My imported milling machine (Busy Bee CT129) has a provision for setting "stops" on the left/right travel of the table (shown in highlighted circles). I find them very handy, and use them a fair bit. The only problem is that the machine has no provisions made for travel stops on the Y axis of the table, front to rear. In my continuing saga of trying to keep myself occupied until I get some "real work" I have decided to design and build some "adjustable stops" for the Y axis travel of my mill.
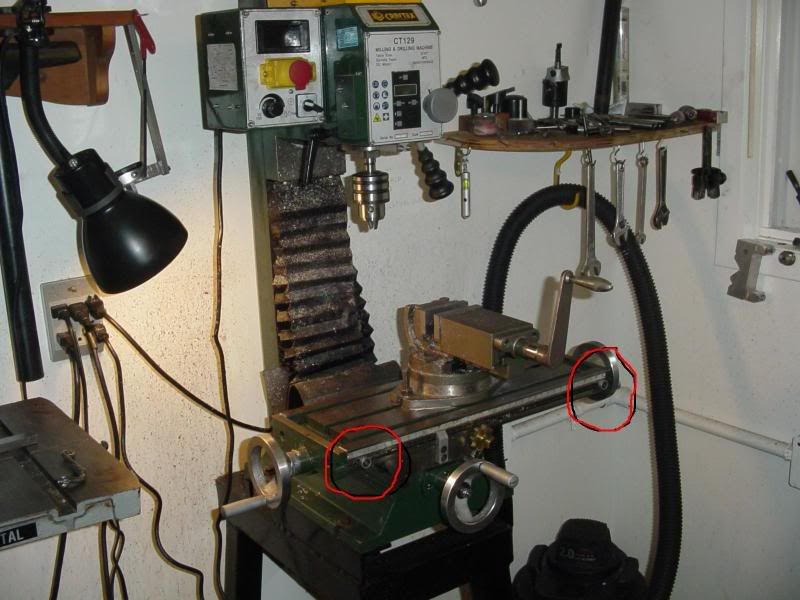