I have a CT129 Craftex mill from Busy Bee and the handwheel that I have to turn (in pink circle) to adjust the height of the head is high up at the rear of the mill. This happens to be right in the quadrant of movement that really bothers an old tendon injury in my right shoulder. Last night I was thinking of adding a power adjustment to the head. What immediately came to mind is the motor and gearset off an old barbeque rotisserie.---Trouble with that is that I doubt the motor is reverseable. Has anybody made a modification like that to their mill?----Brian
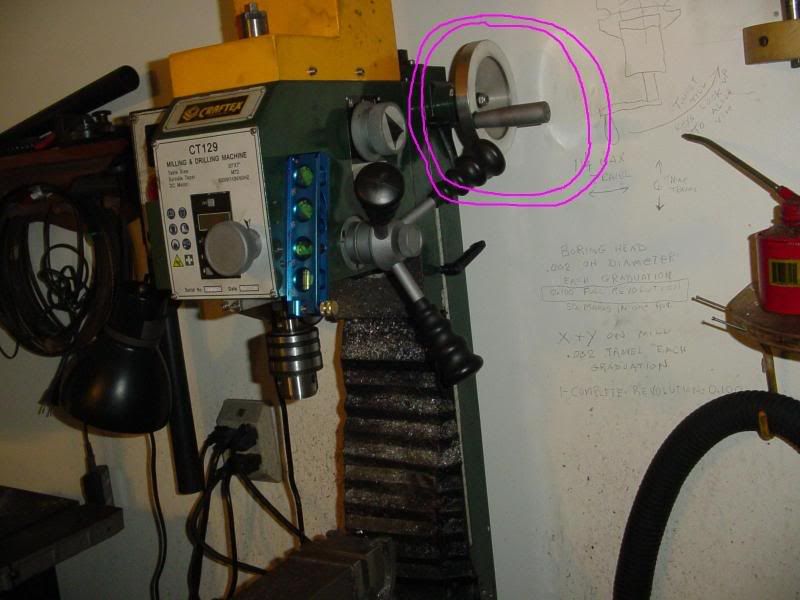