Metal Mickey
Well-Known Member
- Joined
- Jul 5, 2008
- Messages
- 612
- Reaction score
- 6
I have at last started on the refurbishment of my speculative purchase of a Myford ML7 lathe on eBay last February. With the recent sale of my Myford ML10 I had the space for the lathe to go into and the funds to carry out the refurbishment and upgrade.
My intention is to have a Myford with variable speed motor and digital readouts that will outlast me. Time will tell.
Today it was back to the paint brush and a bit of a surprise. The high quality paint brush I had been using did ok, but I thought the paint lay on a little thick at times. Today, because of the smaller mature of the items to paint, I got out a smaller artist type brush from a cheap set bought on the internet. The surprise was in the quality of finish. The cheap artist brush was gave a far better finish!
Yesterday I ordered the new electric motor, inverter and remote control and today it arrived! Good service so far. The package
also included three electric cables and some end fittings so a little study will be needed before it all goes together. I will let you
know how it goes.
The latest edition of Model Engineering Workshop arrived yesterday and included an article of a rev counter that seems a
possibility for the ML7. Again if I go ahead with making one I will let you know how I get on.
After the excitement of unpacking the new motor I then hunted around for the pulley that fitted the old motor. Needless to say
the bore of the pulley didn't match the new motor but fortunately the shaft is larger than the bore so its just a case of boring out the pulley and cut a keyway. Something I have yet to do.
With so many parts laid out around the workshop drying and the new motor unpacked, I thought it was time for a cup of tea, and a new list of action points. So the following list is the next phase of the refurbishment. I will let you know how I get on.
I am now waiting for some handles from RDG Tools online and various items for Myford themselves.
I must be honest I am really enjoying this refurbishment project, surprisingly so. I am treating the ML7 as a big set of castings and it's a good way to look ait I think. More to follow ..
List of actions for Myford ML7 refurbishment 20th January 2009
1. Machine up an new counter shaft
2. Machine up a new leadscrew front shaft
3. Machine new phosphor bushes for leadscrew
4. Make new drawers for lathe bench
5. Make a sheet steel back and side plate for lathe bench
6. Make two raised blocks for lathe to stand on
7. Paint remaining front part of lathe bench with black hammerite
8. Make and fit front door to bench (either wood or sheet metal)
9. Make and fit shelves for lathe bench
10. Bore out and cut a keyway for new lathe motor
11. Make the rollers for the bench drawers to fit on
12. Fly cut top slide tool post area
13. Clean up and paint the leadscrew right hand side handle
14. Wire up and fit new electric motor
15. Wire up and fit new inverter
16. Wire up and fit remote (after giving some thought to position)
17. Check eBay for the following (new or good secondhand):-
a. Rear tailstock handle
b. Long cross slide
I will let you know how I get on.......and here are some pictures of the 'before' bit.....
The variable speed package........
I need to bore out the pulley...................
My intention is to have a Myford with variable speed motor and digital readouts that will outlast me. Time will tell.
Today it was back to the paint brush and a bit of a surprise. The high quality paint brush I had been using did ok, but I thought the paint lay on a little thick at times. Today, because of the smaller mature of the items to paint, I got out a smaller artist type brush from a cheap set bought on the internet. The surprise was in the quality of finish. The cheap artist brush was gave a far better finish!
Yesterday I ordered the new electric motor, inverter and remote control and today it arrived! Good service so far. The package
also included three electric cables and some end fittings so a little study will be needed before it all goes together. I will let you
know how it goes.
The latest edition of Model Engineering Workshop arrived yesterday and included an article of a rev counter that seems a
possibility for the ML7. Again if I go ahead with making one I will let you know how I get on.
After the excitement of unpacking the new motor I then hunted around for the pulley that fitted the old motor. Needless to say
the bore of the pulley didn't match the new motor but fortunately the shaft is larger than the bore so its just a case of boring out the pulley and cut a keyway. Something I have yet to do.
With so many parts laid out around the workshop drying and the new motor unpacked, I thought it was time for a cup of tea, and a new list of action points. So the following list is the next phase of the refurbishment. I will let you know how I get on.
I am now waiting for some handles from RDG Tools online and various items for Myford themselves.
