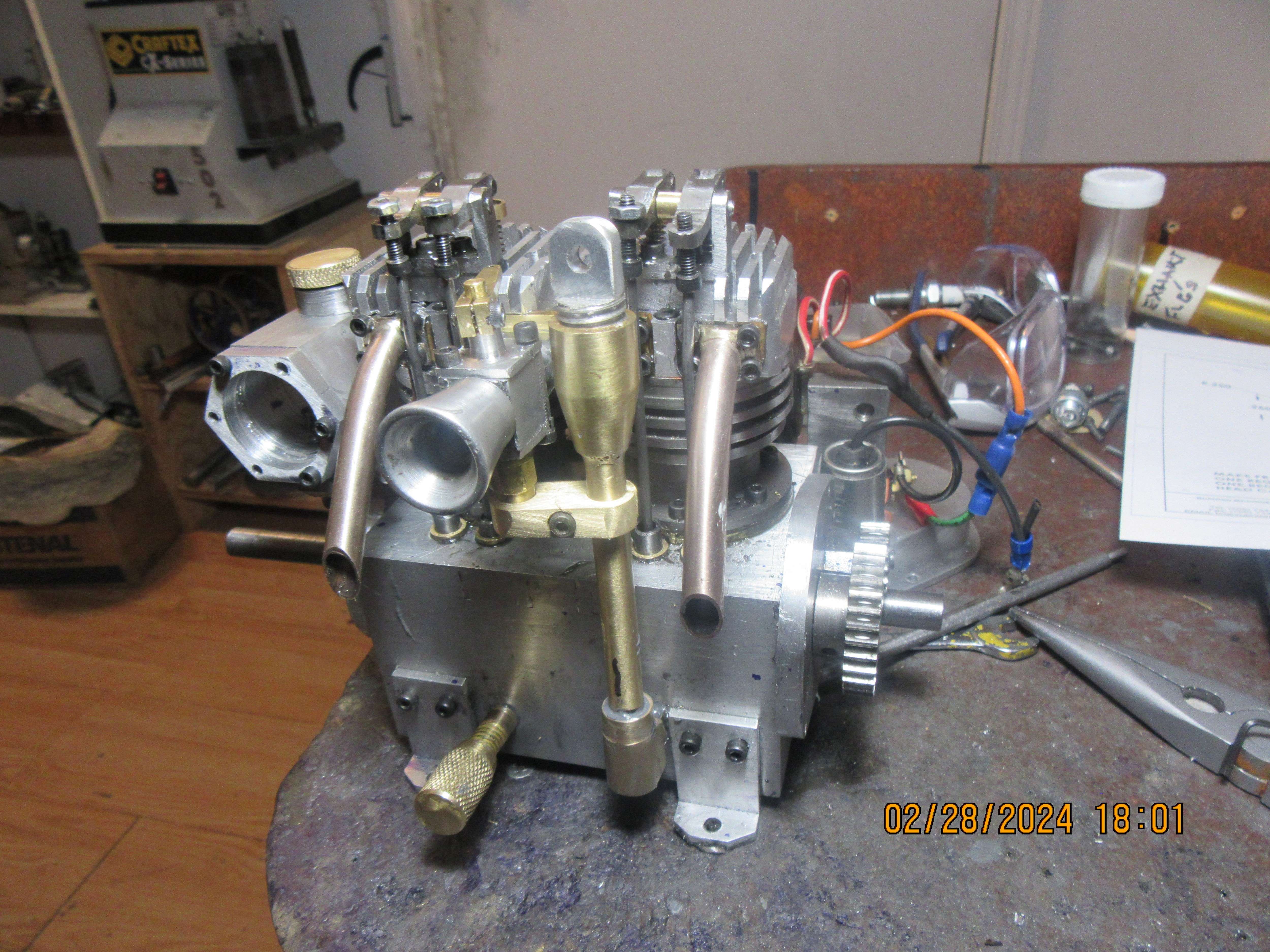
Looking good Brian! I'm looking forward to seeing this engine running. Keep up the great work.This morning I just didn't feel like tacking the valve timing.--However--The electric starting table didn't have any holes tapped in the top plate to suit this particular engine, so I got everything lined up properly and drilled/tapped holes to let me bolt this engine down. The starter turns the engine over very well, and as soon as I get my o-ring seals for the ends of the gas tank it will be installed and plumbed and the valve timing will be set. The only thing on this engine that gives me any concern are the cams. I truly do wish that someone out there in the wide world made a business of cnc machining cams for model engines. Once a machining profile was established then you could machine forty or sixty cams at one run, thus keeping the price down to where hobby guys could afford to buy them.
![]()
Enter your email address to join: