After much procrastination I have started making the cylinders. It was hard to find the courage to make the first cut. I spent about an hour going over the measurements and checking and re checking the positions on the leadscrew wheel.
Finally decided I had all the numbers written down correctly and got on with it.
Had to be slow and steady using middle speed with the backgear on my Myford but all went well without mishap. The fins are 45 thou with 55 spaces.
So with the outside finished I started drilling the bore. All going fine until the drill (11/64 I think) bit for some reason and snapped !!! And there was me fretting over the fin cutting. The broken piece came out easily and I started to breathe again. Ready to have another go with a smaller size to try and ease things through found the cylinder had shifted in the chuck. Out with the clock and set up true after almost giving up. Had to use a boring tool earlier than I planned but now have a cylinder bore 2 thou undersize ready to lap. I think I was a bit lucky.
Number two I have drilled through with ¼ before finishing the outside. No problem with that. Now ready to bore out to ¾ inch.
When I bought the model engineer magazines with this article in them I was perhaps a little naïve in thinking all I had to do was follow the instructions. Not having built an engine before I realize now that it was not a good choice for a first project. I do however believe I can finish it and hopefully get it to run.
I am however suffering from a lack of confidence in posting this stuff. I am well aware that I cannot meet the high standards of some on here who can explain and photograph things very well indeed but I will do my best and hope someone finds it interesting.
ttfn Peter
Finally decided I had all the numbers written down correctly and got on with it.
Had to be slow and steady using middle speed with the backgear on my Myford but all went well without mishap. The fins are 45 thou with 55 spaces.
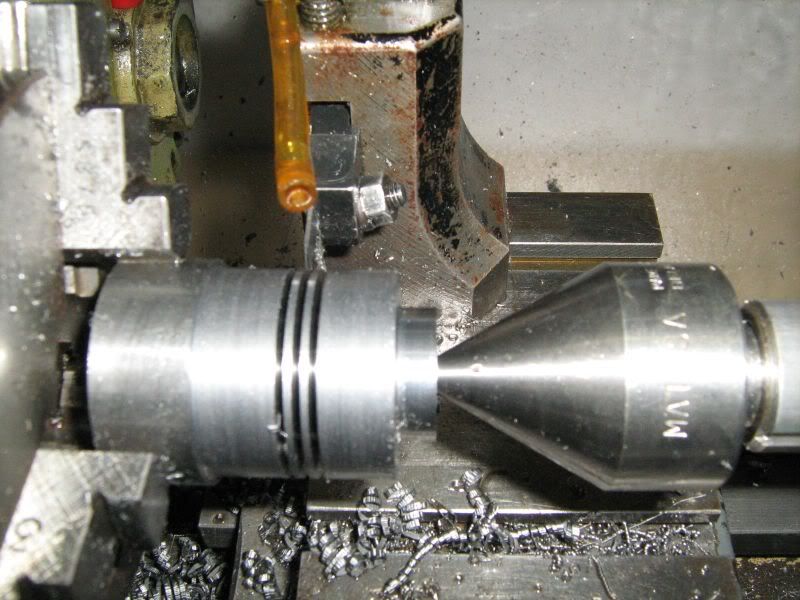
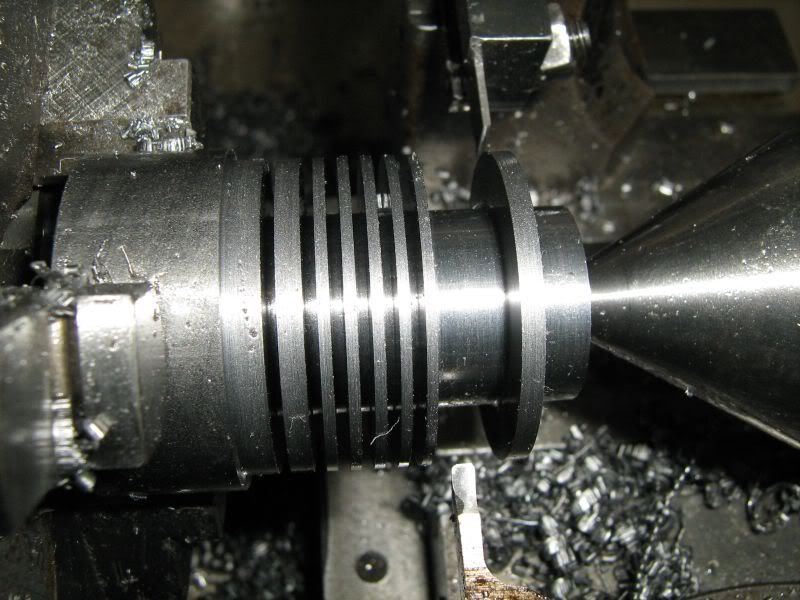
So with the outside finished I started drilling the bore. All going fine until the drill (11/64 I think) bit for some reason and snapped !!! And there was me fretting over the fin cutting. The broken piece came out easily and I started to breathe again. Ready to have another go with a smaller size to try and ease things through found the cylinder had shifted in the chuck. Out with the clock and set up true after almost giving up. Had to use a boring tool earlier than I planned but now have a cylinder bore 2 thou undersize ready to lap. I think I was a bit lucky.
Number two I have drilled through with ¼ before finishing the outside. No problem with that. Now ready to bore out to ¾ inch.
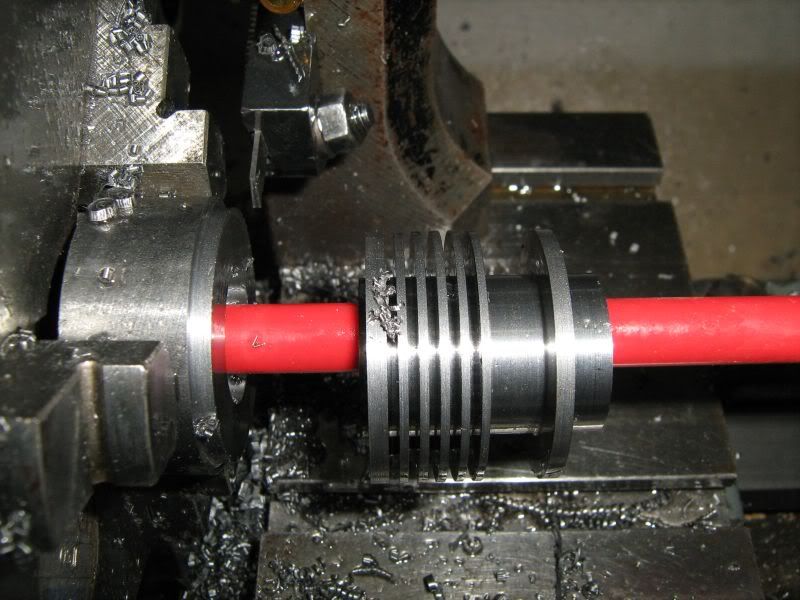
When I bought the model engineer magazines with this article in them I was perhaps a little naïve in thinking all I had to do was follow the instructions. Not having built an engine before I realize now that it was not a good choice for a first project. I do however believe I can finish it and hopefully get it to run.
I am however suffering from a lack of confidence in posting this stuff. I am well aware that I cannot meet the high standards of some on here who can explain and photograph things very well indeed but I will do my best and hope someone finds it interesting.
ttfn Peter