I must be honest I am really enjoying this refurbishment project, surprisingly so. I am treating the ML7 as a big set of castings and it's a good way to look ait I think. More to follow ..
List of actions for Myford ML7 refurbishment 20th January 2009
1. Machine up an new counter shaft
2. Machine up a new leadscrew front shaft
3. Machine new phosphor bushes for leadscrew
4. Make new drawers for lathe bench
5. Make a sheet steel back and side plate for lathe bench
6. Make two raised blocks for lathe to stand on
7. Paint remaining front part of lathe bench with black hammerite
8. Make and fit front door to bench (either wood or sheet metal)
9. Make and fit shelves for lathe bench
10. Bore out and cut a keyway for new lathe motor
11. Make the rollers for the bench drawers to fit on
12. Fly cut top slide tool post area
13. Clean up and paint the leadscrew right hand side handle
14. Wire up and fit new electric motor
15. Wire up and fit new inverter
16. Wire up and fit remote (after giving some thought to position)
17. Check eBay for the following (new or good secondhand):-
a. Rear tailstock handle
b. Long cross slide
I will let you know how I get on.......and here are some pictures of the 'before' bit.....
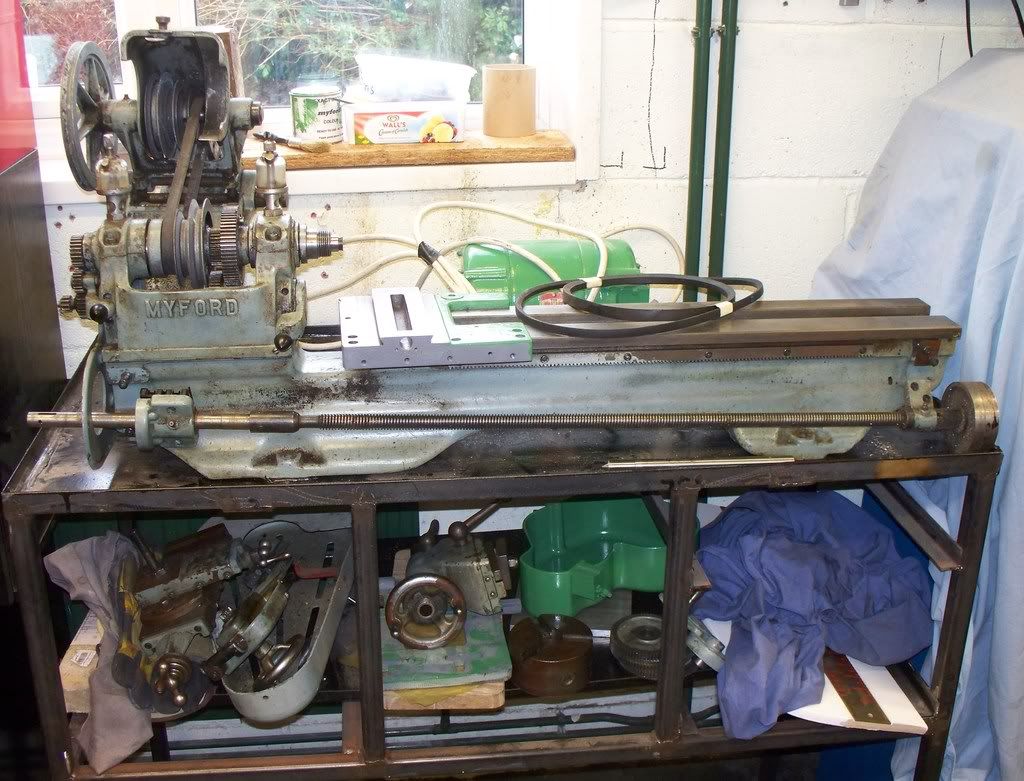
The variable speed package........
