- Joined
- Dec 12, 2012
- Messages
- 2,220
- Reaction score
- 1,285
Niels kindly sent me one of his diamond tools for my new mini lathe
his only request was to use it and do a review,and also send a donation
to our local RSPCA.We are both dog lovers and all animal lovers
The tool he sent is sized for the 7 mini lathe but i decided to do minor mods
to enable it to be used on the sc4 lathe as well.The following photos show
my first tests on both lathes.The tool worked well but i feel can be improved further.Niels emphasised,high speed ,deep cuts and BLUE chips.However the
mini lathe i felt would let us down,power and rigidity wise and so it proved
The tool overhang can be reduced to prevent machine flex which i will look at
The 2 mm carbide is good for light work with cuts up to 30 thou on power feed
and is ideal for the small lathe.
The tool worked better in the larger lathe but depth of cut is restricted to about 80 thou (The width of the 2mm carbide ) and with a 60 thou cut and fast speed of about 800rpm i could get straw chips. With this lathe i did not any reason to
increase the workrate anymore for an 8" lathe and model engineering
I think that the depth of cut and speed can be increased and blue chips produced,BUT WOULD RECOMMEND increasing the carbide to 3mm sq
I will play about with this tool some more but my general impressions are good.It is ideal as is for lighter work in the 7" lathe and for heavier work
in the 8" lathe. Thank you Niels i will keep this thread open. Regards barry
his only request was to use it and do a review,and also send a donation
to our local RSPCA.We are both dog lovers and all animal lovers
The tool he sent is sized for the 7 mini lathe but i decided to do minor mods
to enable it to be used on the sc4 lathe as well.The following photos show
my first tests on both lathes.The tool worked well but i feel can be improved further.Niels emphasised,high speed ,deep cuts and BLUE chips.However the
