I finally finished the large pulley.
To cut the keyway I ground down a tool blank as pictured below.
This worked pretty well, except every once in a while, the tool would dig in pretty bad. I would be forced knock the chip out with a punch, back up 20 thou and try again.
The other problem I had, is the keyway got slightly twisted. I didn't lock the spindle, and I wonder if that had anything to do with it. I had to clean up the twist in the keyway with a file.
After some light filing and sanding the pulley seems to fit well.
After I was sure the pulley would fit, I tapped the 6x1 grub screw hole, and cut the slot for the spindle lock.
To cut the keyway I ground down a tool blank as pictured below.
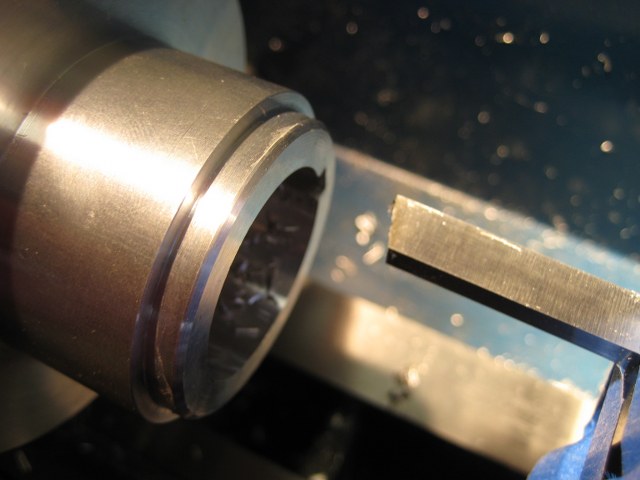
This worked pretty well, except every once in a while, the tool would dig in pretty bad. I would be forced knock the chip out with a punch, back up 20 thou and try again.
The other problem I had, is the keyway got slightly twisted. I didn't lock the spindle, and I wonder if that had anything to do with it. I had to clean up the twist in the keyway with a file.
After some light filing and sanding the pulley seems to fit well.
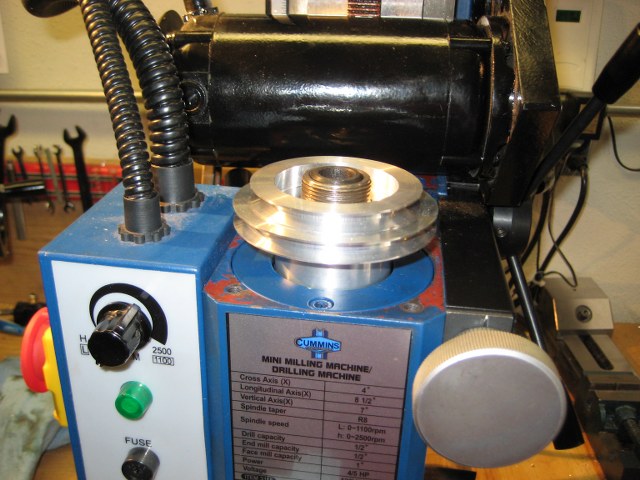
After I was sure the pulley would fit, I tapped the 6x1 grub screw hole, and cut the slot for the spindle lock.
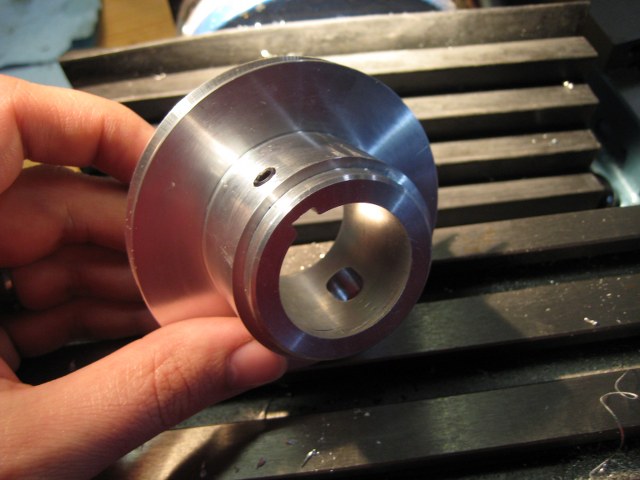