- Joined
- Feb 17, 2008
- Messages
- 2,326
- Reaction score
- 440
All the precision fit parts are done, although there will be some fiddly little parts in the fuel system.
Continuing upward, the cylinder heads are next. They are mostly a straight turning job, and since all the top end sealing is done by the contra piston they don't even need to be gas tight.
Started off with one inch diameter 6061 aluminum bar stock in the lathe. Turned the three diameters down and then cleaned out the tool tip radius where the meets the cylinder so the head would seat on the top of the cylinder. A 0.005 or 0.010 chamfer on the top of the cylinder would have eased this requirement some.
Head is cut off, leaving a few thou for cleanup to thickness, and everything repeated for the second head. Then the head is reversed in the lathe and the top is faced off bringing the head to the finished thickness.
Center drill, drill, tap 10-32 and knock off the burr with a hand held countersink.
After indicating the head to locate the center, the mounting holes were coordinate drilled on the milling machine. I did not center drill, but mounted the drill in a ER collet with only about 1/2 inch protruding. This is stiff enough when drilling aluminum that no center drilling is needed. Both sides of the holes were deburred with a small hand held countersink, then back to the lathe where a slight chamfer was put on the outside edge with a file and the part sanded with 800 and 1200 grit abrasive paper and hit with just a little bit of metal polish. The chamfer has to be small to keep it from going under the mounting screw heads.
And a finished pair of heads.
Gail in NM
Continuing upward, the cylinder heads are next. They are mostly a straight turning job, and since all the top end sealing is done by the contra piston they don't even need to be gas tight.
Started off with one inch diameter 6061 aluminum bar stock in the lathe. Turned the three diameters down and then cleaned out the tool tip radius where the meets the cylinder so the head would seat on the top of the cylinder. A 0.005 or 0.010 chamfer on the top of the cylinder would have eased this requirement some.
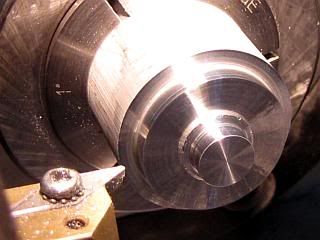
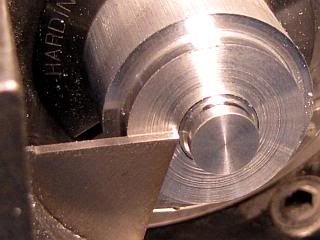
Head is cut off, leaving a few thou for cleanup to thickness, and everything repeated for the second head. Then the head is reversed in the lathe and the top is faced off bringing the head to the finished thickness.
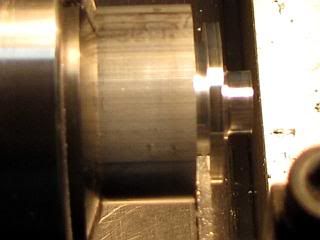
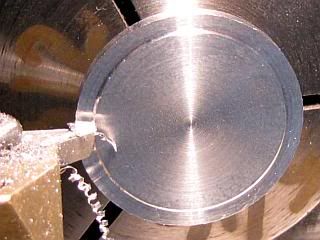
Center drill, drill, tap 10-32 and knock off the burr with a hand held countersink.
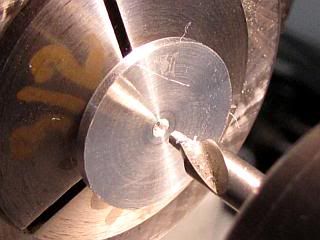
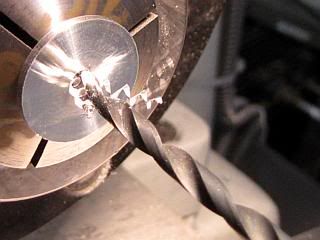
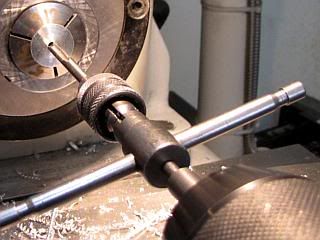
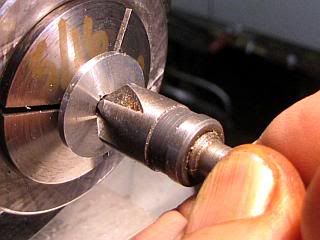
After indicating the head to locate the center, the mounting holes were coordinate drilled on the milling machine. I did not center drill, but mounted the drill in a ER collet with only about 1/2 inch protruding. This is stiff enough when drilling aluminum that no center drilling is needed. Both sides of the holes were deburred with a small hand held countersink, then back to the lathe where a slight chamfer was put on the outside edge with a file and the part sanded with 800 and 1200 grit abrasive paper and hit with just a little bit of metal polish. The chamfer has to be small to keep it from going under the mounting screw heads.
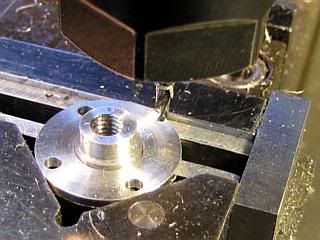
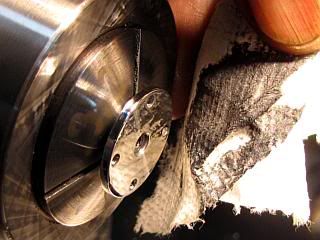
And a finished pair of heads.
Gail in NM
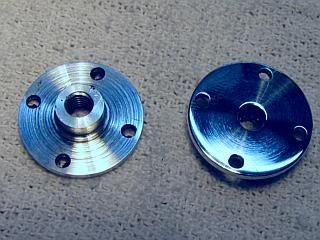