BobWarfield
Well-Known Member
- Joined
- Dec 27, 2007
- Messages
- 1,151
- Reaction score
- 1
One of the most useful and used tools in my shop is my set of transfer punches:
I know you experienced hands bought a set long ago, but for the newcomers, they are cheap and the best thing since sliced bread to transfer hole locations. This is not going to be awesomely accurate (lots of strategies for extreme precision), but for quick and dirty it can't be beat. You can also by transfer screws for blind holes. You screw them into the threaded hole and they have a point on the end like these transfer punches. Tap your piece and the point transfers the hole's location.
When done with my transfer punches, I had this:
Transfer punches are easy to find from the Asian tool outfits. My transfer screws were harder to track down and more expensive. I bought both an English and Metric thread set from somewhere on the web, but I don't recall where.
Best,
BW
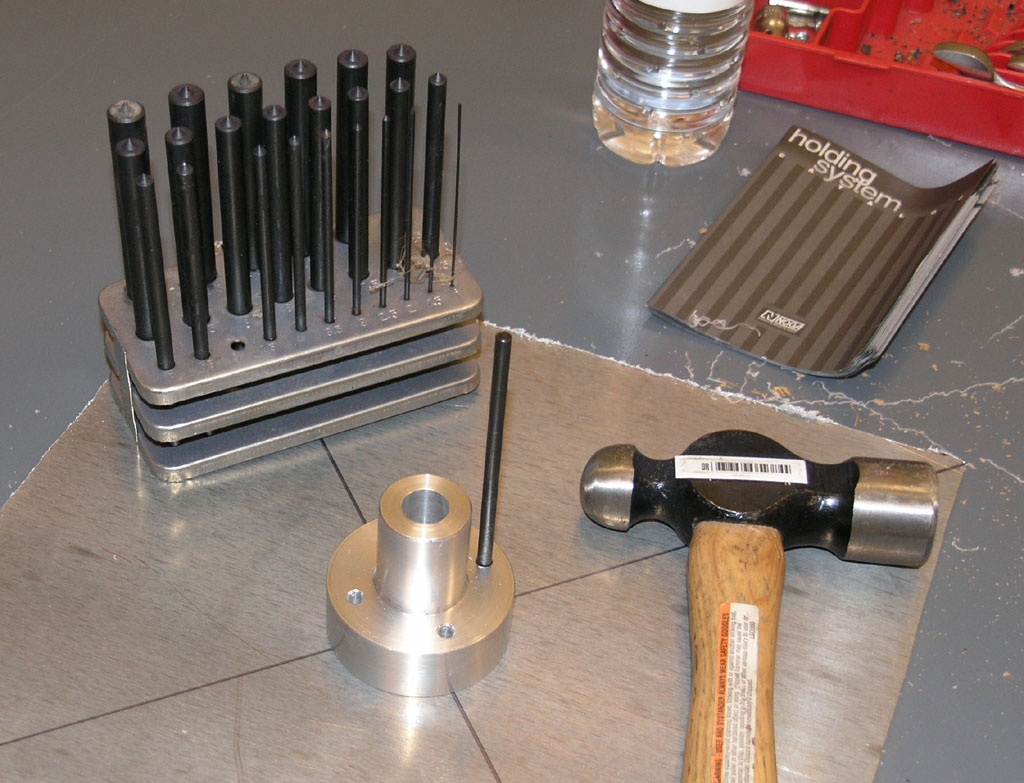
I know you experienced hands bought a set long ago, but for the newcomers, they are cheap and the best thing since sliced bread to transfer hole locations. This is not going to be awesomely accurate (lots of strategies for extreme precision), but for quick and dirty it can't be beat. You can also by transfer screws for blind holes. You screw them into the threaded hole and they have a point on the end like these transfer punches. Tap your piece and the point transfers the hole's location.
When done with my transfer punches, I had this:
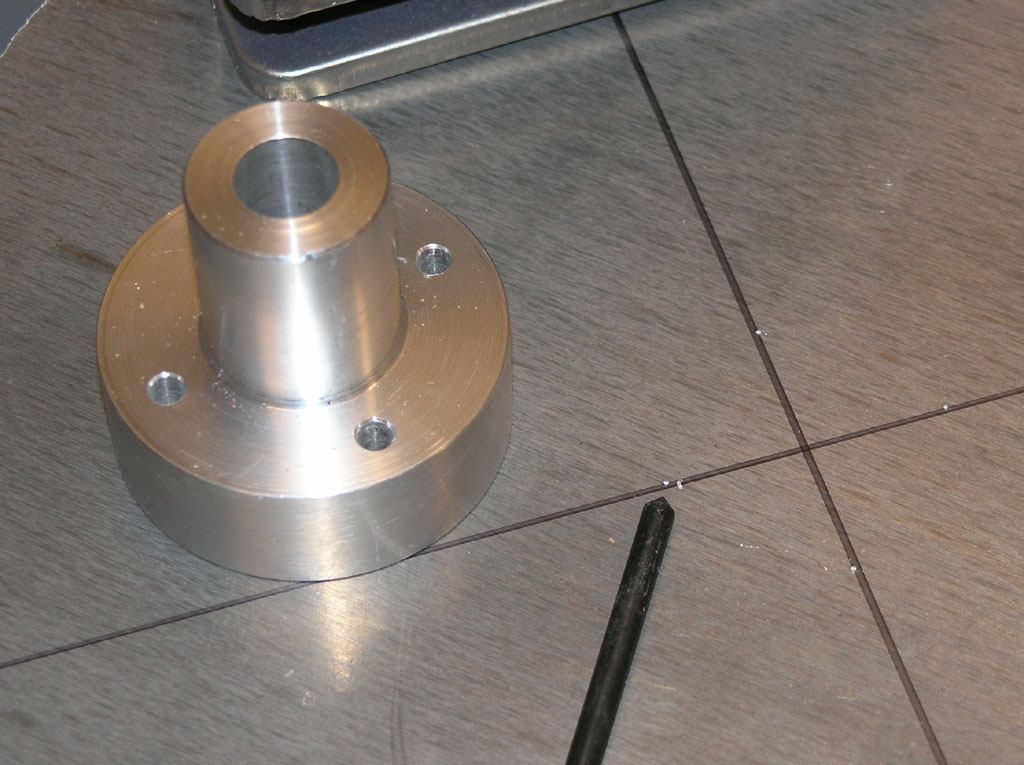
Transfer punches are easy to find from the Asian tool outfits. My transfer screws were harder to track down and more expensive. I bought both an English and Metric thread set from somewhere on the web, but I don't recall where.
Best,
BW