mini lathe i felt would let us down,power and rigidity wise and so it proved
The tool overhang can be reduced to prevent machine flex which i will look at
The 2 mm carbide is good for light work with cuts up to 30 thou on power feed
and is ideal for the small lathe.
The tool worked better in the larger lathe but depth of cut is restricted to about 80 thou (The width of the 2mm carbide ) and with a 60 thou cut and fast speed of about 800rpm i could get straw chips. With this lathe i did not any reason to
increase the workrate anymore for an 8" lathe and model engineering
I think that the depth of cut and speed can be increased and blue chips produced,BUT WOULD RECOMMEND increasing the carbide to 3mm sq
I will play about with this tool some more but my general impressions are good.It is ideal as is for lighter work in the 7" lathe and for heavier work
in the 8" lathe. Thank you Niels i will keep this thread open. Regards barry
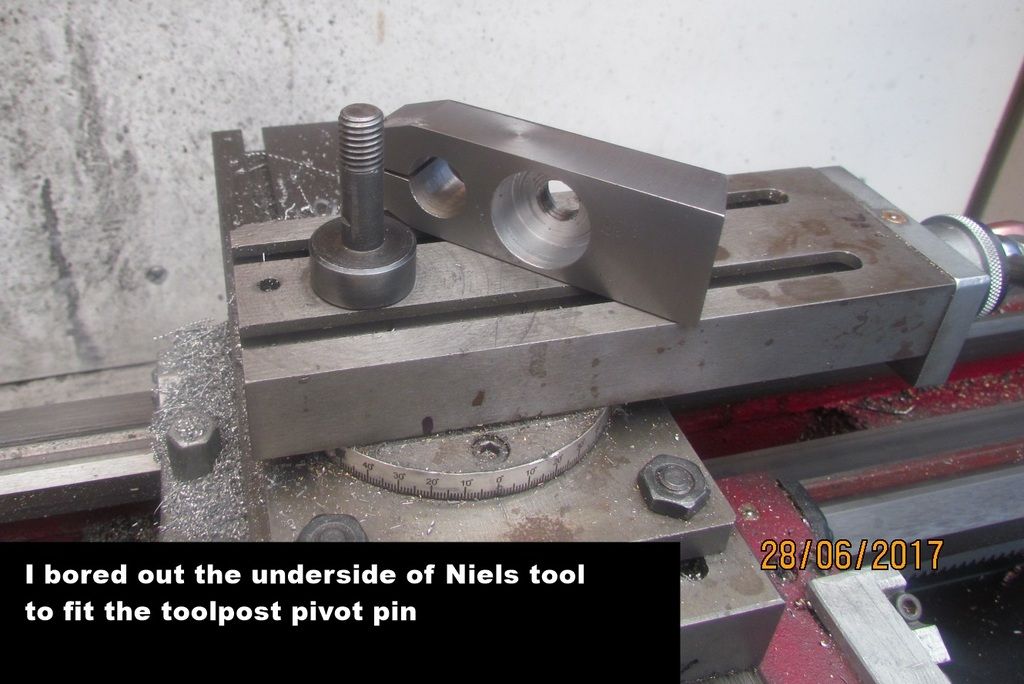
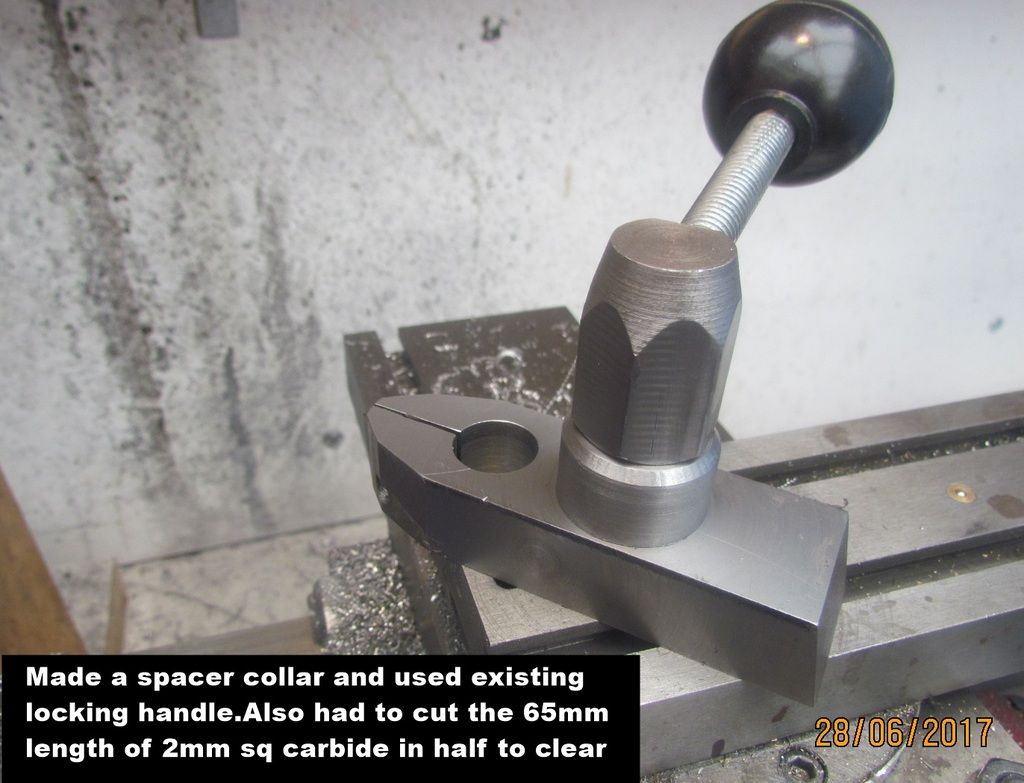
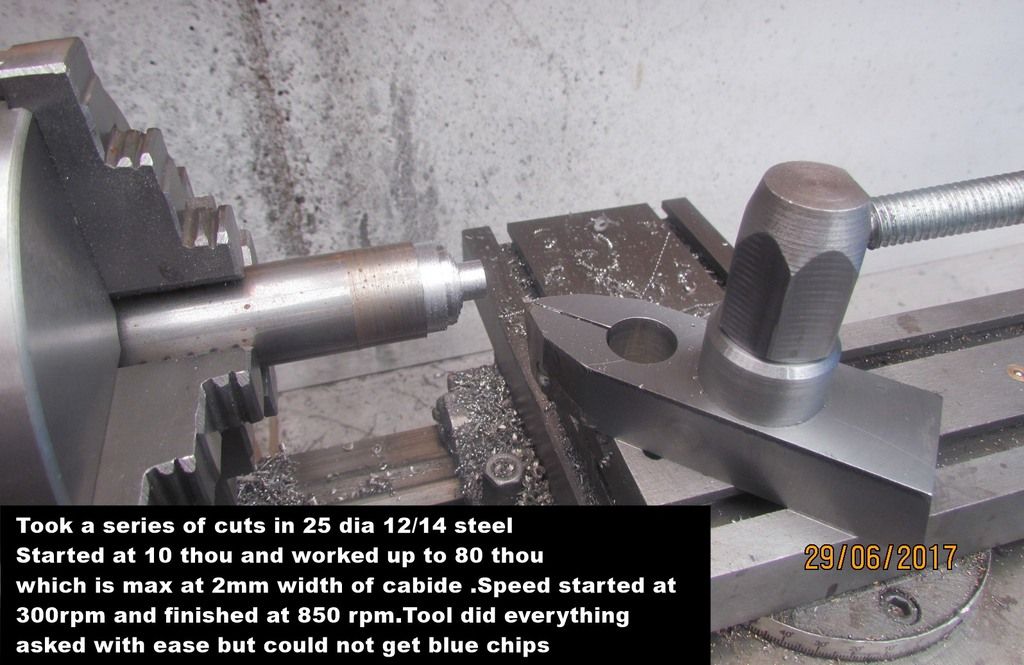
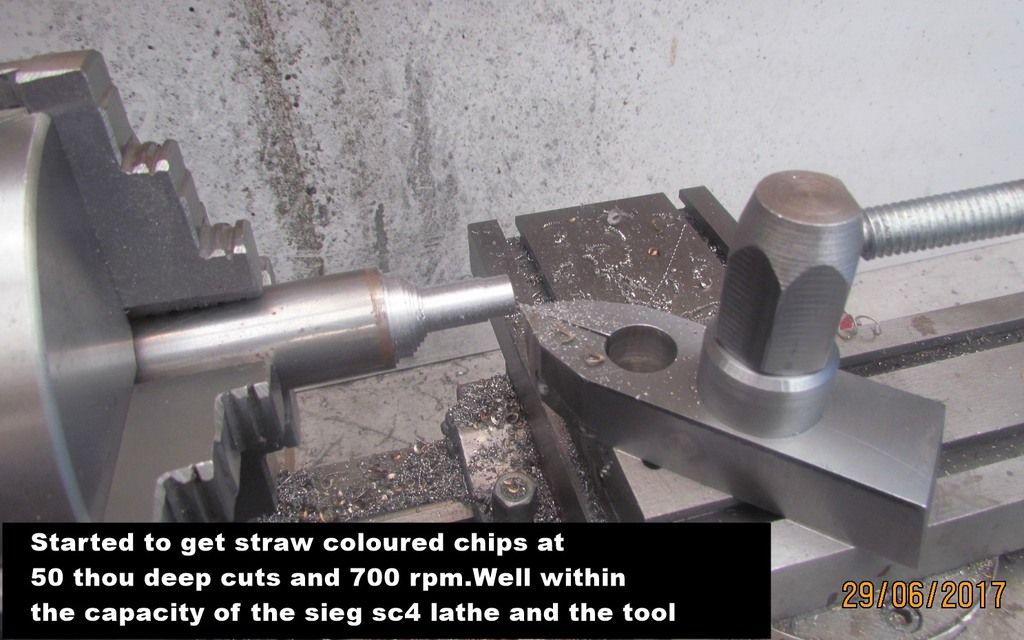
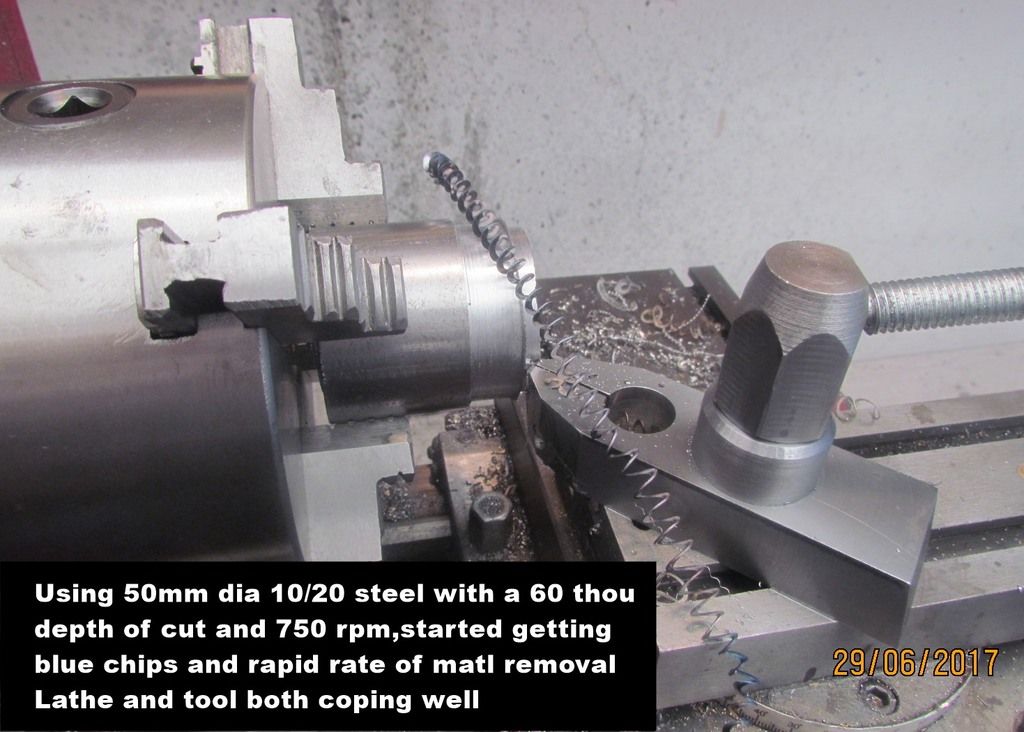
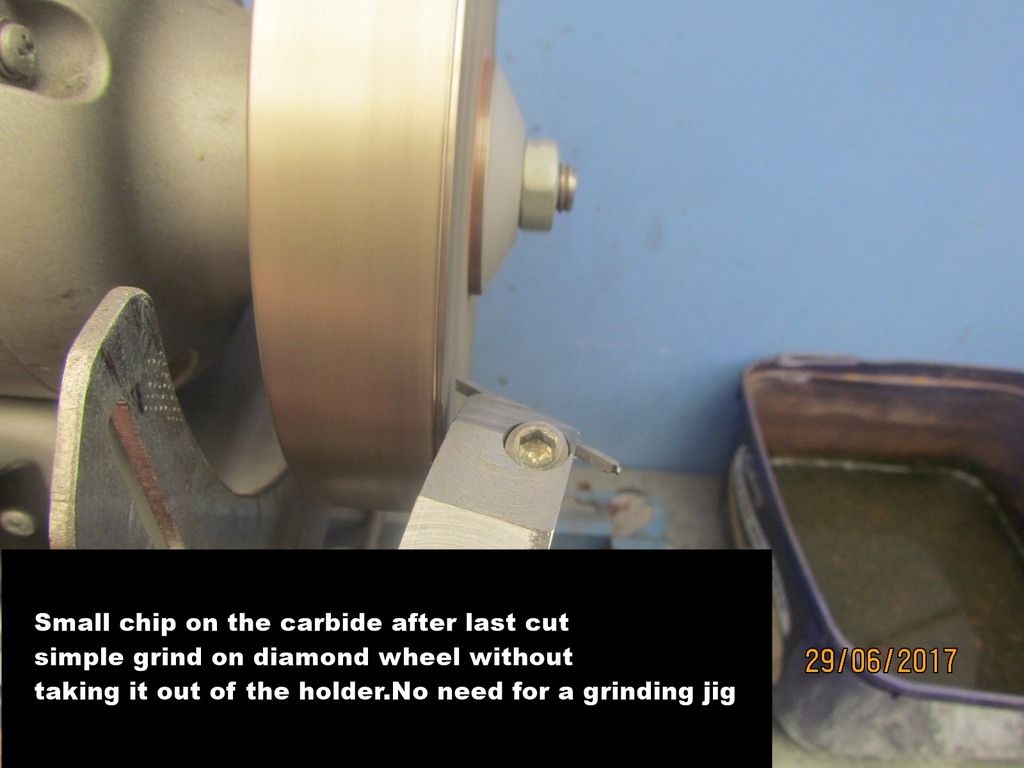
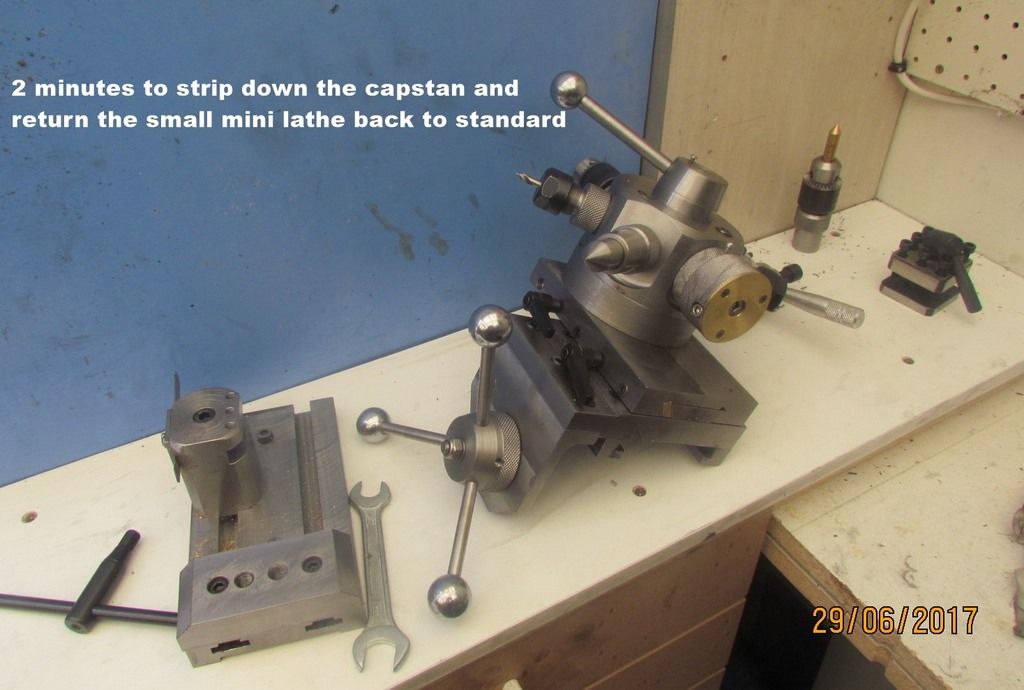
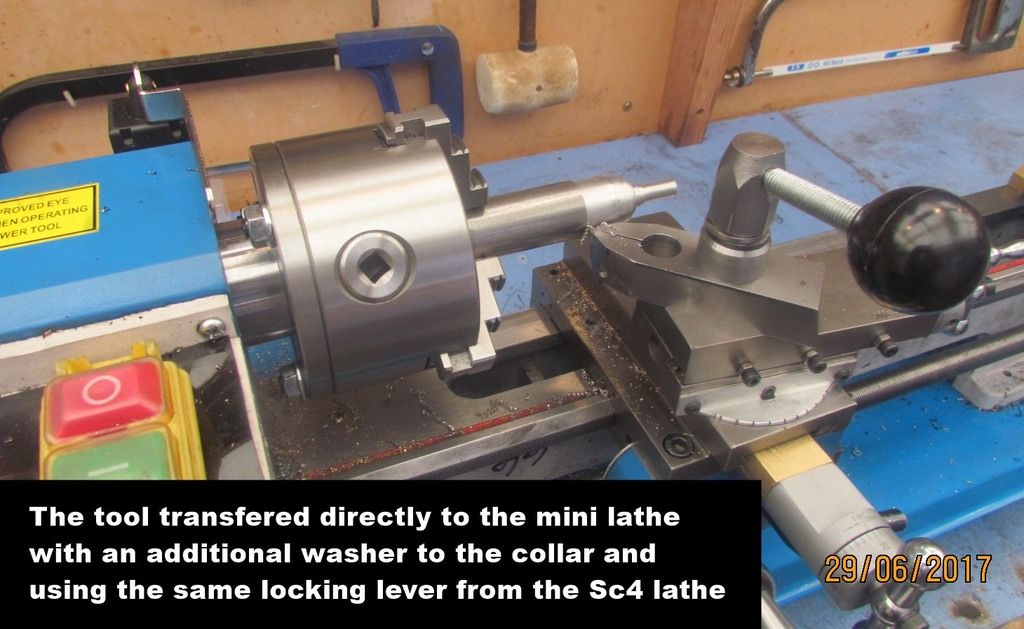