- Joined
- Dec 9, 2015
- Messages
- 327
- Reaction score
- 349
Thanks all for your input. More knowledge the better.
Finished the crankshaft and pressed in the small end bearing.
Made a base for the engine to sit on.
Drilled some holes into the head where I'll press fit some valve cages.
Ran the bottom end assembly in the lathe to run the rings in.
Getting there. Starting to get to the nitty gritty stuff
Finished the crankshaft and pressed in the small end bearing.
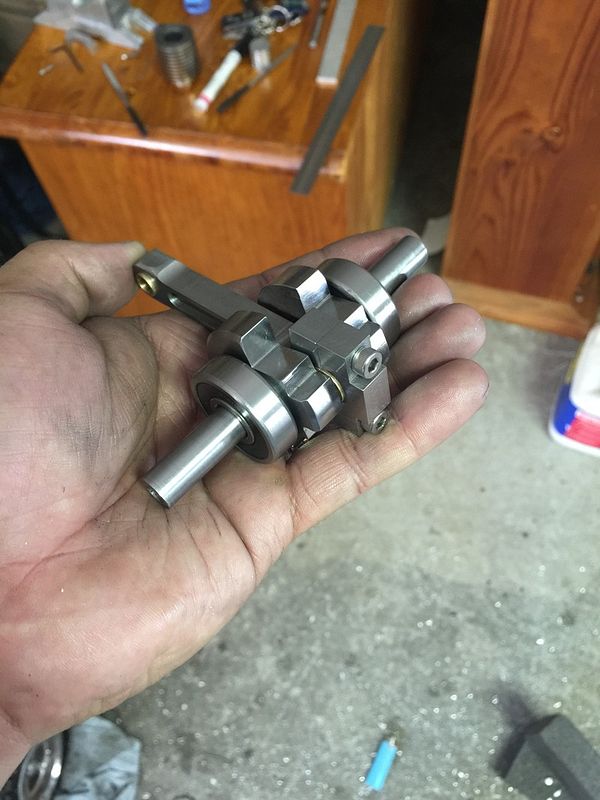
Made a base for the engine to sit on.

Drilled some holes into the head where I'll press fit some valve cages.
Ran the bottom end assembly in the lathe to run the rings in.
Getting there. Starting to get to the nitty gritty stuff