rudydubya
Well-Known Member
- Joined
- Nov 26, 2008
- Messages
- 337
- Reaction score
- 7
When I'm drilling a hole with my mini-lathe, I like to apply a little pressure on the tailstock quill lock to keep the quill more stable while I'm advancing or retracting the drill. But maintaining an even pressure on my machine was something of an art, because the friction on the quill changed depending on the position of the quill (some wear issues, I assume), requiring constant monitoring and adjustment, by feel, of the lock lever. I finally added a lock washer underneath the quill lock lever to introduce some variable spring pressure on the quill lock. I can now adjust the quill lock pressure on the quill from just a little to completely locked by adjusting the lock lever. I filed off the sharp edges of the washer ends a little so it wouldn't dig into the bottom of the lock lever when I was loosening the lock. Simple and cheap. Works pretty good for me.
Rudy
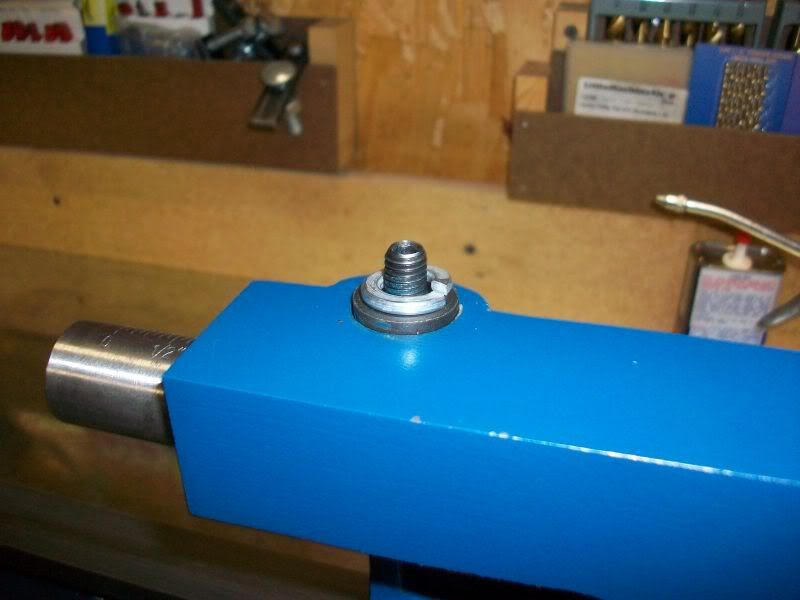
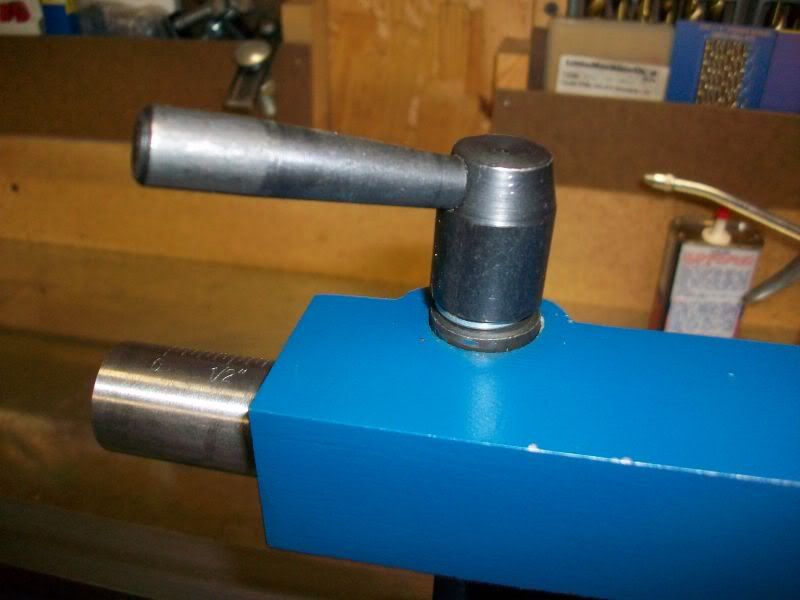
Rudy