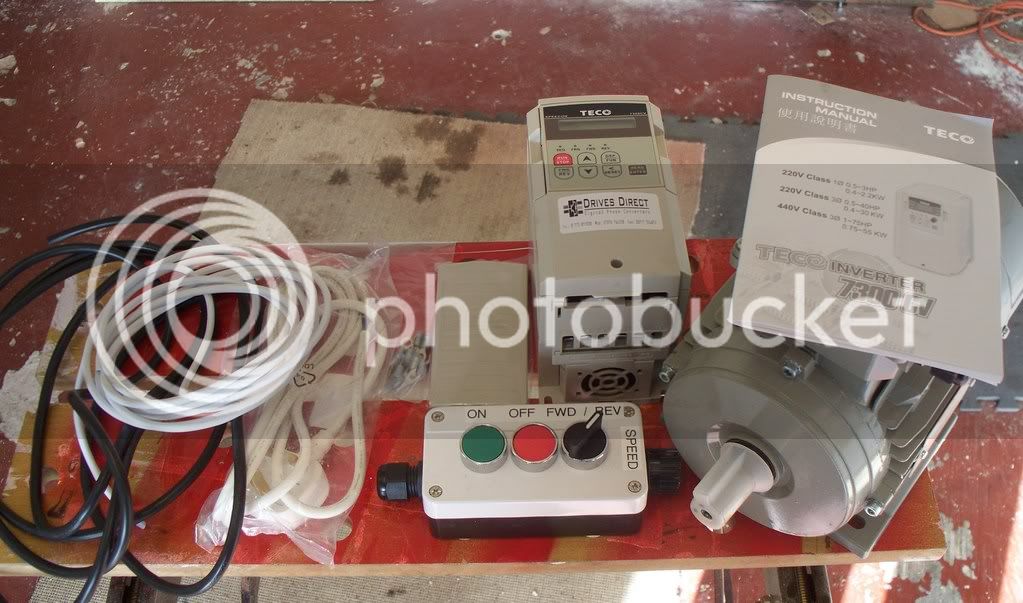
I need to bore out the pulley...................
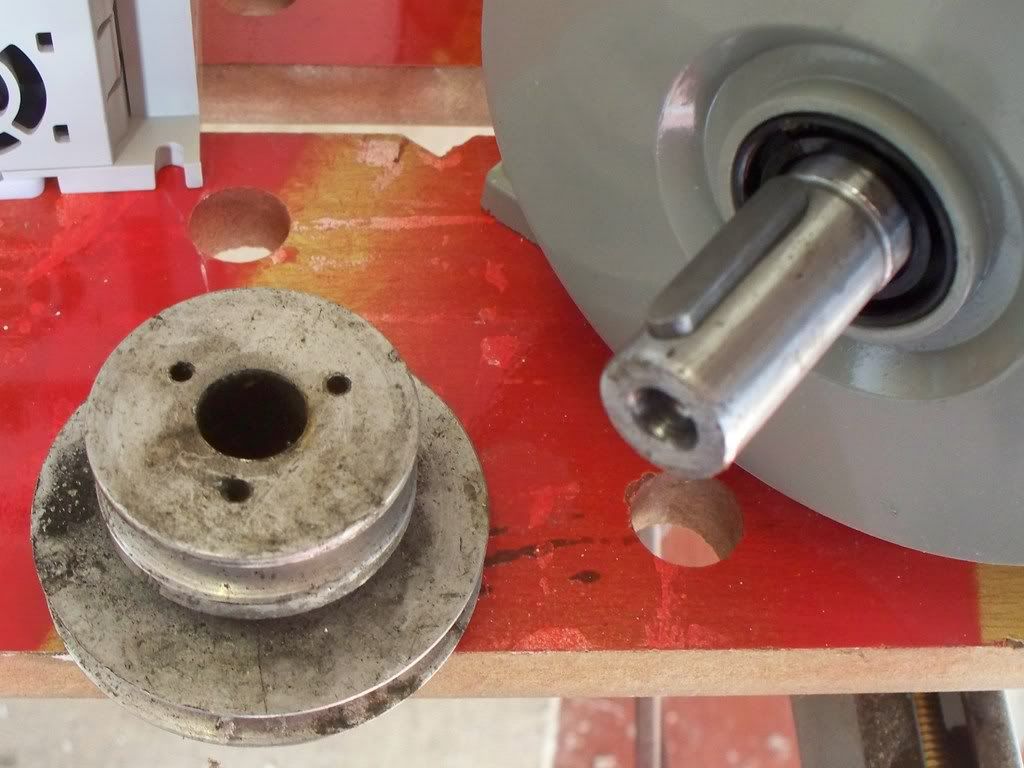