deere_x475guy
Well-Known Member
Well I finally got some time to get back into the shop this evening. Task at hand was to counter bore the head I am making for the my Webster engine. The 4-40 heads are approximately .215 and the only end mill I have that was large enough is .250. Not wanting to go that large I decided to try to make my own from a M42 drill I had laying around that miked out around .233. I am lucky enough to have a end mill sharpening fixture and a surface grinder. While I have sharpened plenty of end mills I never tried to make one from a drill before. It turned out ok and did the job, however if I am going to use this one again I need to shorten it up. I ended up with some chatter and I am sure it is due to the lack of rigidity from the length. Any where I know how you guys like pics so here are a few.
Hopefully I will have something to post in the progress area soon...
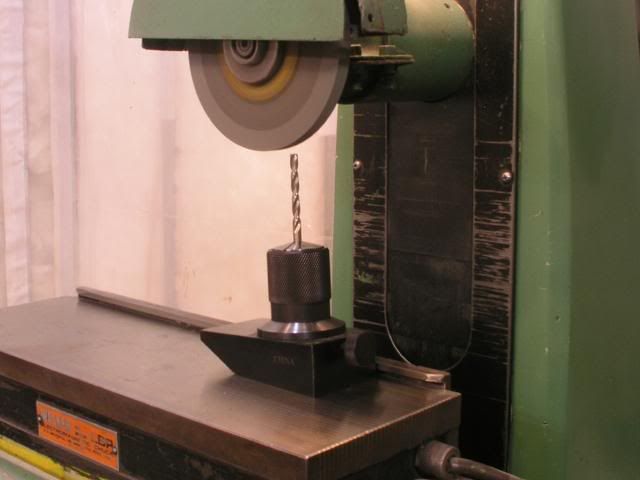
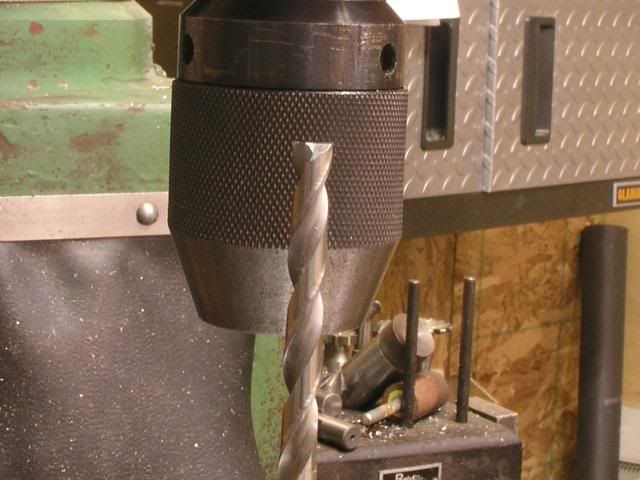
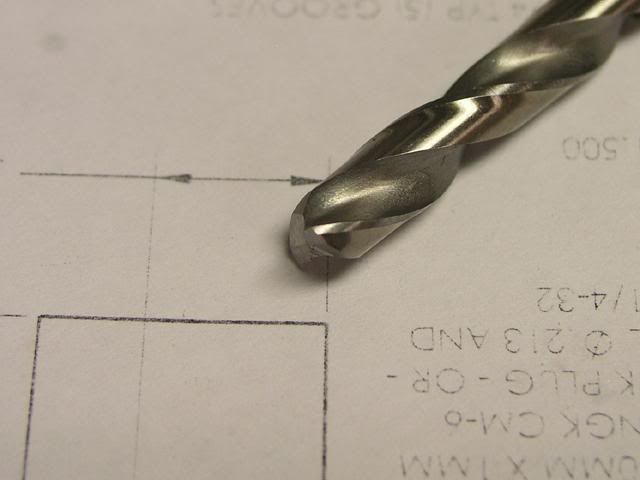
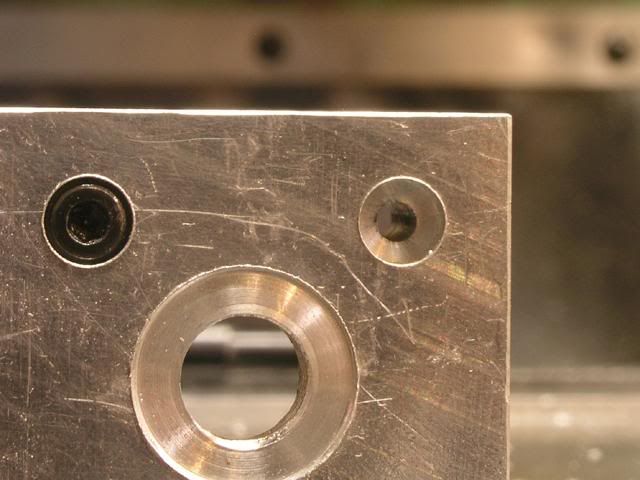
Hopefully I will have something to post in the progress area soon...